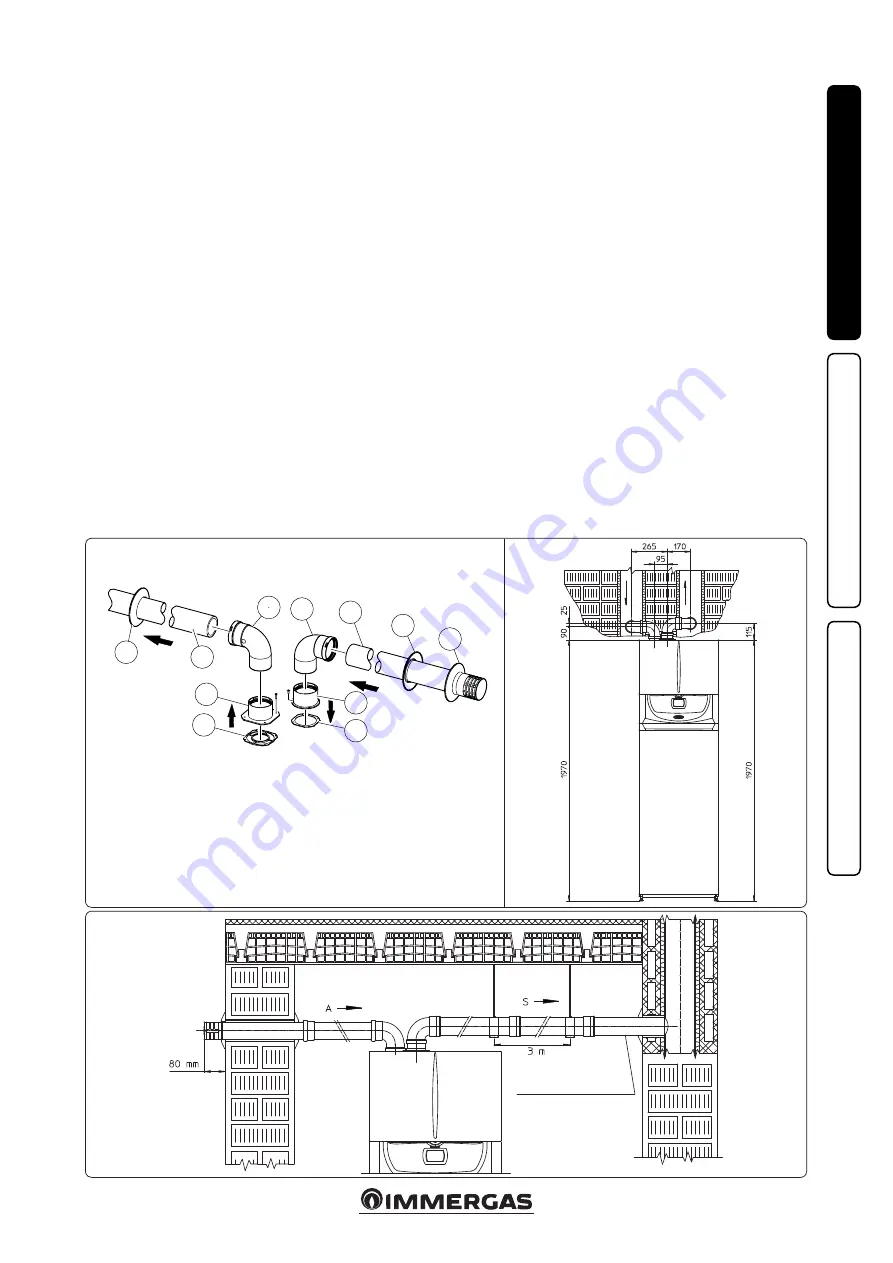
15
C
83
1-20
C
43
1-19
1-18
1
4
7
9
5
5
6
7
8
3
2
S
A
C
53
* - C
83
INS
TALLER
US
ER
MAINTEN
AN
CE TECHNI
CI
AN
1.14 SEPARATOR KIT INSTALLATION.
Type C configuration, sealed chamber and
fan assisted.
Separator kit Ø 80/80.
This kit allows air to come
in from outside the building and the fumes to exit
from the chimney or flue through divided flue
exhaust and air intake pipes. Combustion prod-
ucts are expelled from pipe (S) (in plastic, so as
to resist acid condensate). Air is taken in through
duct (A) for combustion (this is also in plastic).
The intake pipe (A) can be installed either on the
right or left hand side of the central exhaust pipe
(S). Both ducts can be routed in any direction.
• Kit assembly (Fig. 1-18): install flange (4) on
the central hole of the boiler, positioning gasket
(1) with the circular projections downwards in
contact with the boiler flange, and tighten using
the hex screws with flat tip supplied with the
kit. Remove the flat flange present in the most
external hole and replace it with the flange (3),
positioning the gasket (2) already present in
the boiler and tighten using the supplied self-
threading screws. Fit the male side (smooth) to
the bends (5) in the female side of the flanges
(3 and 4). Fit the intake terminal (6) with the
male side (smooth) in the female side of the
bend (5) up to the end stop, ensuring that the
internal and external wall sealing plates are
fitted. Fit the exhaust pipe (9) with the male
side (smooth) to the female side of the bend
(5) up to the end stop; making sure that the
internal wall sealing plate has been fitted, this
will ensure sealing and joining of the elements
making up the kit.
• Installation clearances (Fig. 1-19). The mini-
mum installation clearance measurements of
the Ø 80/80 separator terminal kit have been
stated in some limit conditions.
• Extensions for separator kit Ø 80/80. The
maximum vertical straight length (without
bends) that can be used for Ø 80 intake and
exhaust pipes is 41 metres, regardless from
whether they are used for intake or exhaust.
The maximum horizontal straight length (with
bend in suction and in exhaust) that can be
used for Ø 80 intake and exhaust pipes is 36
metres, regardless from whether they are used
for intake or exhaust.
N.B.:
to favour the removal of possible conden-
sate forming in the exhaust pipe, tilt the pipes
towards the boiler with a minimum slope of
1.5% (Fig. 1-20).
The kit includes:
N° 1 - Exhaust gasket (1)
N° 1 - Flange seal gasket (2)
N° 1 - Female intake flange (3)
N° 1 - Female drain flange (4)
N° 2 - Bend 90° Ø 80 (5)
N° 1 - Intake terminal Ø 80 (6)
N° 2 - Internal wall sealing plates (7)
N° 1 - External wall sealing plate (8)
N° 1 - Drain pipe Ø 80 (9)
* to er complete C
53
configuration also provide for a roof discharge termi-
nal.
Minimum slope 1.5 %
Содержание HERCULES SOLAR 26 2 ErP
Страница 1: ...HERCULES SOLAR 26 2 ErP Instruction and recommendation booklet IE 1 037974ENG ...
Страница 2: ......
Страница 40: ...40 3 7 7 8 9 INSTALLER USER MAINTENANCE TECHNICIAN ...
Страница 42: ...42 3 9 Part E 17 19 18 18 18 18 INSTALLER USER MAINTENANCE TECHNICIAN Part E ...
Страница 51: ......