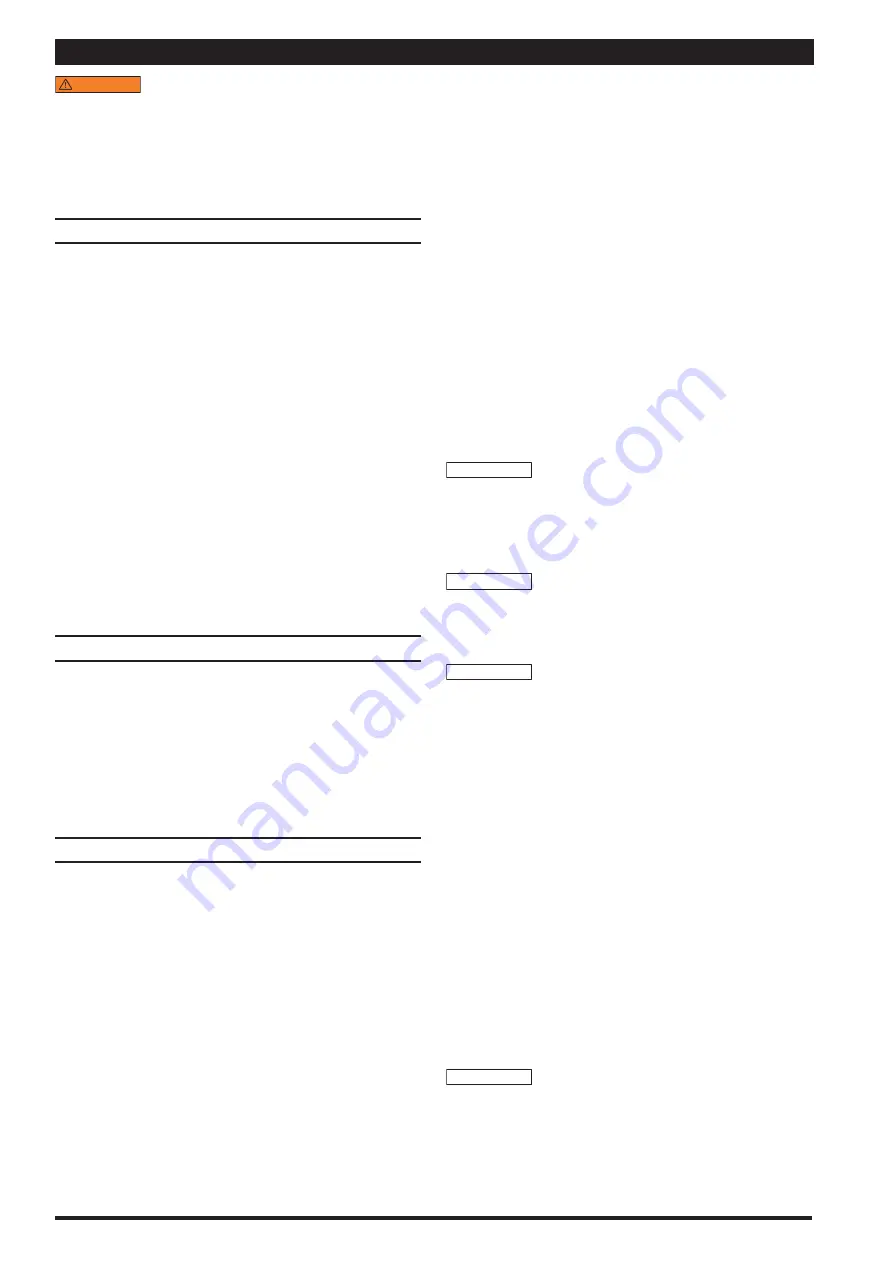
Page 6 of 8
S237-SA (en)
WARNING
Always wear eye protection while per-
forming maintenance on this pump. Always turn off
the air supply and disconnect the air supply hose
before installing, removing or adjusting any acces-
sory on this pump or before performing any main-
tenance on this pump.
LUBRICATION
Each time a S237-SA Sump Pump is disassembled for
maintenance and repair or replacement of parts, lu-
bricate the Pump as follows:
1. Remove the Oil Chamber Plug (8) and fill the oil
chamber in the Backhead (1) with Ingersoll-Rand
No. 50 Oil.
2. Before attaching the air hose, inject about 3 cc of
oil into the air inlet.
3. After each four hours of operation, unless an air
line lubricator is used, fill the oil chamber in the
Backhead with oil.
4. After each forty hours of operation, or as experi-
ence indicates, pump 10 or 15 strokes of Inger-
soll-Rand Water Pump Grease No. 80 into the
Grease Fitting (15) on the Motor Housing (14).
Use the No. P25-228 Grease Gun.
5. We recommend the use of Ingersoll-Rand No.
8LUB12 Lubricator located in the air supply line
as close to the Pump as practical. Keep the Lubri-
cator filled with Ingersoll-Rand No. 50 Oil.
AIR STRAINER
Periodically, clean the Air Strainer Screen (9) as fol-
lows:
1. Shut off the air supply to the Pump.
2. Unscrew the Air Strainer Plug (11).
3. If the Screen still appears clogged, unscrew the
Air Strainer Cap (10) and withdraw the Screen.
Clean the Screen in a suitable cleaning solution
in a well ventilated area.
DISASSEMBLY
General Instructions
1. Do not disassemble the Pump any further than
necessary to replace or repair damaged parts.
2. Whenever grasping a part in a vise, always use
leather-covered or copper-covered vise jaws to
protect the surface of the part and help prevent
distortion. This is particularly true of threaded
members and housings.
3. Do not remove any part which is a press fit in or
on a sub assembly unless the removal of that part
is necessary for repairs or replacement.
Disassemble a S237-SA Pump as follows:
1. If the Air Strainer Screen (9) is to be cleaned or
replaced, unscrew the Air Strainer Cap (10) and
withdraw the Screen.
2. Unscrew and remove the Backhead Cap Screws
(13). Lift off the Backhead.
3. If the oiler is to be disassembled, remove the Oil-
er Body Retainer (7) and withdraw the Oiler Body
Assembly (2) from the Backhead.
4. Unscrew the Impeller Cover Cap Screws (48) and
remove the Inlet (46) and Impeller Cover (45).
5. Sprag the Impeller (41) against rotation by insert-
ing a long screwdriver through one of the suction
ports and into the discharge port in the Housing
(14).
6. Unscrew the Impeller Retaining Screw (43) and
remove the Impeller.
7. While grasping the Controller (18) in one hand,
gently tap on the impeller end of the Rotor Shaft
(32) with a plastic hammer and withdraw the mo-
tor from the Housing.
8. The upper Rotor Shaft Bearing (33) and Bearing
Spacer (34) usually come out with the motor.
Slide them off the Rotor Shaft.
NOTICE
The Controller Retaining Nut (20) has a
right-hand thread.
9. Grasp the Rotor Shaft vertically in copper-cov-
ered vise jaws, and unscrew the Controller Re-
taining Nut.
NOTICE
The Controller Assembly has a left-
hand thread.
10. Using the No. 99V60-950 Controller Wrench, un-
screw the Controller Assembly.
NOTICE
Do not attempt to disassemble the
Controller. It is available only as a unit.
11. Lift off the Rear End Plate Gasket (22).
12. Set the Bearing Cage (21) on blocks on an arbor
press. Using a metal sleeve that contacts only the
outer race of the Rear Rotor Bearing (19), press
off the Bearing Cage.
13. If it is necessary to remove the Rear Rotor Bear-
ing, insert the Rear Rotor Bearing into the No.
99V60-A592 Bearing Clamp and tighten the nut
on the fixture. Insert the No. 99V60-951 Seal
Pressing Tool in the center.
14. Lift off the Rotor Bearing Seal (19) and Rear End
Plate (23).
15. Lift off the Cylinder (24).
16. Remove the Vanes (29).
17. Withdraw the Rotor (27) and lift out the Rotor Key (28).
18. Lift off the Front End Plate (30).
19. Remove the Motor Clamp Washers (31).
NOTICE
The Water Seal Cap Assembly (37) has
a left-hand thread. Do not remove the Water Seals
(38) from within the Water Seal Cap unless you
have two new Seals on hand for installation. The
Water Seals are always damaged during the remov-
al process. Always check the Water Seals for wear or
leakage.
MAINTENANCE SECTION