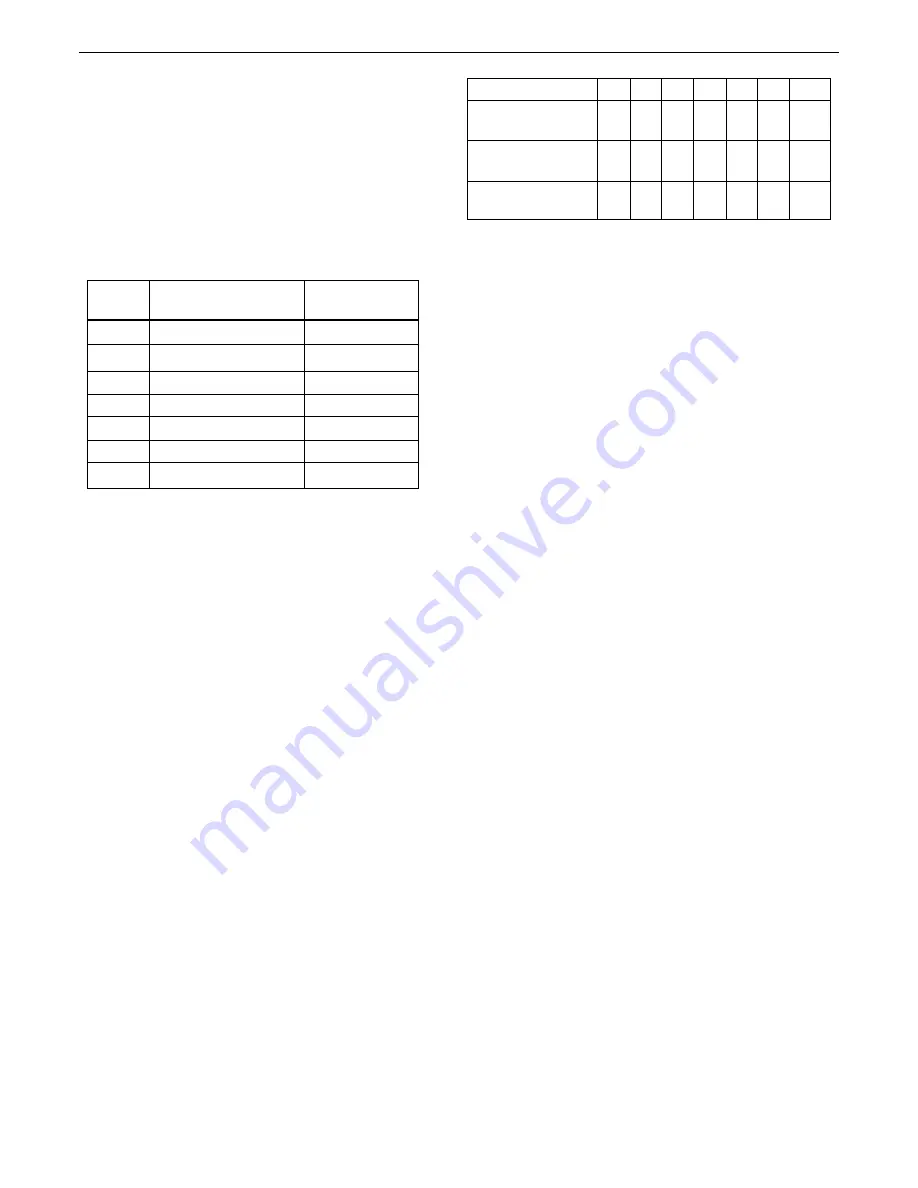
Classic
FF
-
Installation & Servicing
7
GENERAL
2. If the boiler is to be installed in a cupboard or compartment,
permanent air vents are required (for cooling purposes) in
the cupboard/compartment, at both high and low levels.
The air vents must either communicate with room/internal
space, or be direct to outside air. The minimum effective
areas of the permanent air vents, required in the cupboard/
compartment, are specified in Table 4 and are related to
maximum rated heat input.
3. Both air vents MUST communicate with the same room or
internal space or MUST be on the same wall to outside air.
4. In siting the air vents care must be taken to avoid the
freezing of pipework.
WATER CIRCULATION SYSTEM
The boiler must NOT be used for direct hot water supply. For the
types of system and correct piping procedure refer to 'Introduction'
and Frame 1.
The central heating system should be in accordance with BS.6798
and, in addition, for Smallbore and Microbore systems, BS. 5449.
The domestic hot water system, if applicable, should be in
accordance with the relevant recommendations of BS. 5546. Copper
tubing to BS. 2871:1 is recommended for water carrying pipework.
The hot water storage cylinder MUST be of the indirect type and
should preferably be manufactured of copper.
Single feed, indirect cylinders are not recommended and MUST
NOT be used on sealed systems.
The appliances are NOT suitable for gravity central heating, nor
are they suitable for the provision of gravity domestic hot water.
The hot water cylinder and ancillary pipework, not forming part of
the useful heating surface, should be lagged to prevent heat loss
and any possible freezing - particularly where pipes run through
roof spaces and ventilated under floor spaces.
Boilers not fitted to a sealed system must be vented.
IMPORTANT
A minimum length of 1m of copper pipe MUST be fitted to both
flow and return connections from the boiler before connection to
any plastic piping. This applies to ALL types of installation.
Draining taps MUST be located in accessible positions, which
permit the draining of the whole system - including the boiler
and hot water storage vessel. They should be at least
1/2" BSP
nominal size and be in accordance with BS. 2879.
The boiler is fitted with a special drain plug, which is provided, to
drain the BOILER ONLY, in the event of the system drain plug
being unable to do so. The hydraulic resistance of the boilers, at
MAXIMUM OUTPUT with an 11
O
C (20
O
F) temperature differential,
are shown in Table 5.
Maximum boiler operating temperature should be 82
o
C (180
o
F).
WATER TREATMENT
These boilers incorporate a cast iron heat exchanger.
IMPORTANT. The application of any other treatment to this
product may render the guarantee of Caradon Ideal Limited
INVALID.
Caradon Ideal Limited recommend Water Treatment in
accordance with the
Benchmark Guidance Notes on Water
Treatment in Central Heating Systems.
Caradon Ideal Limited recommend the use of Fernox, GE Betz
Sentinel or Salamander water treatment products, which must
be used on accordance with the manufacturers instructions.
For further information contact:
Fernox Manufacturing Co. Ltd, Cookson Electronics, Forsyth Road,
Sheerwater, Woking, Surrey. GU21 5RZ. Tel. +44 (0) 1799 521133
or
G E Betz Ltd, Sentinel Division, Foundry Lane, Widnes, Cheshire,
WA8 8UD. Tel. +44 (0) 151 424 5351
or
Salamander Engineering Ltd, Unit 24, Reddicap Trading Estate,
Sutton Coldfield, West Midlands B75 7BU. Tel. +44 (0) 121 378 0952
Notes.
1. It is most important that the correct concentration of the water
treatment products is maintained in accordance with the
manufacturers' instructions.
2. If the boiler is installed in an existing system any unsuitable
additives MUST be removed by thorough cleansing.
BS7593:1992 details the steps necessary to clean a
domestic heating system.
3. In hard water areas, treatment to prevent limescale may be
necessary - however the use of artificially softened water is
NOT permitted.
4. Under no circumstances should the boiler be fired before
the system has been thoroughly flushed.
BOILER CONTROL INTERLOCKS
Caradon Ideal Limited recommend that heating systems utilising
full thermostatic radiator valve control of temperature in individual
rooms should also be fitted with a room thermostat controlling the
temperature in a space served by radiators not fitted with such a
valve as stated in BS. 5449.
Central heating systems controls should be installed to ensure the
boiler is switched off when there is no demand for heating or hot water.
When thermostatic radiator valves are used, the space heating
temperature control over a living / dining area or hallway having a
heating requirement of at least 10% of the boiler heat output should
be achieved using a room thermostat, whilst other rooms are
individually controlled by thermostatic radiator valves. However, if
the system employs thermostatic radiator valves on all radiators,
or two port valves without end switches, then a bypass circuit must
be fitted with an automatic bypass valve to ensure a flow of water
should all valves be in the closed position.
Table 4 - High and low vent areas
Boiler
Air from room/internal
Air direct from
space, cm (in
2
)
outside, cm (in
2
)
FF330
102
(16)
51
(8)
FF340
135
(21)
68
(11)
FF350
170
(26)
83
(13)
FF360
198
(31)
102
(16)
FF370
231
(36)
116
(18)
FF380
264
(41)
132
(21)
FF3100
340
(52)
170
(26)
Boiler Size
FF
330
340
350
360
370
380
3100
Boiler
kW 8.8 11.7 14.6 17.6 20.5 23.4 29.3
Output Btu/h x 1000
30
40
50
60
70
80
100
Water Flow
l/min 11.4 15.2 19.0 22.8 26.5 30.3 38.0
Rate
gal/h 150 200 250 300 350 400 500
Pressure
mbar 22.0 20.4 31.5 41.7 54.8 77.0 106
Loss
in wg 8.9 8.3 12.6 16.7 22.0 30.9 42.5
Table 5 - Water flow rate and pressure loss
Содержание FF 330
Страница 39: ...Classic FF Installation Servicing 39 NOTES...