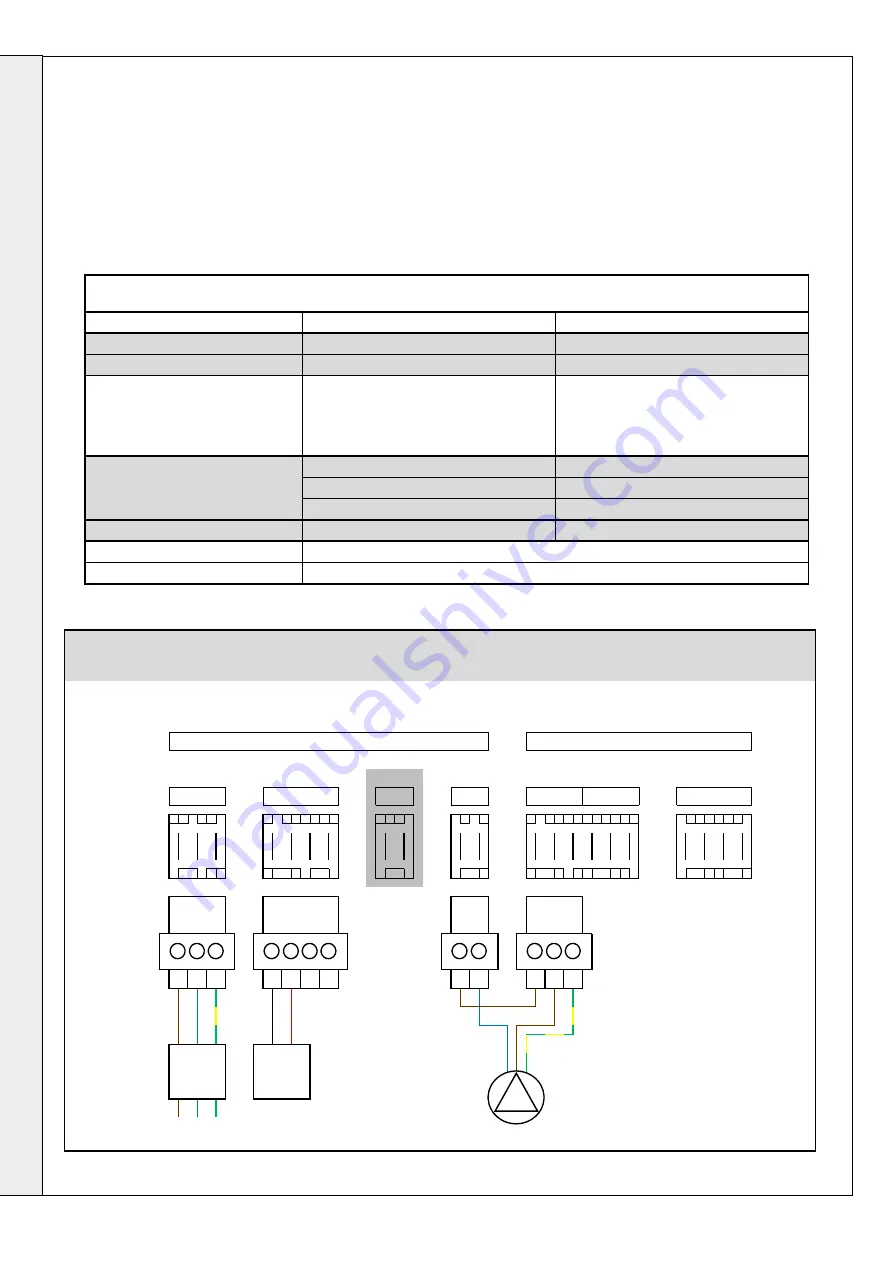
2.27 BOILER WITH EXTERNAL CONTROLS
1. The boiler must be provided with a 4 minute pump overrun
period. Failure to do so may invalidate the boiler warranty.
2. It is preferable that any pump used to circulate water
through an individual boiler is controlled by the local boiler.
Either as a 230V 50Hz supply as shown, enabled by the
Volts Free Contacts e.g. MFR1 or controlled by the option
kit for 0-10V pump control. If not then a pump overrun
function MUST be provided by the controlling system.
3. The pump load and switch on surge current must be within
the limits of the output if it is powered directly from the Volts
Free Contact. The limits are as specified in the Electrical
Specification Table below.
A slave contactor may be used to power the pump where
needed.
4. If the switched live is provided without a Volts Free Contact
then this MUST be taken from the same phase as the
boiler mains supply, preferable through the same isolator.
External
controls
via
switched
live
demand
Boiler
Pump
controlled
directly
from
MFR1
I1
I2
I3
I4
I5
I6
1
2
3
1
2
3
4
1
2
1
2
1
2
3
4
5
6
1
2
3
4
L
N
PE
Switched
Live
/
Volts
Free
Contact
Mains
Supply
External
Controls
Boiler
Pump
MFR3
MFR4
Volts
Free
Contacts
NO
PE
C
NO
C
NO
Mains
Voltage/230V
50Hz
C
NO
PE
C
MFR1
MFR2
~
L
N
230V
50Hz
Auxiliary
Fused
Spur
/
Isolator
SL1
L
SL2
L
~
L
N
PE
Mains
Supply
Demand
inputs
230V
50Hz
Interlock
External Controls via Switched Live Demand
Boiler pump controlled directly from MFR1
continued............
Electrical Specifications for External Connections
Voltage
Load
Input - SL1, SL2
230V 50Hz
3kΩ min
Input - 0-10V
0 to 10V DC
5mA max
Sensor - Outside
Sensor - Header
Sensor - Room
Sensor - DHW Tank
5V DC
10kΩ @ 25ºC β(25/85)=3977
Output - MFR1..4 output
24 V DC to 230V 50Hz
1.0 A max at CosØ = 0.6
230V 50Hz
Peak Surge 20A < 20ms
230V 50Hz
Peak Transient 100A < 10uS
Output - Pump 0-10V output
0 to 10V DC
10mA max
Bus - OT1, OT2
OpenTherm V 4.0
Bus - VariCAN
CAN Open, proprietary protocol
32
Installation & Servicing
SECTION 2 - INSTALLATION
INST
ALLA
TION
Содержание EVOMAX 2 30
Страница 4: ...4 Installation Servicing...
Страница 75: ...75 Installation Servicing NOTES...
Страница 76: ...76 Installation Servicing NOTES...
Страница 77: ...77 Installation Servicing NOTES...
Страница 78: ...78 Installation Servicing NOTES...
Страница 79: ...79 Installation Servicing NOTES...