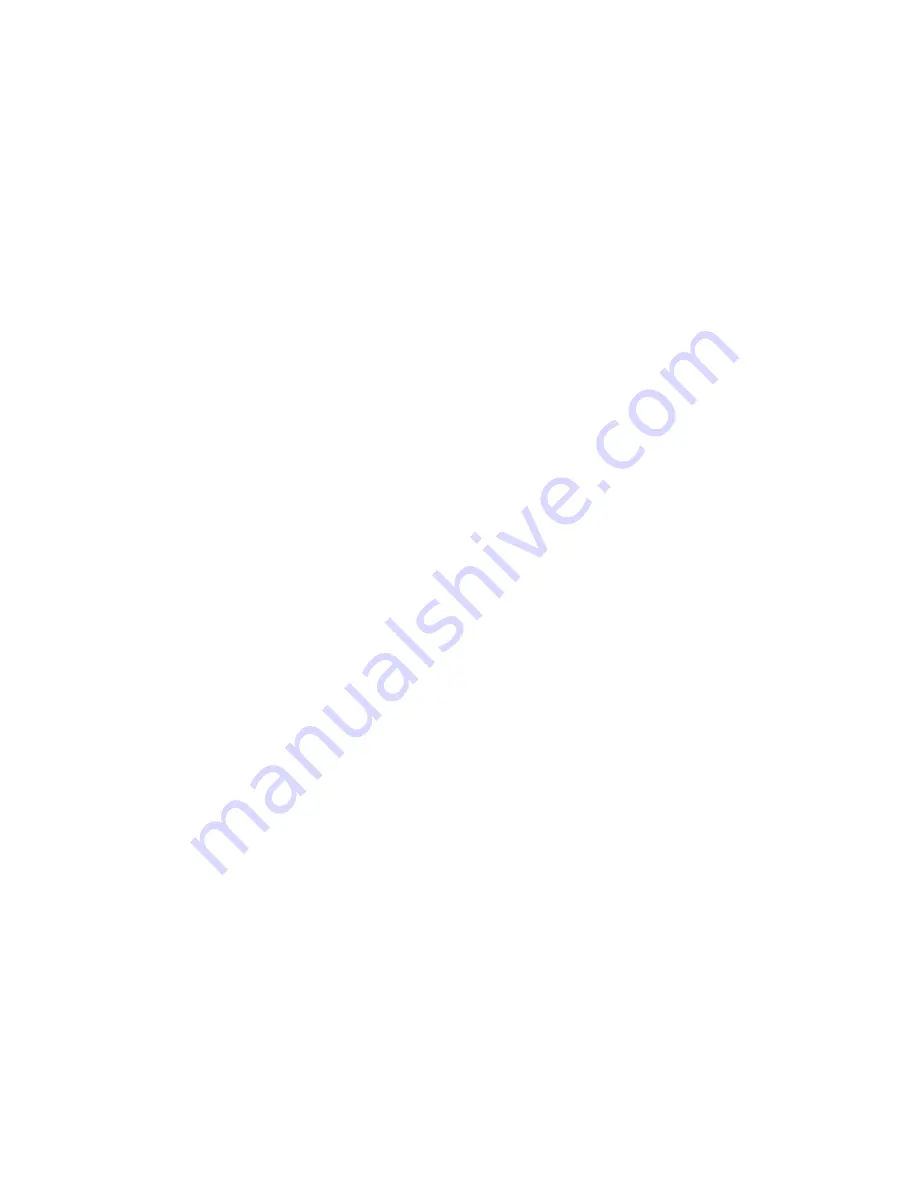
2
TABLE OF CONTENTS
0.0
SAFETY AND WARNINGS
0.1 safety instructions
0.2 safety precautions
0.3 decals
1.0
RECEIPT OF EQUIPMENT
1.1 inspection
1.2 unpacking and handling
1.3 tools
2.0
INSTALLATION
2.1 ventilation
2.2 foundation requirements
2.3 piping
2.4 electrical installation
2.5 outdoor sheltered
3.0
INTELLISYS
®
3.1 intellisys controls
3.2 display screen
3.3 current status
3.4 main menu
3.5 operator setpoints
3.6 options
3.7 sensor calibration
3.8 alarm history
3.9 warnings
3.10 alarms
4.0
SCHEDULED PREVENTATIVE MAINTENANCE
4.1 maintenance schedule
4.2 maintenance records
4.3 maintenance procedures
4.4 inlet air filter
4.5 coolant filter
4.6 coolant
4.7 separator tank scavenge screen/orifice
4.8 coolant separator element
4.9 cooler cores (cleaning)
4.10 motor lubrication
4.11 long term storage
4.12 coolant/lubricant changeout
4.13 intellisys removal
4.14 coolant hoses
4.15 fluid and vibration monitoring
4.16 coolant sampling procedure
5.0
SYSTEMS
5.1 general system information
5.2 air cooled compressors
5.3 coolant system
5.4 compressed air system
5.5 coolant/air separation system
5.6 electrical system
5.7 stepper motor inlet control
5.8 capacity control system
5.9 automatic start/stop control
5.10 remote start/sto
6.0
TROUBLESHOOTING
7.0
OPTIONS
7.1 power outage restart option
7.2 sequencer
7.3 low ambient
7.4 separator delta-p solenoid
7.5 separator delta-p sensor
7.6 high dust filter
7.7 lead/lag cycle length
7.8 schedule start/stop
7.9 remote load/unload
7.10 modbus
7.11 integral sequencing
8.0
REFERENCE DRAWINGS
8.1 electrical schematic, star delta
8.2 foundation plan, 125/150 HP, A/C - Single Stage
8.3 foundation plan, 200 HP, A/C - Single Stage
8.4 foundation plan, 125/150 HP, W/C - Single Stage
8.5 foundation plan, 200 HP, W/C - Single Stage
8.6 foundation plan, 125/150 HP, A/C - Two Stage
8.7 foundation plan, 200 HP, A/C - Two Stage
8.8 foundation plan, 125/150 HP, W/C - Two Stage
8.9 foundation plan, 200 HP, W/C - Two Stage
8.10 flow schematic, A/C - Single Stage
8.11 flow schematic, W/C-90°F (32°C) - Single Stage
8.12 flow schematic, W/C-115°F (46°C) - Single Stage
8.13 flow schematic, A/C - Two Stage
8.14 flow schematic, W/C-90°F (32°C) - Two Stage
8.15 flow schematic, W/C-115°F (46°C) - Two Stage
8.16 typical system flow diagrams
9.0
WATER QUALITY RECOMMENDATIONS
10.0
MAINTENANCE RECORD
Weight ..............................See foundation plan, Section 8.0
Cooling Air Flow .............See foundation plan, Section 8.0
Ambient Temperature Limits ..........................35°F to 115°F
...........................................................................(
(2°C to 46°C)
Coolant.............................Factory Filled SSR Ultra Coolant
Coolant Change ............................8000 hours or two years
............................................................
whichever comes first
Coolant Capacity
125/200 HP (90-160 KW) -
Single Stage ...................................23.0 gallons (87.4 liters)
100 HP (75 KW) -
Two Stage .......................................22.0 gallons (83.3 liters)
125-200 HP (90-160 KW) -
Two Stage .....................................30.0 gallons (113.6 liters)
Discharge Temperature Limit .........................228°F (109°C)
Power Inlet Wiring .........................Recommended conduit:
............................
metallic flexible Greenfield, or equivalent
Tools ..............................................U.S. standard and metric
...................................
are required to perform maintenance
Содержание 100-200
Страница 17: ...FIGURE 2 5 1 TYPICAL OUTDOOR SHELTERED INSTALLATION 15...
Страница 18: ...16 3 0 INTELLISYS INTELLISYS CONTROLLER INGERSOLLrAND INTELLISYS...
Страница 52: ...50 54418074 REV B 8 0 REFERENCE DRAWINGS 8 1 ELECTRICAL SCHEMATIC STAR DELTA...
Страница 53: ...51...
Страница 54: ...52 54622865 REV B 8 2 FOUNDATION PLAN 125 150 HP 90 110KW AIRCOOLED SINGLE STAGE CONTINUED...
Страница 55: ...53 54622865 REV B 8 2 FOUNDATION PLAN 125 150 HP 90 110 KW AIRCOOLED SINGLE STAGE...
Страница 56: ...8 3 FOUNDATION PLAN 200 HP 132 160 KW AIRCOOLED SINGLE STAGE CONTINUED 54622931 REV B 54...
Страница 57: ...8 3 FOUNDATION PLAN 200 HP 132 160 KW AIRCOOLED SINGLE STAGE 54622931 REV B 55...
Страница 58: ...56 8 4 FOUNDATION PLAN 125 150 HP 90 110 KW WATERCOOLED SINGLE STAGE CONTINUED 39925300 REV C...
Страница 59: ...57 8 4 FOUNDATION PLAN 125 150 HP 90 110 KW WATERCOOLED SINGLE STAGE 39925300 REV C...
Страница 60: ...58 8 5 FOUNDATION PLAN 200 HP 132 160 KW WATERCOOLED SINGLE STAGE CONTINUED 39926191 REV C...
Страница 61: ...59 8 5 FOUNDATION PLAN 200 HP 132 160 KW WATERCOOLED SINGLE STAGE 39926191 REV C...
Страница 62: ...60 8 6 FOUNDATION PLAN AIRCOOLED CONTINUED 100 150 HP 75 110 KW TWO STAGE 54622980 REV B...
Страница 63: ...61 54622980 REV B 8 6 FOUNDATION PLAN AIRCOOLED 100 150 HP 75 110 KW TWO STAGE...
Страница 64: ...62 8 7 FOUNDATION PLAN AIRCOOLED CONTINUED 200 HP 132 160 KW TWO STAGE 54623053 REV B...
Страница 65: ...63 54623053 REV B 8 7 FOUNDATION PLAN AIRCOOLED 200 HP 132 160 KW TWO STAGE...
Страница 66: ...64 8 8 FOUNDATION PLAN WATERCOOLED CONTINUED 100 150 HP 75 110 KW TWO STAGE 39925326 REV C...
Страница 67: ...65 8 8 FOUNDATION PLAN WATERCOOLED 100 150 HP 75 110 KW TWO STAGE 39925326 REV C...
Страница 68: ...66 8 9 FOUNDATION PLAN WATERCOOLED CONTINUED 200 HP 132 160 KW TWO STAGE 39926340 REV C...
Страница 69: ...67 8 9 FOUNDATION PLAN WATERCOOLED 200 HP 132 160 KW TWO STAGE 39926340 REV C...
Страница 70: ...68 8 10 FLOW SCHEMATIC AIRCOOLED SINGLE STAGE 54579081 REV A...
Страница 71: ...69...
Страница 72: ...70 8 11 FLOW SCHEMATIC WATERCOOLED 90 F 32 C SINGLE STAGE 54579503 REV A...
Страница 73: ...71...
Страница 74: ...72 8 12 FLOW SCHEMATIC WATERCOOLED 115 F 46 SINGLE STAGE 54579511 REV A...
Страница 75: ...73...
Страница 76: ...74 8 13 FLOW SCHEMATIC AIR COOLED TWO STAGE 54579644 REV A...
Страница 77: ...75...
Страница 78: ...76 8 14 FLOW SCHEMATIC WATERCOOLED 90 F 32 C TWO STAGE 54579693 REV A...
Страница 79: ...77...
Страница 80: ...78 8 15 FLOW SCHEMATIC WATERCOOLED 115 F 46 C TWO STAGE 54579727 REV A...
Страница 81: ...79...
Страница 82: ...80 8 16 TYPICAL SYSTEM FLOW DIAGRAMS TYPICAL SYSTEM FLOW DIAGRAM...
Страница 83: ...81 8 16 TYPICAL SYSTEM FLOW DIAGRAMS...
Страница 84: ...82 8 16 TYPICAL SYSTEM FLOW DIAGRAMS...
Страница 85: ...83 8 16 TYPICAL SYSTEM FLOW DIAGRAMS...
Страница 86: ...84 8 16 TYPICAL SYSTEM FLOW DIAGRAMS...
Страница 90: ...88 DATE RUN TIME WORK DONE QTY UNIT WORK HOURS MEASURE BY 10 0 MAINTENANCE RECORD...
Страница 91: ...89 DATE RUN TIME WORK DONE QTY UNIT WORK HOURS MEASURE BY MAINTENANCE RECORD...
Страница 92: ...90 DATE RUN TIME WORK DONE QTY UNIT WORK HOURS MEASURE BY MAINTENANCE RECORD...
Страница 93: ...91 DATE RUN TIME WORK DONE QTY UNIT WORK HOURS MEASURE BY MAINTENANCE RECORD...