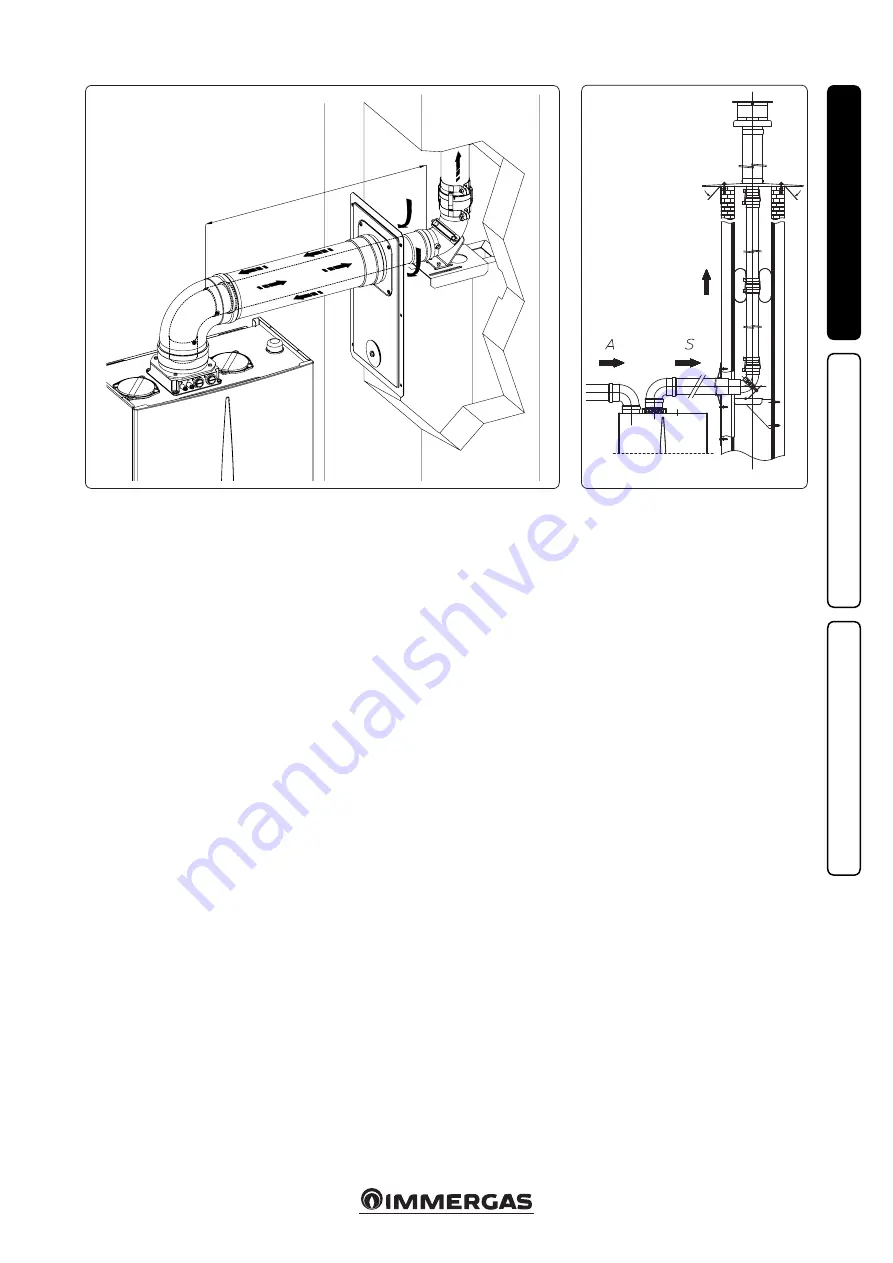
17
1-24
C
53
X
1-23
C
93
INS
TALLER
US
ER
MAINTEN
AN
CE TECHNI
CI
AN
1.15 DUCTING OF FLUES OR
TECHNICAL SLOTS.
Ducting is an operation through which, via
the introduction of one or more relevant pipes,
one achieves a system for the evacuation of the
combustion products of a gas appliance, made up
from the coupling of an existing or new ducting
pipe with a chimney, flue or technical slot (also
in new buildings) (Fig. 1-24). Ducting requires
ducts declared to be suitable for the purpose by
the manufacturer, following the installation and
user instructions, provided by the manufacturer
and the requirements of the standards in force.
Immergas ducting system.
The Ø 60 rigid and
Ø 80 flexible “Green Range” ducting systems must
only be used for domestic use and with Immergas
condensing boilers.
In any case, ducting operations must respect
the provisions contained in the standard and in
current technical regulations. The instructions in
the project or technical report must likewise be
followed, in cases provided for by the standard
and current technical regulations. The system or
components of the system have a technical life
complying with current standards, provided that:
- it is used in average atmospheric and environ-
mental conditions, according to current regula-
tions (absence of fumes, dusts or gases that can
alter the normal thermophysical or chemical
conditions; existence of temperatures coming
within the standard range of daily variation,
etc.).
- Installation and maintenance must be per-
formed according to the indications supplied
by the manufacturer and in compliance with
the provisions in force.
- The max. possible length of the Ø 60 flexible
ducting vertical section is equal to 22 m. This
length is obtained considering the complete
Ø 80 exhaust terminal, 1m of Ø 80 pipe in
exhaust, two 90° Ø 80 bends at boiler outlet.
- The max. possible length of the Ø 80 flexible
ducting vertical section is equal to 30 m. This
length is obtained considering the complete
exhaust terminal, 1m of Ø 80 pipe in exhaust,
two 90° Ø 80 bends at boiler outlet for connect-
ing to the ducting system and two direction
changes of the flexible hose inside the chimney/
technical slot.
- The maximum possible length of the Ø 80 rigid
ducting vertical section is equal to 30 m. This
length is obtained considering the complete
Ø 80 exhaust terminal, 1m of Ø 80 pipe in ex-
haust, two 90° Ø 80 bends on the boiler outlet.
1.16 CONFIGURATION TYPE B, OPEN
CHAMBER AND FAN ASSISTED FOR
INDOORS.
The appliance can be installed inside buildings
in
23
or B
53
mode; in this case, all technical rules
and national and local regulations in force, must
be complied with.
- type B open chamber boilers must not be
installed in places where commercial, artisan
or industrial activities take place, which use
products that may develop volatile vapours
or substances (e.g. acid vapours, glues, paints,
solvents, combustibles, etc.), as well as dusts
(e.g. dust deriving from the working of wood,
coal fines, cement, etc.), which may be harm-
ful for the components of the appliance and
jeopardise operation.
- in B
23
and B
53
configuration, the boilers must
not be installed in bedrooms, bathrooms or in
studio flats unless otherwise provided by local
regulations.
- The installation of appliances in B
23
and B
53
con-
figurations are only recommended outdoors (in
a partially-protected place) or in places that
are not lived in and which are permanently
ventilated.
The suitable kit referred to in paragraph 1.10
must be used for installation.
1.17 FLUE EXHAUST TO FLUE/CHIMNEY.
Flue exhaust does not necessarily have to be
connected to a branched type traditional flue.
The flue exhaust, for boiler clots installed in C
configuration, can be connected to a special
LAS type multiple flue. For B configurations,
exhaust is only allowed into individual chimney
or directly into the external atmosphere via a
relevant terminal, unless otherwise provided by
local regulations. The multiple flues and the com-
bined flues must also only be connected to type C
appliances of the same type (condensing), having
nominal heat inputs that do not differ by more
than 30% less with respect to the maximum that
can be attached and powered by the same fuel.
The thermo-fluid dynamic features (flue flow
rate, % of carbon dioxide, % humidity etc....) of
the appliances attached to the same multiple flues
or combined flues, must not differ by more than
10% with respect to the average boiler attached.
Multiple and combined flues must be specially
designed according to the calculation method
and requirements of the technical standards in
force, by a professionally qualified company (e.g.
EN 13384).
Chimney or flue sections for connec-
tion of the flue exhaust pipe must comply with
requisites of technical standards in force.
Содержание 3.025615
Страница 1: ...MAGIS VICTRIX ERP IE Instruction and recommendation booklet 1 038946ENG...
Страница 2: ......