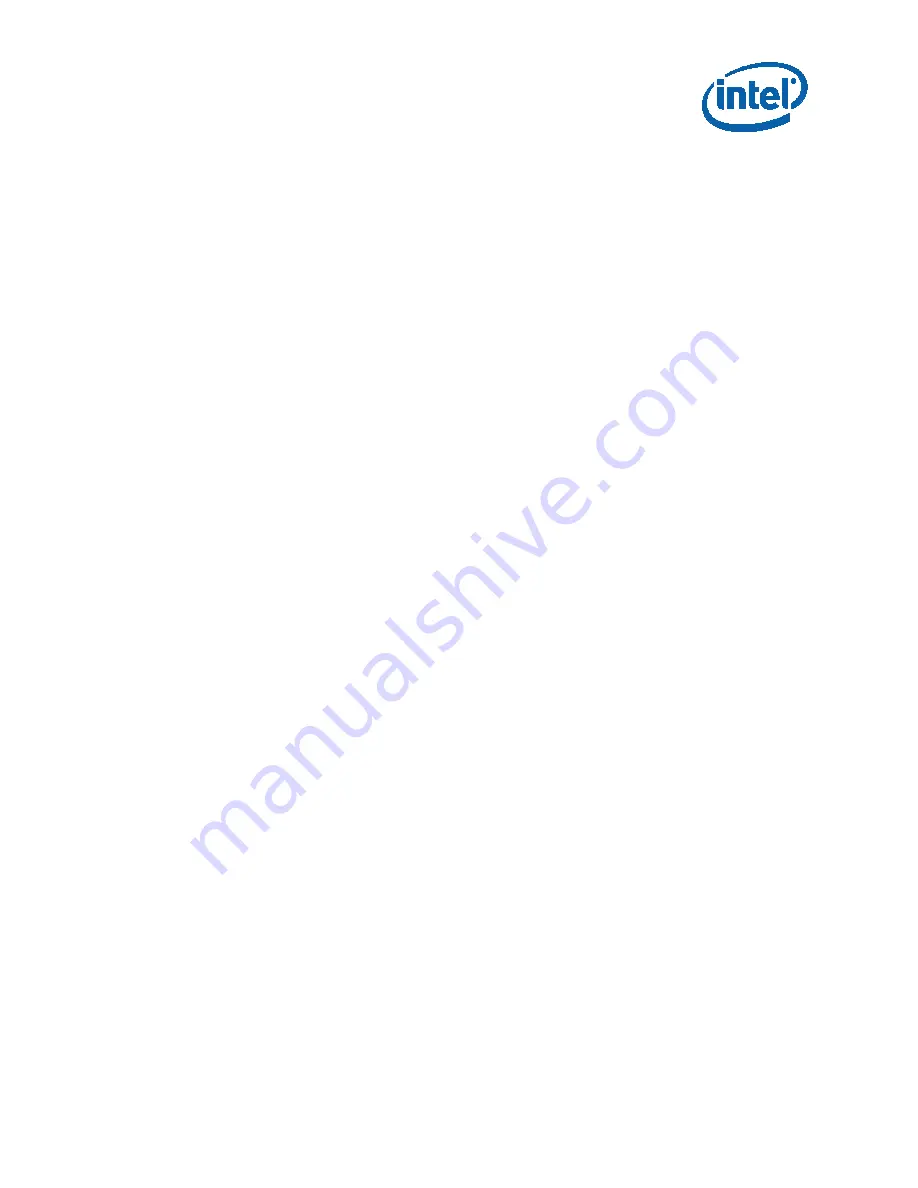
Processor Thermal/Mechanical Information
Thermal and Mechanical Design Guidelines
21
The recommended maximum heatsink mass for the ATX thermal solution is 550g. This
mass includes the fan and the heatsink only. The attach mechanism (clip, fasteners,
and so forth) are not included.
The mass limit for BTX heatsinks that use Intel reference design structural ingredients
is 900 grams. The BTX structural reference component strategy and design is
reviewed in depth in the latest version of the
Balanced Technology Extended (BTX)
System Design Guide.
Note:
The 550g mass limit for ATX solutions is based on the capabilities of the reference
design components that retain the heatsink to the board and apply the necessary
preload. Any reuse of the clip and fastener in derivative designs should not exceed
550g. ATX Designs that have a mass of greater than 550g should analyze the preload
as discussed in Appendix A and retention limits of the fastener.
Note:
The chipset components on the board are affected by processor heatsink mass.
Exceeding these limits may require the evaluation of the chipset for shock and
vibration.
2.3.3
Package IHS Flatness
The package IHS flatness for the product is specified in the datasheet and can be used
as a baseline to predict heatsink performance during the design phase.
Intel recommends testing and validating heatsink performance in full mechanical
enabling configuration to capture any impact of IHS flatness change due to combined
socket and heatsink loading. While socket loading alone may increase the IHS
warpage, the heatsink preload redistributes the load on the package and improves the
resulting IHS flatness in the enabled state.
2.3.4
Thermal Interface Material
Thermal interface material application between the processor IHS and the heatsink
base is generally required to improve thermal conduction from the IHS to the
heatsink. Many thermal interface materials can be pre-applied to the heatsink base
prior to shipment from the heatsink supplier and allow direct heatsink attach, without
the need for a separate thermal interface material dispense or attach process in the
final assembly factory.
All thermal interface materials should be sized and positioned on the heatsink base in
a way that ensures the entire processor IHS area is covered. It is important to
compensate for heatsink-to-processor attach positional alignment when selecting the
proper thermal interface material size.
When pre-applied material is used, it is recommended to have a protective application
tape over it. This tape must be removed prior to heatsink installation.
Содержание CELERON PROCESSOR E3000 - THERMAL AND MECHANICAL DESIGN
Страница 24: ...Processor Thermal Mechanical Information 24 Thermal and Mechanical Design Guidelines ...
Страница 80: ...Heatsink Clip Load Metrology 80 Thermal and Mechanical Design Guidelines ...
Страница 82: ...Thermal Interface Management 82 Thermal and Mechanical Design Guidelines ...
Страница 106: ...Balanced Technology Extended BTX System Thermal Considerations 106 Thermal and Mechanical Design Guidelines ...
Страница 108: ...Fan Performance for Reference Design 108 Thermal and Mechanical Design Guidelines ...
Страница 120: ...Mechanical Drawings 120 Thermal and Mechanical Design Guidelines Figure 7 50 Reference Fastener Sheet 1 ...
Страница 121: ...Mechanical Drawings Thermal and Mechanical Design Guidelines 121 Figure 7 51 Reference Fastener Sheet 2 ...
Страница 122: ...Mechanical Drawings 122 Thermal and Mechanical Design Guidelines Figure 7 52 Reference Fastener Sheet 3 ...
Страница 123: ...Mechanical Drawings Thermal and Mechanical Design Guidelines 123 Figure 7 53 Reference Fastener Sheet 4 ...