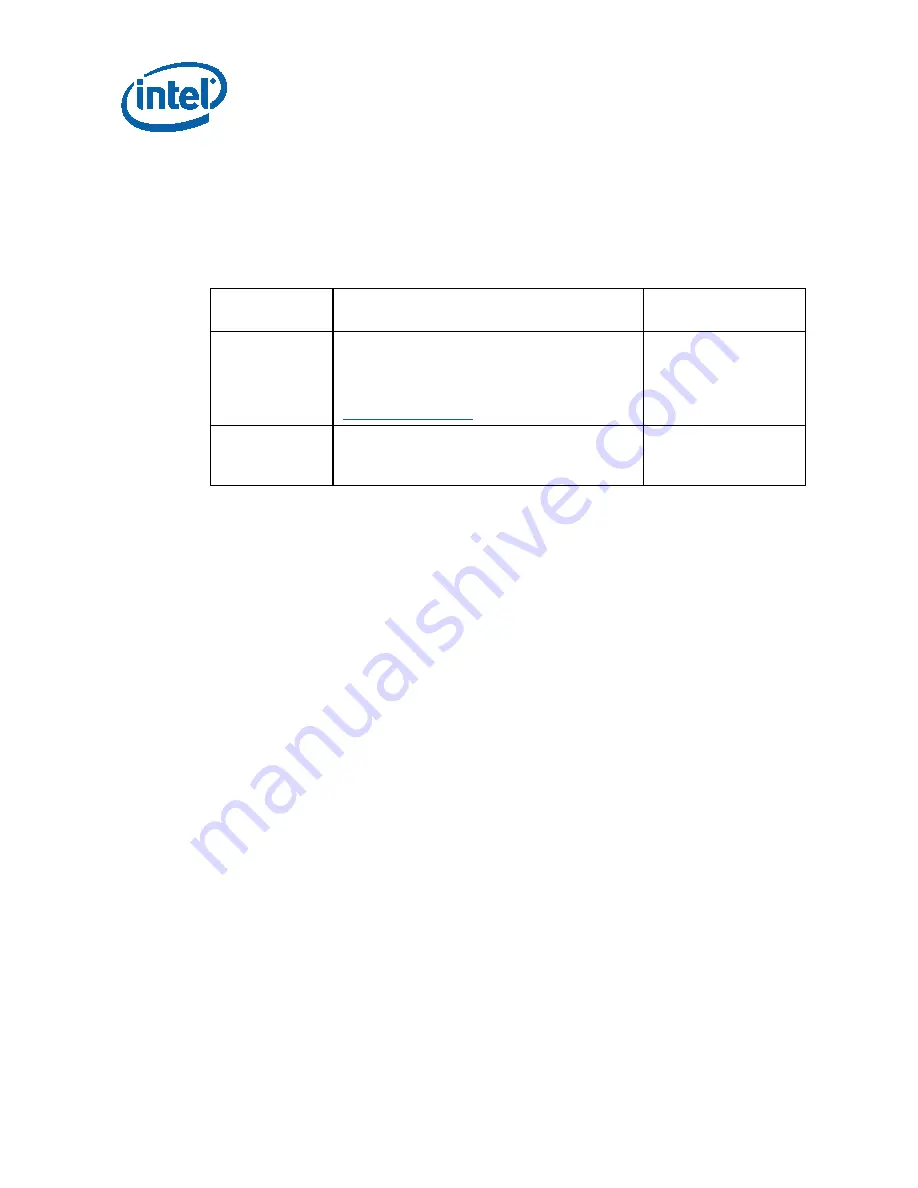
Heatsink Clip Load Metrology
78
Thermal and Mechanical Design Guidelines
B.2.2
Typical Test Equipment
For the heatsink clip load measurement, use equivalent test equipment to the one
listed in Table 7–2.
Table 7–2. Typical Test Equipment
Item
Description
Part Number
(Model)
Load cell
Notes: 1, 5
Honeywell*-Sensotec* Model 13 subminiature
load cells, compression only
Select a load range depending on load level
being tested.
Data Logger (or
scanner)
Notes: 2, 3, 4
Vishay* Measurements Group Model 6100
scanner with a 6010A strain card (one card
required per channel).
Model 6100
NOTES:
1.
Select load range depending on expected load level. It is usually better, whenever
possible, to operate in the high end of the load cell capability. Check with your load cell
vendor for further information.
2.
Since the load cells are calibrated in terms of mV/V, a data logger or scanner is
required to supply 5 volts DC excitation and read the mV response. An
automated model will take the sensitivity calibration of the load cells and convert the
mV output into pounds.
3.
With the test equipment listed above, it is possible to automate data recording and
control with a 6101-PCI card (GPIB) added to the scanner, allowing it to be connected
to a PC running LabVIEW* or Vishay's StrainSmart* software.
4.
IMPORTANT
: In addition to just a zeroing of the force reading at no applied load, it is
important to calibrate the load cells against known loads. Load cells tend to drift.
Contact your load cell vendor for calibration tools and procedure information.
5.
When measuring loads under thermal stress (bake for example), load cell thermal
capability must be checked, and the test setup must integrate any hardware used along
with the load cell. For example, the Model 13 load cells are temperature compensated
up to 71° C, as long as the compensation package (spliced into the load cell's wiring) is
also placed in the temperature chamber. The load cells can handle up to 121° C
(operating), but their uncertainty increases according to 0.02% rdg/°F.
B.3
Test Procedure Examples
The following sections provide two examples of load measurement. However, this is
not meant to be used in mechanical shock and vibration testing.
Any mechanical device used along with the heatsink attach mechanism will need to be
included in the test setup (that is, back plate, attach to chassis, and so forth).
Prior to any test, make sure that the load cell has been calibrated against known
loads, following load cell vendor’s instructions.
Содержание CELERON PROCESSOR E3000 - THERMAL AND MECHANICAL DESIGN
Страница 24: ...Processor Thermal Mechanical Information 24 Thermal and Mechanical Design Guidelines ...
Страница 80: ...Heatsink Clip Load Metrology 80 Thermal and Mechanical Design Guidelines ...
Страница 82: ...Thermal Interface Management 82 Thermal and Mechanical Design Guidelines ...
Страница 106: ...Balanced Technology Extended BTX System Thermal Considerations 106 Thermal and Mechanical Design Guidelines ...
Страница 108: ...Fan Performance for Reference Design 108 Thermal and Mechanical Design Guidelines ...
Страница 120: ...Mechanical Drawings 120 Thermal and Mechanical Design Guidelines Figure 7 50 Reference Fastener Sheet 1 ...
Страница 121: ...Mechanical Drawings Thermal and Mechanical Design Guidelines 121 Figure 7 51 Reference Fastener Sheet 2 ...
Страница 122: ...Mechanical Drawings 122 Thermal and Mechanical Design Guidelines Figure 7 52 Reference Fastener Sheet 3 ...
Страница 123: ...Mechanical Drawings Thermal and Mechanical Design Guidelines 123 Figure 7 53 Reference Fastener Sheet 4 ...