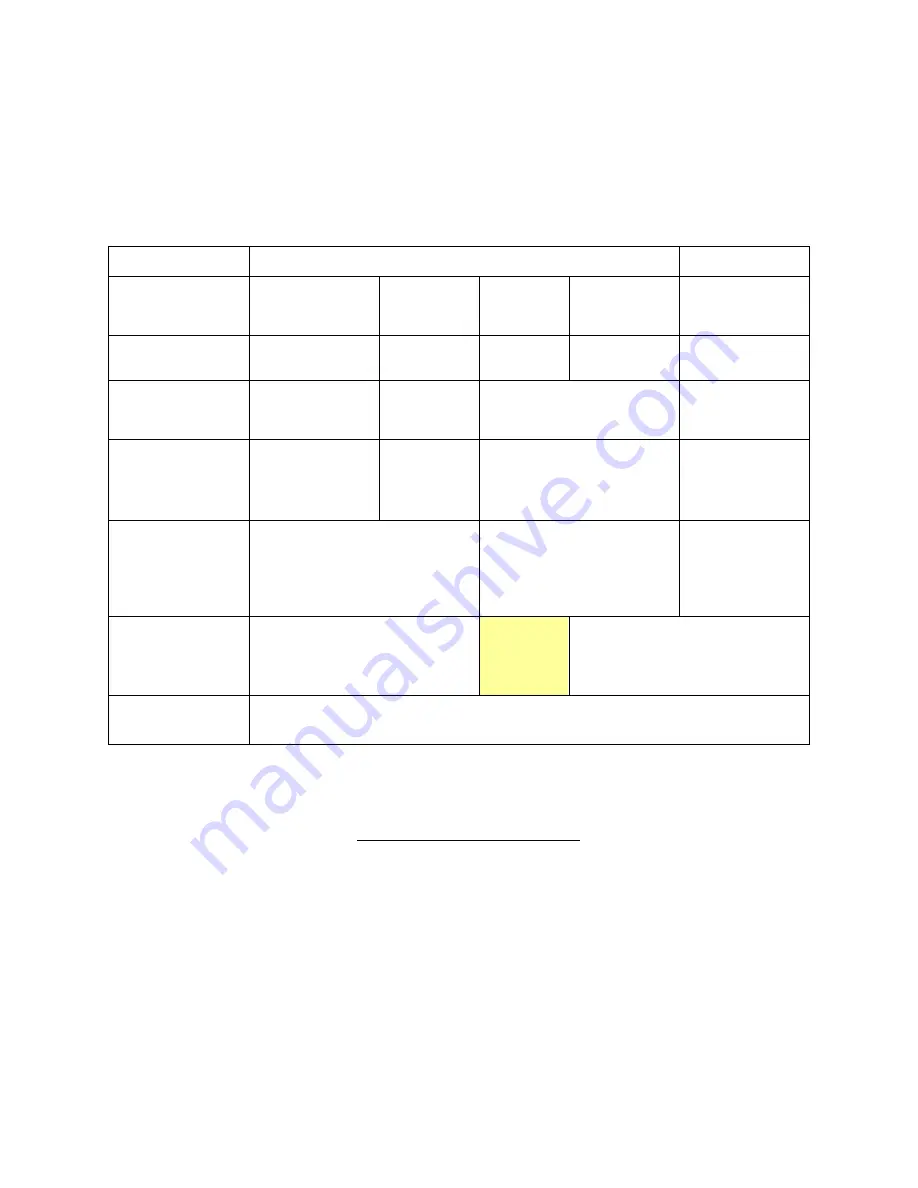
Chapter 3 Environment description and installation
3-9
3.3.2 MC, MCCB, Fuse and cable specifications.
MCCB/ MC/ Fuse
z
IMO warranty will not apply under the following condition.
(1) MCCB or fuse is not installed or incorrectly installed or installed with over
capacity, which has resulted in
iDrive
failure.
(2) MC or capacitor or surge absorber is connected in series between inverter
and motor.
iDrive
EDX model
###
-11/21/43
###
-43(-E)
020-11/040-11
040-11
040-21-E
075-21-E
075-23
150-21-E
220-21-E
150-23
220-23
075/150/220
Fuse
10A
300Vac
16A
300Vac
20A
300Vac
16A/600Vac
MCCB
10A
20A
32A
16A
MC
(from IMO)
MC14-S MC18-S
MC32-S
MC18-S
Power
Input/Output
cables (c.s.a.)
2.5mm
2
/ (13 AWG)
Terminal screw M4
4 mm
2
/ (11AWG)
Terminal screw M4
2.5mm
2
/ (13
AWG)
Terminal screw
M4
Earth/ground
cables PE
terminal (c.s.a.)
4 mm
2
/ (11AWG)
Terminal screw M4
See Note
1
Below
4 mm
2
(14AWG)
Terminal screw M4
Control
terminals (TM2)
Cable dimension 0.75mm
2
(18AWG) Terminal screw M3
Notes
1. To comply with BS7671 requirements the
iDrive
must be earthed by a conductor(s) of
minimum 4 mm
2
c.s.a. with additional mechanical protection. Therefore the
iDrive
must be
installed in a steel enclosure and wired according to the diagram on page 3-11.
2. Use a single fuse in the live line for 1-phase input
iDrive
models where supply is L+N.
Where L+L supply is to be used, each line must be fused.
For 3-phase input models, each L1(L)/L2/L3(N) phase must be fused or protected by MCCB.
3. A suitable three-phase ‘squirrel cage’ induction motor must be used with
iDrive
.
4. If an
iDrive
is to operate more than one motor in parallel, the total operating current should
be less than or equal to the
iDrive’s
rated output current.
A suitable thermistor should be installed in each motor to protect from winding over-heat.
5. Do not install a capacitor, LC, or RC network between the
iDrive
and the motor.