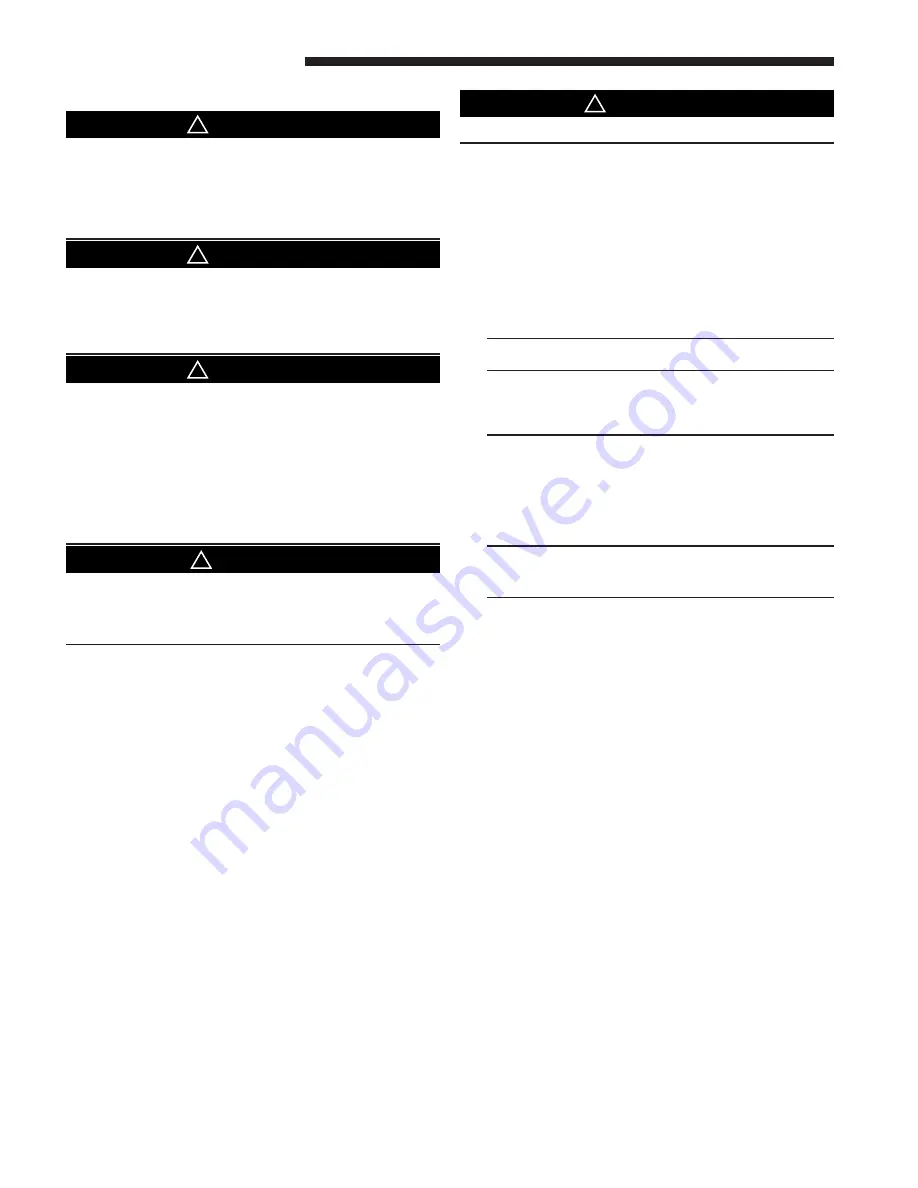
6
Service Facts
M952-SF-4
PERIODIC SERVICING REQUIREMENTS
▲
WARNING
!
ELECTRIC SHOCK HAZARD
DISCONNECT POWER TO THE UNIT BEFORE REMOVING
THE BLOWER DOOR. ALLOW A MINIMUM OF 15
SECONDS FOR IFC POWER SUPPLY TO DISCHARGE TO
0 VOLTS. FAILURE TO FOLLOW THIS WARNING COULD
RESULT IN PERSONAL INJURY FROM MOVING PARTS.
▲
WARNING
!
CARBON MONOXIDE POISONING HAZARD
FAILURE TO FOLLOW THE SERVICE AND/OR PERIODIC
MAINTENANCE INSTRUCTIONS FOR THE FURNACE
AND VENTING SYSTEM, COULD RESULT IN CARBON
MONOXIDE POISONING OR DEATH.
▲
WARNING
!
FIRE OR EXPLOSION HAZARD
FAILURE TO FOLLOW THE SAFETY WARNINGS EXACTLY
COULD RESULT IN SERIOUS INJURY, DEATH OR
PROPERTY DAMAGE.
NEVER TEST FOR GAS LEAKS WITH AN OPEN FLAME.
USE A COMMERCIALLY AVAILABLE SOAP SOLUTION
MADE SPECIFICALLY FOR THE DETECTION OF LEAKS
TO CHECK ALL CONNECTIONS. A FIRE OR EXPLOSION
MAY RESULT CAUSING PROPERTY DAMAGE, PERSONAL
INJURY, OR LOSS OF LIFE.
▲
CAUTION
!
Label all wires prior to disconnection when servicing
controls. Wiring errors can cause improper and
dangerous operation. Verify proper operation after
servicing.
1. GENERAL INSPECTION –
Examine the furnace
installation annually for the following items:
a. All flue product carrying areas external to the furnace
(i.e. chimney, vent connector) are clear and free of
obstruction. A vent screen in the end of the vent (flue)
pipe must be inspected for blockage annually.
b. The vent connector is in place, slopes upward and is
physically sound without holes or excessive corrosion.
c. The return air duct connection(s) is physically sound, is
sealed to the furnace and terminates outside the space
containing the furnace.
d. The physical support of the furnace should be sound
without sagging, cracks, gaps, etc., around the base so
as to provide a seal between the support and the base.
e. There are no obvious signs of deterioration of the
furnace.
2. FILTERS – Filters should be cleaned or replaced (with
high velocity filters only), monthly and more frequently
during high use times of the year such as midsummer or
midwinter.
3. BLOWERS – The blower size and speed determine
the air volume delivered by the furnace. The blower
motor bearings are factory lubricated and under normal
operating conditions do not require servicing. If motor
lubrication is required it should only be done by a qualified
servicer. Annual cleaning of the blower wheel and
housing is recommended for maximum air output, and this
must be performed only by a qualified servicer or service
agency.
▲
CAUTION
!
Do NOT touch igniter. It is extremely hot.
4. IGNITER – This unit has a hot surface direct ignition
device that automatically lights the burners. Please note
that it is very fragile and should be handled with care.
5. BURNER – Gas burners do not normally require
scheduled servicing, however, accumulation of foreign
material may cause a yellowing flame or delayed ignition.
Either condition indicates that a service call is required.
For best operation, burners must be cleaned annually
using brushes and vacuum cleaner.
Turn off gas and electric power supply. To clean burners,
remove burner box cover (6 to 8 screws) and top burner
bracket. Lift burners from orifices.
NOTE: Be careful not to break igniter when removing
burners.
Clean burners with brush and/or vacuum cleaner.
Reassemble parts by reversal of the above procedure.
The burner box must be resealed when replacing box
cover.
NOTE: On LP (propane) units, some light yellow
tipping of the outer mantle is normal. Inner mantle
should be bright blue.
Natural gas units should not have any yellow tipped
flames. This condition indicates that a service call
is required. For best operation, burners must be
cleaned annually using brushes and vacuum cleaner.
NOTE: On LP (propane) units, due to variations in
BTU content and altitude, servicing may be required
at shorter intervals.
6. HEAT EXCHANGER/FLUE PIPE – These items must be
inspected for signs of corrosion, and/or deterioration at
the beginning of each heating season by a qualified service
technician and cleaned annually for best operation. To
clean flue gas passages, follow recommendations below:
a. Turn off gas and electric power supply.
b. Inspect flue pipe exterior for cracks, leaks, holes or
leaky joints. Some discoloration of PVC pipe is normal.
c. Remove burner compartment door from furnace.
d. Inspect around insulation covering flue collector
box. Inspect induced draft blower connections from
recuperative cell and to the flue pipe connection.
e. Remove burners. (See Item 5.)
f. Use a mirror and flashlight to inspect interior of heat
exchanger, be careful not to damage the igniter, flame
sensor or other components.
g. If any corrosion is present the heat exchanger should
be cleaned by a qualified service technician.
h. After inspection is complete replace burner box cover,
burners, and furnace door.
i. Restore gas supply. Check for leaks using a soap
solution. Restore electrical supply. Check unit for
normal operation.
7. COOLING COIL CONDENSATE DRAIN – If a cooling
coil is installed with the furnace, condensate drains
should be checked and cleaned periodically to assure
that condensate can drain freely from coil to drain. If
condensate cannot drain freely water damage can
occur. (See Condensate Drain in Installer’s Guide)
Содержание M952V060BD36AB
Страница 7: ...7 Service Facts M952 SF 4 M952 WIRING DIAGRAM From drawing D345191P01...
Страница 8: ...8 Service Facts M952 SF 4 M952 SCHEMATIC DIAGRAM2 From drawing D345191P01...
Страница 9: ...9 Service Facts M952 SF 4 M952 WIRING DIAGRAM From drawing D345192...
Страница 10: ...10 Service Facts M952 SF 4 M952 SCHEMATIC DIAGRAM From drawing D345192...
Страница 37: ...37 Service Facts M952 SF 4...