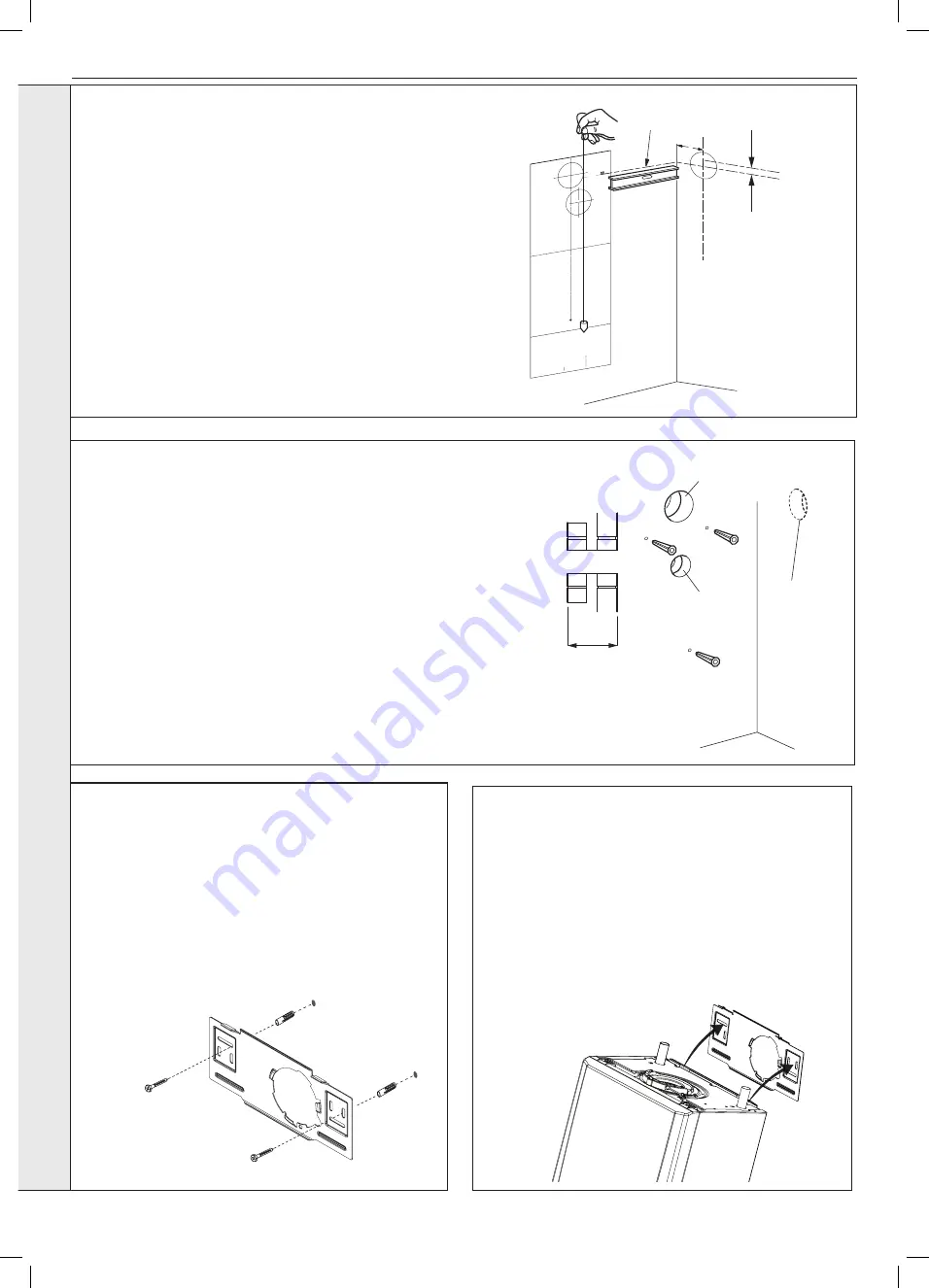
22
Installation and Servicing
SECTION 2 - INSTALLATION
A** - See Diagram in
Section 1.16
Extended centre line
155
(200)
IMPORTANT.
Ensure that, during the cutting operation, masonry falling outside of the
building does not cause damage or personal injury.
1.
Cut the rear flue hole (preferably with a 5” core boring tool), ensuring
that the hole is square to the wall.
Both wall faces immediately around the cut hole should be flat.
2.
Drill 3 holes with a 7.5mm / 8mm masonry drill and insert the plastic
plugs, provided, for the wall mounting plate and the boiler bottom
retaining bracket.
3.
Locate 2 No.14 x 50mm screws in the wall mounting plate (one at each
side, in any of the 3 holes provided at each side) and screw home.
205862-10070
X
Section
through wall
Note.
Check all of the hole
positions before drilling.
Alternative
Side flue only
5" diameter hole
Turret Rear
Flue - 5” dia
Alternative
Rear Flue
5” dia
The wall mounting template is located on the internal protective
packaging. The template shows the position of the fixing and rear
flue centre holes for a standard installation
Care MUST be taken to ensure the correct holes are drilled.
1.
Tape template into the required position, ensuring its squareness
by hanging a plumbline as shown.
2.
If fitting a side flue, extend the flue centreline onto the side by
155mm
on a standard wall fix or
200mm
if using a stand-off
bracket.
3.
Mark the following on to the wall:
a
The selected group of wall mounting screw holes.
b.
The centre position of the flue duct. Marking both the centre
and the circumference of the flue duct.
4.
Remove the template plate from the wall.
2.4 WALL MOUNTING TEMPLATE
2.5 PREPARING THE WALL
2.7 MOUNTING THE BOILER
(TURRET OPTION)
2.6 FITTING THE WALL MOUNTING
PLATE (TURRET OPTION)
Screw the wall mounting plate to the wall using 2 wall plugs
(previously fitted) with the 2 screws provided.
Choose one of the 2 sets of slots in left and right bank.
Ensuring that at least one of the screws is fitted into a top slot
and the mounting bracket is level.
205862-10084
Example of fixing
1. Remove the top flue plastic blanking disc and retain the
plastic horseshoe fixing and screw.
Caution: water may discharge from open pipes
2. Lift the boiler onto the wall mounting plate (refer to the
Introduction section for safe handling advice), locating it
over the two tabs.
3. Screw the boiler bottom retaining bracket to the wall with
the screw provided.
INST
ALLA
TION
Содержание LOGIC MAX HEAT H 12
Страница 4: ...4 Installation and Servicing ...
Страница 6: ...6 Installation and Servicing ...
Страница 61: ...61 NOTES Installation and Servicing ...
Страница 62: ...62 Installation and Servicing SECTION 5 SPARE PARTS ...
Страница 68: ...68 NOTES Installation and Servicing ...
Страница 69: ...69 NOTES Installation and Servicing ...