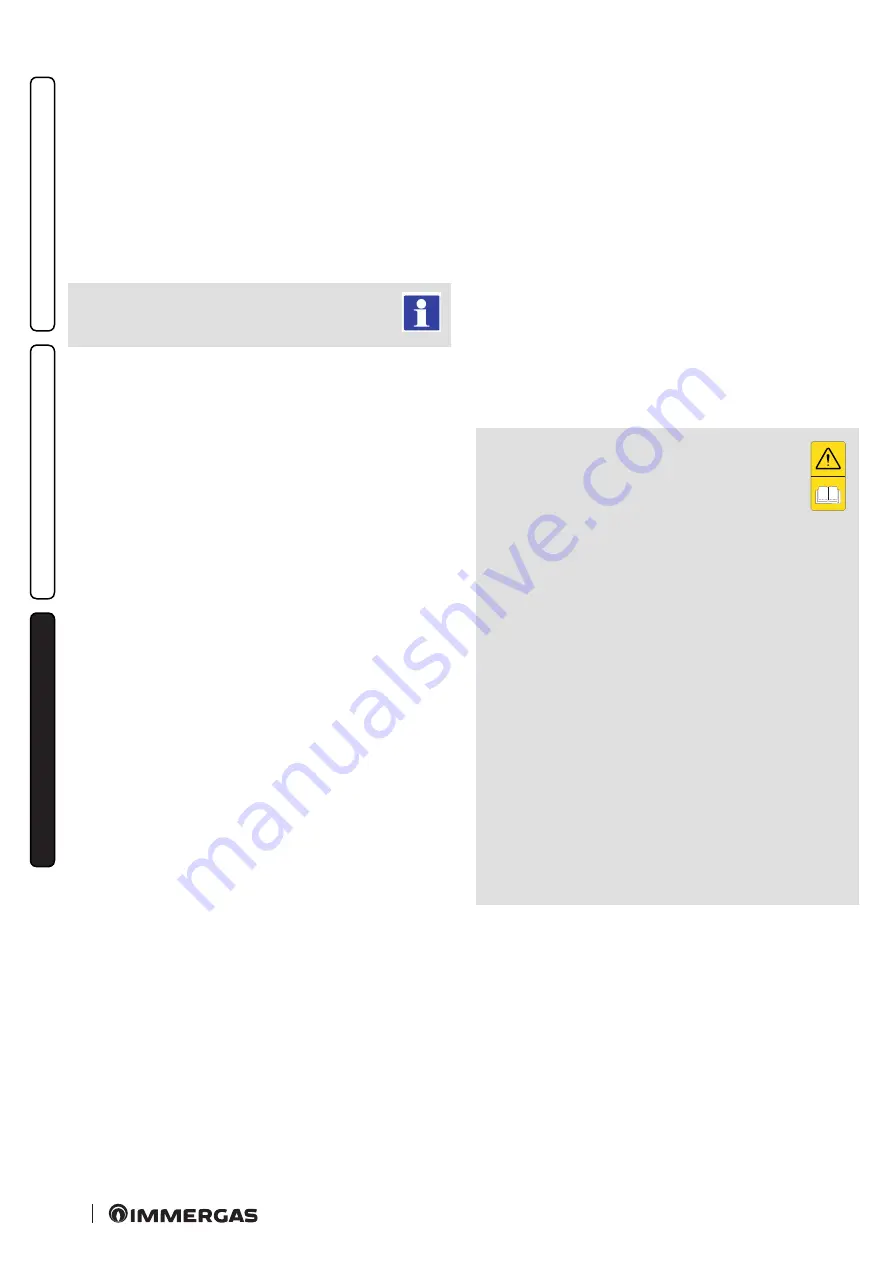
48
INS
TALLER
US
ER
MAINTEN
AN
CE TECHNI
CI
AN
Comando Amico Remoto
V2
: the boiler is prepared for the applica-
tion of the Comando Amico Remoto remote control
V2
(CAR
V2
),
which must be connected to clamps 44/40 and 41 of the terminal
board (located in the boiler control panel) respecting the polarity
and eliminating jumper X40.
Room thermostat: the boiler is prepared for the application of
the room thermostat (S20), which must be connected to clamps
44/40 - 41 of the terminal board (located in the boiler control
panel) eliminating jumper X40.
3.6 POSSIBLE PROBLEMS AND THEIR CAUSES.
Maintenance interventions must be carried out by
an authorised company (e.g. Immergas After-Sales
Technical Assistance Service).
- Smell of gas.
Caused by leakage from gas circuit pipelines. Check
tightness of gas intake circuit.
- Repeated ignition blocks.
It can be caused by no gas, check the
presence of pressure in the network and that the gas adduction
cock is open. Incorrect adjustment of the gas valve, check the
correct calibration of the gas valve.
- Irregular combustion or noisiness.
It may be caused by: a
dirty burner, incorrect combustion parameters, intake-exhaust
terminal not correctly installed. Clean the above components
and ensure correct installation of the terminal, check correct
setting of the gas valve (Off-Set setting) and correct percentage
of CO
2
in flue gas.
- Frequent interventions of the safety thermostat function (del-
egated to flow probe and system return probe).
It can depend
on the lack of water in the boiler, little water circulation in the
system (or blocked pump, see Par. 1.28). Check on the pressure
gauge that the system pressure is within established limits. Check
that the radiator valves are not closed and also the functionality
of the pump.
- Drain trap clogged.
This may be caused by dirt or combustion
products deposited inside. Check that there are no residues of
material blocking the flow of condensate.
- Heat exchanger blocked.
This may be caused by the drain trap
being blocked. Check that there are no residues of material
blocking the flow of condensate.
- Noise due to air in the system.
Check opening of the special air
vent valve cap (Part. 22 Fig. 33). Make sure the system pressure
and expansion tank factory-set pressure values are within the
set limits. The factory-set pressure values of the expansion vessel
must be 1.0 bar, the value of system pressure must be between
1 and 1.2 bar.
Red pump LED.
There can be three possible causes for this anomaly:
- Low power supply voltage.
When the minimum voltage is
reached after about 2 seconds, the LED switches from green
to red and the pump stops. Wait for the power supply voltage
to rise; when the pump restarts, the LED will turn green again
with a delay of about one second.
Note: obviously the flow rate decreases as the supply voltage
decreases.
- Rotor seized.
Powering the pump with the rotor seized, after
about 4 seconds the LED switches from green to red. Carefully
act on the screw in the middle of the head to manually release
the crankshaft; circulation starts up immediately after the rotor
is released and the LED switches from red to green after about
10 seconds.
- Electrical error.
Pump, wiring or P.C.B. fault. Check the indi-
cated components.
3.7 CONVERTING THE BOILER TO OTHER
TYPES OF GAS.
If the appliance needs to be converted to a different
gas type to that specified on the data plate, request the
relative conversion kit for quick and easy conversion.
The gas conversion operation must be carried out by
an authorised company (e.g. Immergas After-Sales Technical
Assistance Service).
To convert to another type of gas the following operations are
required:
- disconnect power to the appliance;
- replace the nozzle located on the gas valve (Part. 10 Fig. 33),
taking care to disconnect the appliance during this operation;
- re-power the appliance;
- calibrate fan speed (Par. 3.8):
- adjust the CO
2
(Par. 3.9);
- seal the gas flow rate regulation devices (if settings are mod-
ified);
- after completing the conversion, apply the sticker, contained
in the conversion kit, on the data plate in the area relating to
the type of gas.
These adjustments must be made with reference to the type of
gas used, following that given in the table (Par. 4.2).