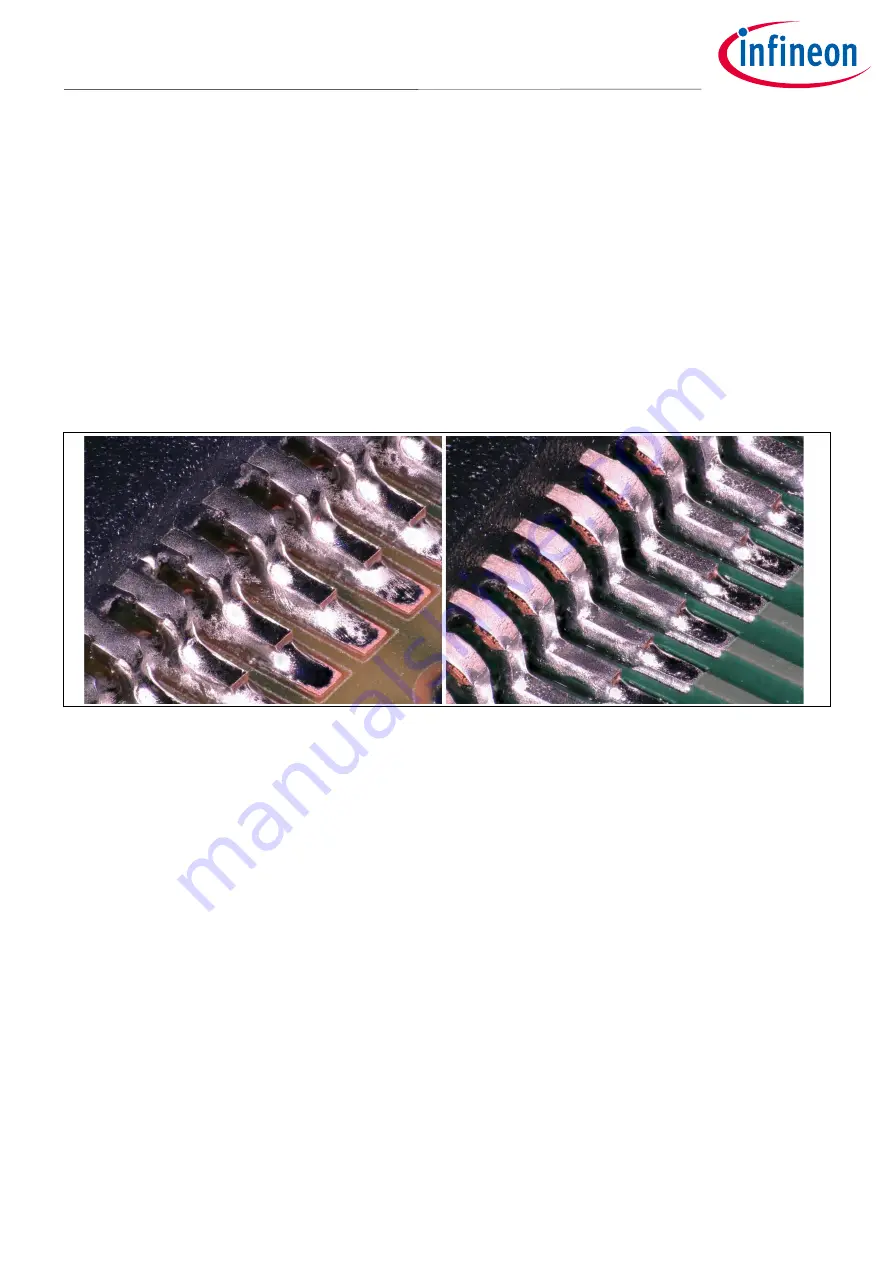
Additional Information
15 of 20
Revision 6.0
2020-11-12
Recommendations for Board Assembly of Infineon Quad Flat
Packages
Inspection
5
Inspection
5.1
Optical Solder Joint Inspection
The visual inspection of the solder joints at the gullwing-shaped QFP leads with conventional Automated
Optical Inspection (AOI) systems is a standard procedure.
shows optical images of two properly
soldered QFP with either having Sn plating or a PPF. As can be seen, the gullwing leads with PPF surface can
appear different on their top side from those with Sn plating because the Ni/Au surface does not melt together
with the solder during reflow. According to IPC-A-610 the top side of a gullwing lead is not taking part in the
solder joint formation [6]. Irrespective of the specific geometry of a gullwing lead the solder joint is generally
considered to be of good quality when the heel region is wetted up to a certain height and the sidewall is
sufficiently covered. The tips of the leads have bare copper (e.g. cut edges) that is not intended to wet by design
according to the IPC-A-610 [6].
Figure 8
Optical images of QFP with Sn plated gullwing leads (left) and with PPF surface (right). In
the latter example, the top side of the leads does appear different because the plating
does not melt together with the solder during reflow.
For engineering tasks, cross-sectioning can offer detailed information about the solder joint quality. Due to its
destructive character, cross-sectioning during monitoring is naturally not practical.
For further information about the acceptability of electronic assemblies inspected optically, please also refer to
the IPC-A-610 standard [6].
5.2
X-Ray Solder Joint Inspection
Automated X-ray Inspection (AXI) systems are appropriate for efficient inline control of component parts that
cannot be inspected properly by optical systems (such as exposed pads). AXI systems are available as 2D and
3D solutions. They usually consist of an X-ray camera and the hardware and software needed for inspection,
controlling, analyzing, and data transferring routines. These reliable systems enable the user to detect
soldering defects such as poor soldering, bridging, voiding, and missing parts. However, other defects such as
broken solder joints are not easily detectable by X-ray.
shows a typical X-ray photograph of a QFP component. The internal lead frame, as well as the wire
bonds, and the solder joints that connect the package to the PCB are visible. Large exposed pads may tend to
increase voiding because they do not provide a sufficient ratio between volume and surface necessary for
proper outgassing of the organic compounds during reflow. Generally, the extent of voiding depends on the