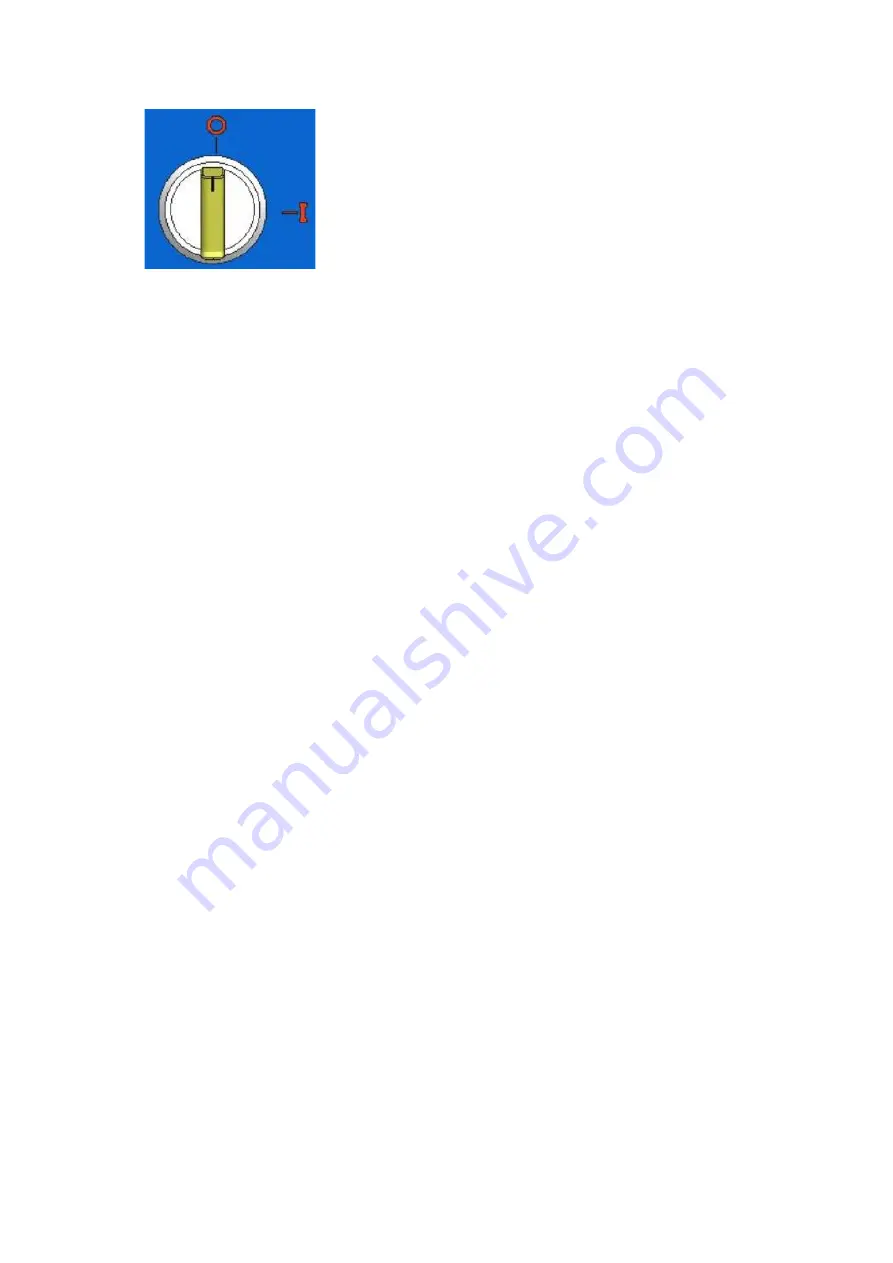
6. OPERATION
Turn the switch to
“1” position.
Turning on and off
the
machine
is
controlled
from
start-stop buttons
on
the
control
panel.
Turn On-off and START switches to “1”.
Machine will automatically start heating up once
the water is filled and water level goes up the
heaters.
Once the water is filled, machine will
automatically start washing.
Minimum and maximum water levels are
automatically controlled with a pressurestat
(pressure switch).
Washing starts once the baskets are provided by
the inlet counter and continues in 4 stages.
Respectively;
Pre-washing:
Part where the dishes are roughly
washed. This stage is provided by pumping the
water filtered twice and sucked in from the
sprinklers. Ideal washing water temperature for
this stage is 45-50
0
C'dir. Sprinklers are designed
to spray water on all surfaces of the dishes.
Washing:
Part where pre-washed dishes are
washed again. Ideal washing water temperature
in this stage is around 60
0
C. Circulation of the
water is provided through pumping the water
filtered twice and sucked through sprinklers.
Sprinklers are designed to spray water on all
surfaces of the dishes.
Rinsing:
This is the part where all cleaned
cutleries, glasses and plates are ideally rinsed and
sterilized. Rinsing is performed with 85
0
C water
coming from the boiler. Hot water in this
temperature also works as sterilizer. Rinsing
water reaches all surfaces to be rinsed. Boiler
heating power is calibrated considering the water
inlet temperature will be around 50
0
C. Boiler and
tank heaters are sized according to operating
environment in cold water inlets.
Drying:
In order to ensure the drying stage meets
all required standards;
Hard water should not be used in washing and
rinsing stages. Hard water leads to spots on dried
surfaces.
Water temperature in pre-washing and washing
stages should be as predetermined.
Use detergent and rinse aid in adequate amounts.
Water pressure in rinsing stage should be as
predetermined.
A mild humidity occurs on the surfaces of plates,
cutleries and glasses coming out of drying tunnel.
This is a temporary situation and will pass in a
couple of minutes. This humidity is caused by the
temperature
difference
between
the
hot
environment of drying tunnel and the cold
environment out of the machine.
Drying unit of the machine produces an ideal
drying operation provided that pre-washing,
washing and drying stages were completed in
accordance with the necessary standards.
NOTE: The machine will stop working if the
maintenance and cleaning lid in the mid-section
of the device is opened.
7. CLOSING
Bring the on-off switch of the machine to “0”.
Close water inlet valve.
Maintenance of the boiler and cleaning the boiler
by emptying the water in the boiler and in pipes
should periodically be made by authorized
personnel.
If the device will not be used for a while, all
surfaces should be coated with a thin layer of
Vaseline.
In case of detection of a dangerous situation in
the device, authorized technical service should
immediately be notified. Do not let unauthorized
personnel interfere.
STANDARD ACCESSORIES
500x500x100mm plate, cutlery and glass trays
are included in machine prices.
EXTRA ACCESSORIES
Inlet – outlet counters
Rinsing water pressure pump
Detergent and rinse aid pumps
Extra accessories are not included in machine price.
Содержание BKE2000L
Страница 2: ...2...
Страница 22: ...22 BKE 2000L R ELEKTR K EMASI ELECTRICAL SCHEDULE BKE 2000L R ELECTRICAL SCHEDULE...