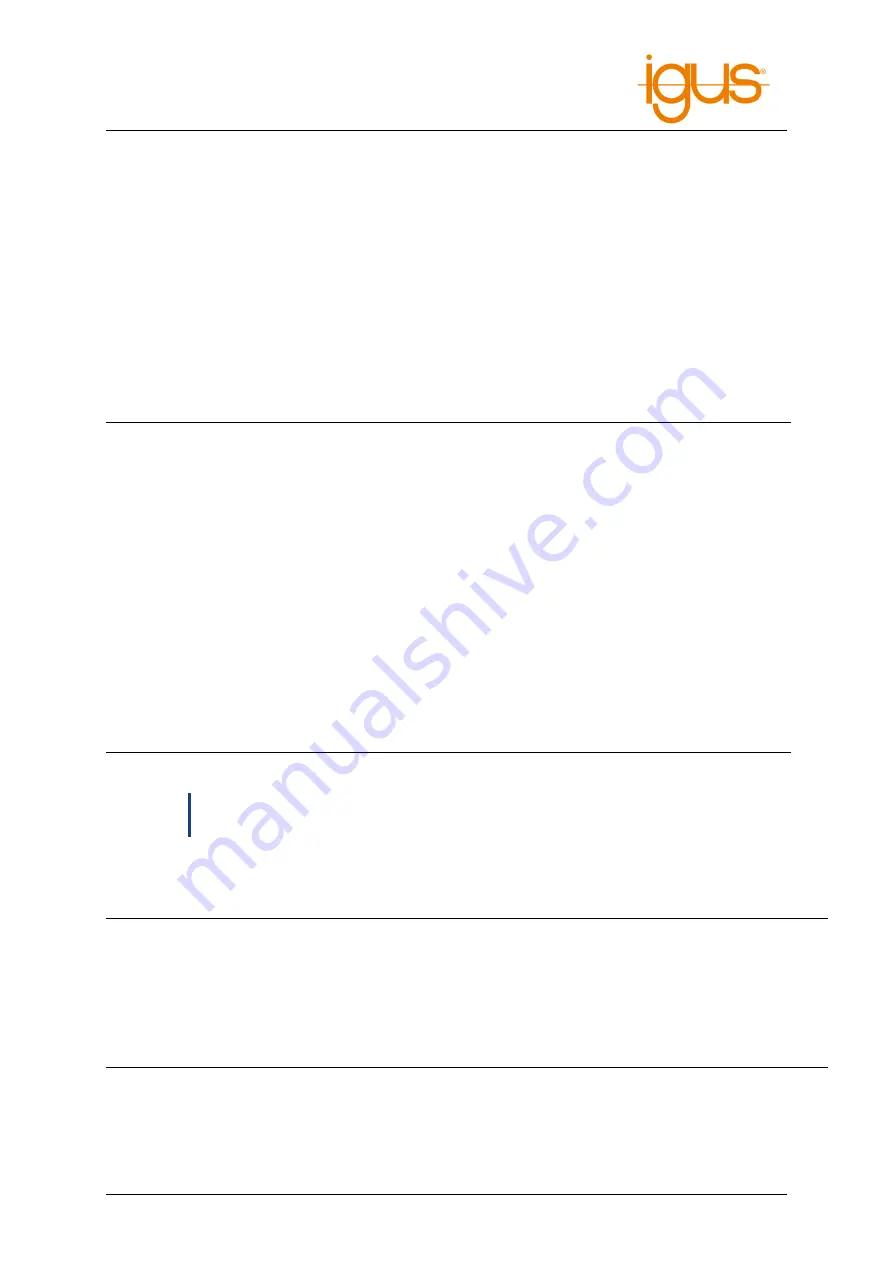
9 SOFTWARE CONFIGURATION
9.2 Interfaces
For communication with and control by other software and devices iRC offers a PLC interface, the
CRI Ethernet interface and an interface for connecting ifm O2D cameras.
9.2.1 PLC Interface
The PLC interface enables the execution of basic functions and the signaling of states by means of
digital inputs and outputs. In addition to control by a PLC, this interface also enables operation by
hardware pushbuttons.
The PLC interface requires unused digital inputs and outputs. It reacts to rising edges at inputs.
The following input functions are supported:
Parameter
Meaning
Enable
Executes Reset and Enable
Request reference
Starts the referencing of all axes
Play
Starts the execution of the loaded program if no program is running, con-
tinues a paused program or stops the execution of a running program
Pause
Pauses a running program or continues a paused program
Alt Start
One-button control: Executes the following functions in succession when
the button is pressed several times: Reset, Activate, Reference (if not yet
done), Start program
Alt Stop
One-button control: Executes the following functions in succession when
the button is pressed several times: Pause, Stop, Reset
Shutdown
Shuts down the control computer
Start Platform Mission
Starts the mission of the mobile platform
Add joint command
Add-Axis statement to the current position in the program editor
Add linear command
Add-Linear statement to the current position in the program editor
ð
Add-Joint and Add-Linear can only be used if iRC is connected to the robot.
The following output functions are supported:
Parameter
Meaning
No fault
Output is active when the robot is in fault-free state
Fault
Output is active when the robot is in fault state
Robot is referenced
Output is active when all axes are referenced
Program running
Output is active when a program is running
No program running
Output is active when no program is running
Platform mission running
The mobile platform is executing a mission
The configuration of the PLC interface is done via the configuration area in iRC (File
→
Configure
Interfaces
→
PLC interface). To configure a robot with integrated control it must be connected. The
field "Active" activates the interface, "Automatically connect" causes iRC to try to connect to the robot
automatically. The number fields to the inputs and outputs correspond to the numbers of the digital
©2022 igus® GmbH
42
Содержание ReBeL
Страница 1: ......
Страница 2: ...Version 13 4 PRERELEASE July 13 2022 Commonplace Robotics GmbH...
Страница 14: ...5 QUICK START GUIDE Figure 1 Choosing a project Figure 2 Jog Commands 2022 igus GmbH 12...
Страница 63: ...10 MODBUS Value Meaning Table 34 Reason for last stop pause of program 2022 igus GmbH 61...