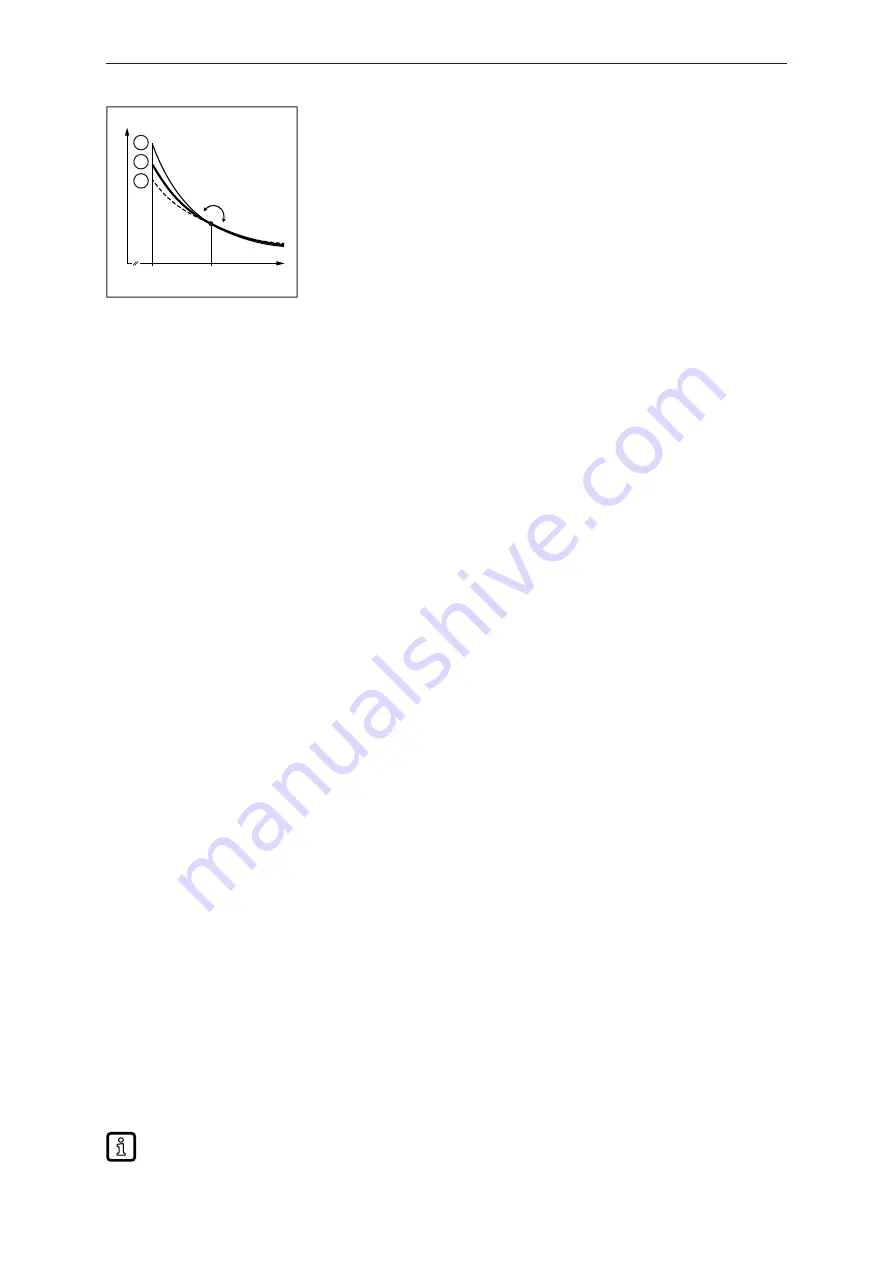
Mechatronic flow sensor
SB1xxx SB2xxx SB3xxx SB4xxx SB5xxx SB6xxx SB7xxx SB8xxx SB9xxx
SB03xx
23
40 °C
20°C
+ CGA
-
1
2
R
ʋ
T
Fig. 19: Measured value
characteristic for 3 oils
ν:
Viscosity of the oil
T:
Temperature of the oil
R:
Reference oil
1:
Oil 1
2:
Oil 2
10.4.3.1 Parameter setting via unit keys: Calibration
u
Call up the menu [EF] > [CFG].
u
Select [CGA] and set the slope of the measuring characteristic in per cent.
10.4.3.2 Parameter setting via IO-Link: Calibration
u
Select [Parameter] > [Calibration].
u
Select [CGA] and set the slope of the measuring characteristic in per cent.
10.4.4 Output polarity of the switching outputs
The parameter [P-n] can be used to select whether the outputs are plus-switching or negative-
switching.
10.4.4.1 Parameter setting via unit keys: Output polarity
u
Call up the menu [EF] > [CFG].
u
Select [P-n] and set PnP or nPn.
10.4.4.2 Parameter setting via IO-Link: Output polarity
u
Call up [Parameters] > [Output Configuration].
u
Select [P-n] and set PnP or nPn.
10.4.5 Damping
Damping can be used to set a delay time during which the unit does not output erratically occurring
measured value changes.
The set delay time stabilises the output signals.
This concerns the outputs, the display and the process value transmission via the IO-Link interface.
Selectable values:
•
[dAP] = damping time for switching signal, display and IO-Link signal (63% rise time)
•
[dAA] = damping time for analogue signal (10...90% rise time)
The damping time is added to the response time of the sensor (
Ò
Technical data).
The signals UL and OL are defined under consideration of the damping time.
Measured value damping only has an effect on the measured variable flow.