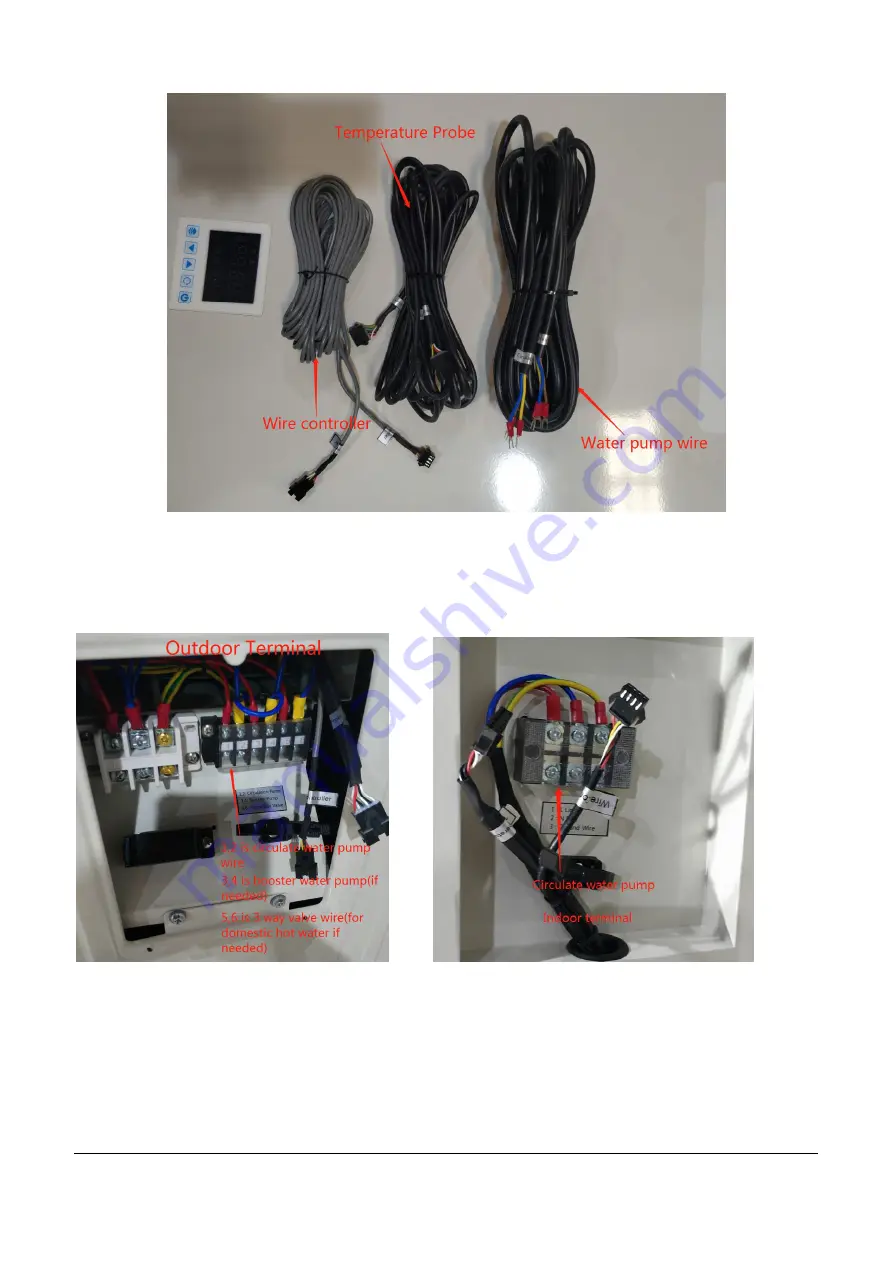
- 26 -
The three kinds of wires are in 1-1 mapping relationship with the connecting terminals. The connecting methods
are as follows
1.
Connect the circulate water pump wire to the wiring terminals(1 or 2) of the outdoor machine and the
indoor machine, as shown in the figure below.
Outdoor Terminal Indoor Terminal
2.
Connect the controller wire to the wire controller wiring terminal of the outdoor machine and the
indoor machine, as shown in the figure below:
Содержание ISW-10 SF1-DN1
Страница 21: ... 21 XD 05BSPM ...
Страница 56: ... 56 By sliding the button you can adjust the setting parameters Function buttons ...
Страница 65: ......