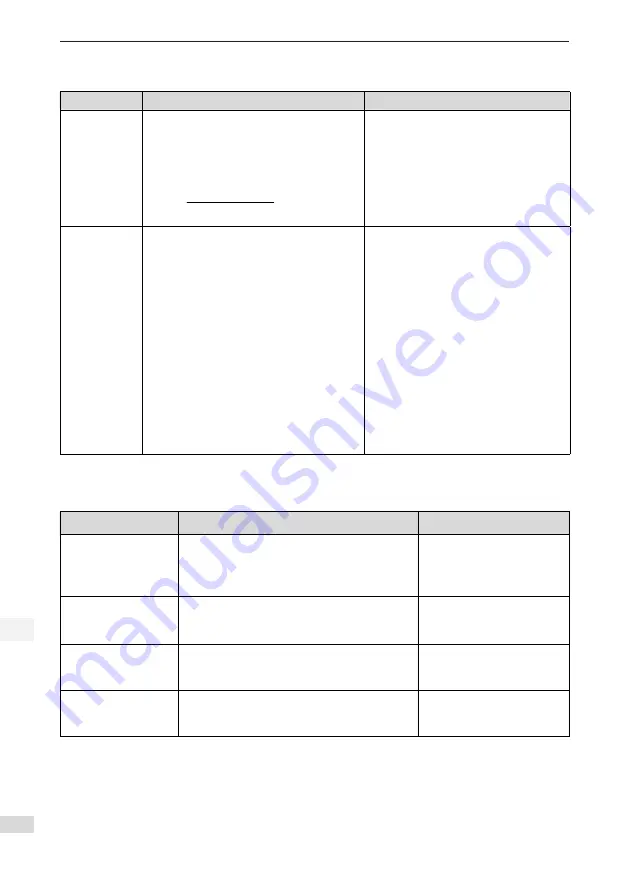
5 Troubleshooting
5
- 50 -
Er.510: Pulse output overspeed
Cause
Confirming Methods
Corrective Action
Output pulse
frequency
exceeds
frequency upper
limit allowed
by hardware (2
MHz).
When H05-38 = 0 (encoder frequency-division
output), calculate pulse frequency corresponding
to motor speed at occurrence of fault and check
whether the pulse frequency exceeds limit.
Output pulse frequency (Hz) =
Motor speed (rpm)
60
x H05-17
Decrease H05-17(Encoder frequency-
division pulses), making output pulse
frequency below frequency upper limit
allowed by hardware in the speed range
required by mechanical condition.
Output pulse
frequency
exceeds
frequency upper
limit allowed
by hardware (2
MHz).
When H05-38 = 1 (reference pulse synchronous
output), input pulse frequency exceeds 2 MHz or
interference exists on pulse input pin.
Low-speed pulse input pin:
Differential input terminals, PULSE+, PULSE-,
SIGN+, SIGN-
Max. pulse frequency: 500 kpps
Open-collector input terminals, PULLHI,
PULSE+, PULSE-, SIGN+, SIGN-
Max. pulse frequency: 200 kbps
High-speed pulse input pin:
Differential input terminals: ,
HPULSE-, HSIGN+, HSIGN-
Max. pulse frequency: 2 Mpps
Decrease input pulse frequency to within
frequency upper limit allowed by hardware.
In this case, if you do not modify electronic
gear ratio, motor speed will slow down.
If input pulse frequency is very high but is
still within frequency upper limit allowed by
hardware, take anti-interference measures
(use STP cable for pulse input and set pin
filter parameters H0A-24 or H0A-30), which
prevents interference pulse adding to pulse
and resulting in fault misreported.
Er.602: Angle auto-tuning failure
Er.610: Servo drive overload
Cause
Confirming Methods
Corrective Action
1. Parameter setting is
incorrect.
Check whether H01-02 (drive SN) is set correctly.
Check whether the gain parameters (group H08) or
the stiffness (H09-00 and H09-01) are set correctly.
Set H01-02 according to the
actual drive SN.
Adjust the parameters based
on the current feedback effect.
The servo drive load
ratio is too large (load
inertia excessive).
Check whether H0B-12 (average load ratio) is
excessive (over 80%) and then whether the inertia
is excessive through inertia auto-tuning.
Use a drive model of higher
power.
3. The servo drive
load ratio is too large
(mechanical stuck)
Check whether H0B-12 (average load ratio) is
excessive (over 80%) and then whether stuck
occurs during load running.
Eliminate the mechanical stuck
problem.
4. Locked rotor occurs
in the motor.
Check whether H0A-33 (locked rotor over-
temperature protection) is 0. If yes, the drive trips
Er.610 when locked rotor occurs.
Take actions for Er.630.
Содержание IS650P Series
Страница 1: ......
Страница 101: ...100 Revision History Date Version Change Description March 2017 A00 First issue...
Страница 102: ......