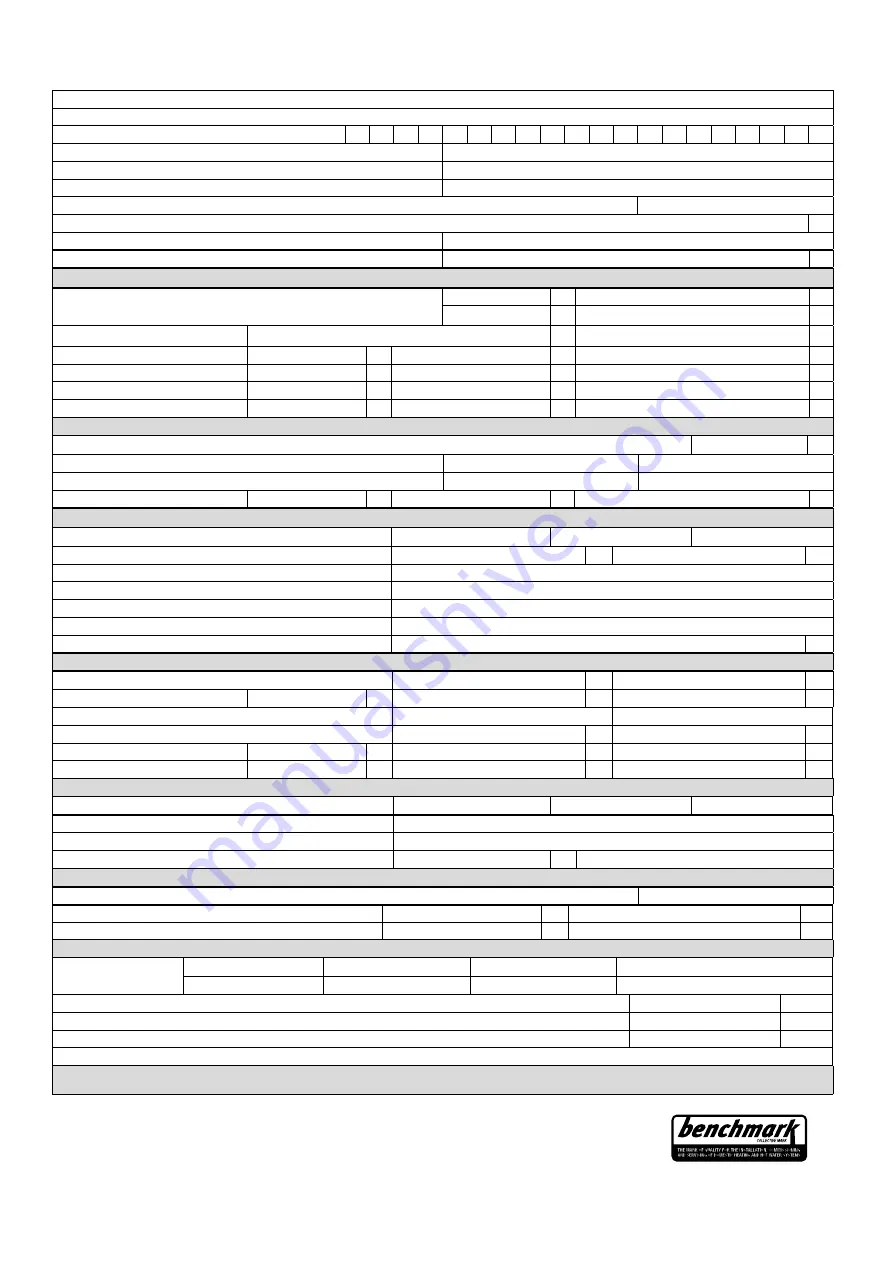
58
Installation and Servicing
Section 6 - Benchmark to Commissioning
© Heating and Hotwater Industry Council (HHIC)
www.centralheating.co.uk
* All installations in England and Wales must be notified to Local Authority Building Control (LABC) either directly or through a
Competent Persons Scheme. A Building Regulations Compliance Certificate will then be issued to the customer.
GAS BOILER SYSTEM COMMISSIONING CHECKLIST & WARRANTY VALIDATION RECORD
Address:
Boiler make and model:
Boiler serial number:
Commissioned by (PRINT NAME):
Gas Safe registration number:
Company name:
Telephone number:
Company email:
Company address:
Commissioning date:
Heating and hot water system complies with the appropriate Building Regulations? Yes
Optional: Building Regulations Notification Number (if applicable):
Boiler Plus requirements (tick the appropriate box(s))
Boiler Plus option chosen for combination boiler in ENGLAND
Weather compensation
Smart thermostat with automisation and optimisation
Load compensation
Flue Gas Heat Recovery
Time and temperature control to hot water
Cylinder thermostat and programmer/timer
Combination boiler
Zone valves
pre-existing
Fitted
Not required
Thermostatic radiator valves
pre-existing
Fitted
Not required
Automatic bypass to system
pre-existing
Fitted
Not required
Underfloor heating
pre-existing
Fitted
Not required
Water quality
The system has been flushed, cleaned and a suitable inhibitor applied upon final fill, in accordance with BS7593 and boiler manufacturers’ instructions
Yes
What system cleaner was used?
Brand:
Product:
What inhibitor was used?
Brand:
Product:
Primary water system filter
pre-existing
Fitted
Not required
CENTRAL HEATING MODE measure and record (as appropriate)
Gas rate (for combination boilers complete DHW mode gas rate)
m
3/
hr
or
ft
3
/hr
Central heating output left at factory settings?
Yes
No
If no, what is the maximum central heating output selected?
kW
Dynamic gas inlet pressure
mbar
Central heating flow temperature
°C
Central heating return temperature
°C
System correctly balanced/rebalanced?
Yes
COMBINATION BOILERS ONLY
Is the installation in a hard water area (above 200ppm)?
Yes
No
Water scale reducer/softener
pre-existing
Fitted
Not required
What type of scale reducer/softener has been fitted?
Brand:
Product:
Water meter fitted?
Yes
No
If yes- DHW expansion vessel
pre-existing
Fitted
Not required
Pressure reducing valve
pre-existing
Fitted
Not required
DOMESTIC HOT WATER MODE Measure and record
Gas rate
m
3/
hr
or
ft
3
/hr
Dynamic gas inlet pressure at maximum rate
mbar
Cold water inlet temperature
°C
Hot water has been checked at all outlets
Yes
Temperature °C
CONDENSATE DISPOSAL
The condensate drain has been installed in accordance with the manufacturers’ instructions and/or BS5546/BS6798
Yes
Point of termination
Internal
External (only where internal termination impractical)
Method of disposal
Gravity
Pumped
ALL INSTALLATIONS
Record the following
At max rate:
CO ppm CO
2
%
CO/CO
2
Ratio
At min rate (where possible)
CO ppm CO
2
%
CO/CO
2
Ratio
Where possible, has a flue integrity check been undertaken in accordance with manufacturers’ instructions, and readings are correct?
Yes
The operation of the boiler and system controls have been demonstrated to and understood by the customer
Yes
The manufacturers’ literature, including Benchmark Checklist and Service Record, has been explained and left with the customer
Yes
Commissioning Engineer’s signature
Customer’s signature
(To confirm satisfactory demonstration and receipt of manufacturers’ literature)
Time, temperature control and boiler interlock provided for central heating and hot water
Yes