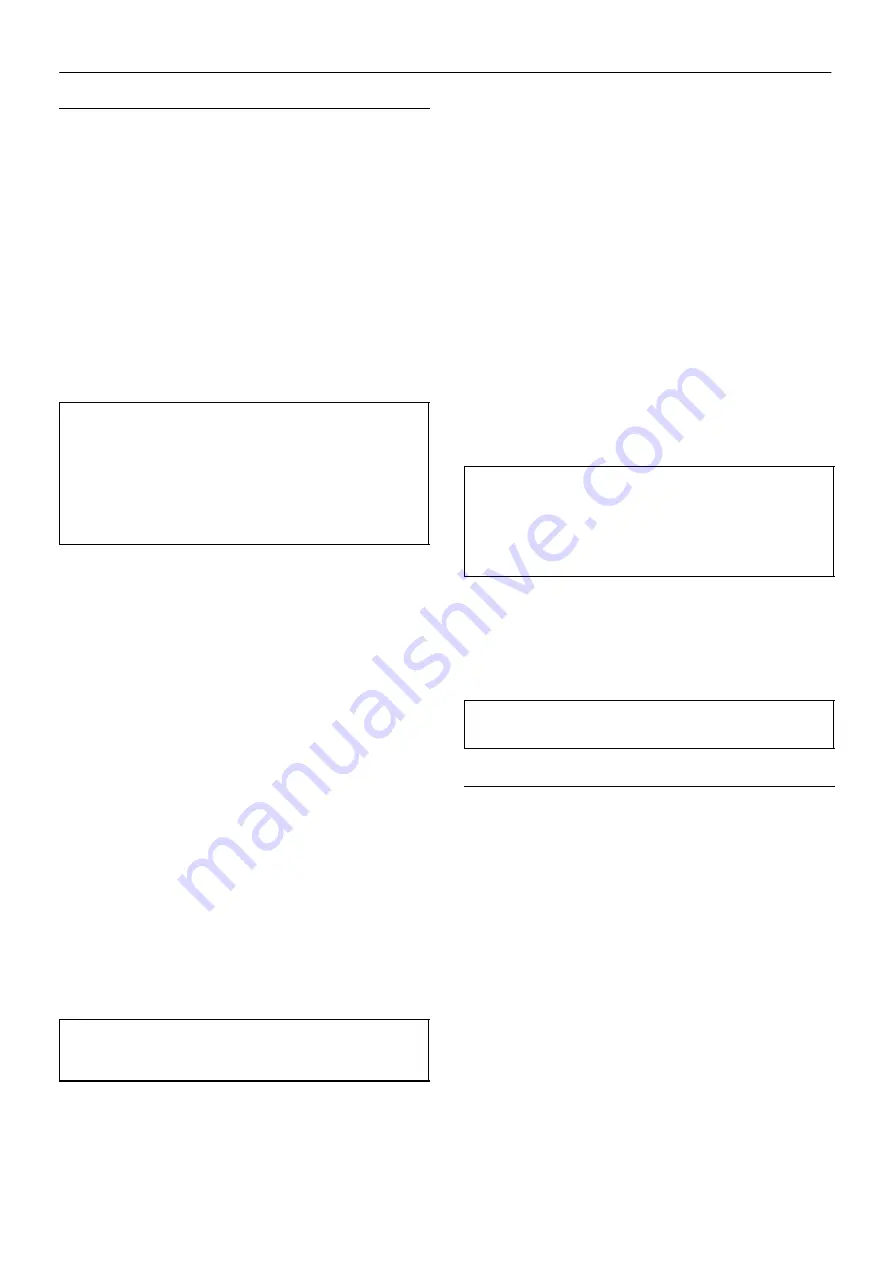
MAINTENANCE
30
IRN 7.5
−
15 HP (5.5
−
11 kW)
http://air.irco.com
ROUTINE MAINTENANCE
This section refers to the various components which require
periodic maintenance and replacement.
. It should be noted that the intervals between service requirement
may be significantly reduced as a consequence of poor operating
environment. This would include effects of atmospheric contamination
and extremes of temperature.
The
SERVICE/MAINTENANCE CHART
indicates the various
components’ descriptions and the intervals when maintenance has to
take place. Oil capacities, etc., can be found in the
GENERAL
INFORMATION
section of this manual.
Compressed air can be dangerous if incorrectly handled. Before
doing any work on the unit, ensure that all pressure is vented from the
system and that the machine cannot be started accidentally.
CAUTION: Before beginning any work on the compressor, open,
lock and tag the main electrical disconnect and close the isolation
valve on the compressor discharge. Vent pressure from the unit
by slowly unscrewing the coolant fill cap one turn. Unscrewing
the fill cap opens a vent hole, drilled in the cap, allowing pressure
to release to atmosphere. Do not remove the fill cap until all
pressure has vented from the unit. Also vent piping by slightly
opening the drain valve. When opening the drain valve or the
coolant fill cap, stand clear of the valve discharge and wear
appropriate eye protection.
Ensure that maintenance personnel are properly trained,
competent and have read the Maintenance Manuals.
Prior to attempting any maintenance work, ensure that:
−
. all air pressure is fully discharged and isolated from the system. If
the automatic blowdown valve is used for this purpose, then allow
enough time for it to complete the operation.
. the machine cannot be started accidentally or otherwise.
. all residual electrical power sources (mains and battery) are
isolated.
Prior to opening or removing panels or covers to work
inside
a machine, ensure that:
−
. anyone entering the machine is aware of the reduced level of
protection and the additional hazards, including hot surfaces and
intermittently moving parts.
. the machine cannot be started accidentally or otherwise.
Prior to attempting any maintenance work on a
running
machine, ensure that:
−
DANGER
Only properly trained and competent persons should
undertake any maintenance tasks with the compressor running or
with electrical power connected.
. the work carried out is limited to only those tasks which require the
machine to run.
. the work carried out with safety protection devices disabled or
removed is limited to only those tasks which require the machine to be
running with safety protection devices disabled or removed.
. all hazards present are known (e.g. pressurised components,
electrically live components, removed panels, covers and guards,
extreme temperatures, inflow and outflow of air, intermittently moving
parts, safety valve discharge etc.).
. appropriate personal protective equipment is worn.
. loose clothing, jewellery, long hair etc. is made safe.
. warning signs indicating that
Maintenance Work is in Progress
are
posted in a position that can be clearly seen.
Upon completion of maintenance tasks and prior to returning
the machine into service, ensure that:
−
. the machine is suitably tested.
. all guards and safety protection devices are refitted and correctly
working.
. all panels are replaced, canopy and doors closed.
. hazardous materials are effectively contained and disposed of in a
manner compliant with local or National environmental protection
codes.
WARNING
Do not under any circumstances open any drain valve or
remove components from the compressor without first ensuring
that the compressor is FULLY SHUT
−
DOWN, power isolated and
all air pressure relieved from the system.
Check dryer pressure gauge and vent dryer lines to zero
pressure before servicing.
TOP UP COOLANT PROCEDURE
The reservoir is designed to prevent overfill. With warm unit stopped
in the normal way, the sight glass level should be at the midpoint of the
glass. The level should not drop beyond the bottom of the sight glass
when running with a steady load.
CAUTION
Ensure that SSR ULTRA
−
PLUS coolant is used. Failure to do
so will void manufacturers warranty.
COOLANT CHANGE PROCEDURE
It is better to drain the coolant immediately after the compressor has
been operating as the liquid will drain more easily and any contaminant
will still be in suspension.
1. Stop the machine, electrically isolate and vent all trapped pressure.
2. Place a suitable container close to the drain valve.
3. Slowly remove fill/vent cap.
4. Remove plug from drain valve.
5. Open the drain valve and drain coolant into container.
6. Close the drain valve.
7. Replace plug in drain valve.
8. Refill the machine following the ”top up coolant” procedure above.
After initial fill, to purge any airlocks, the machine should be run for a
few minutes before checking that the level is correct.
9. Top up as needed after running for five minutes.