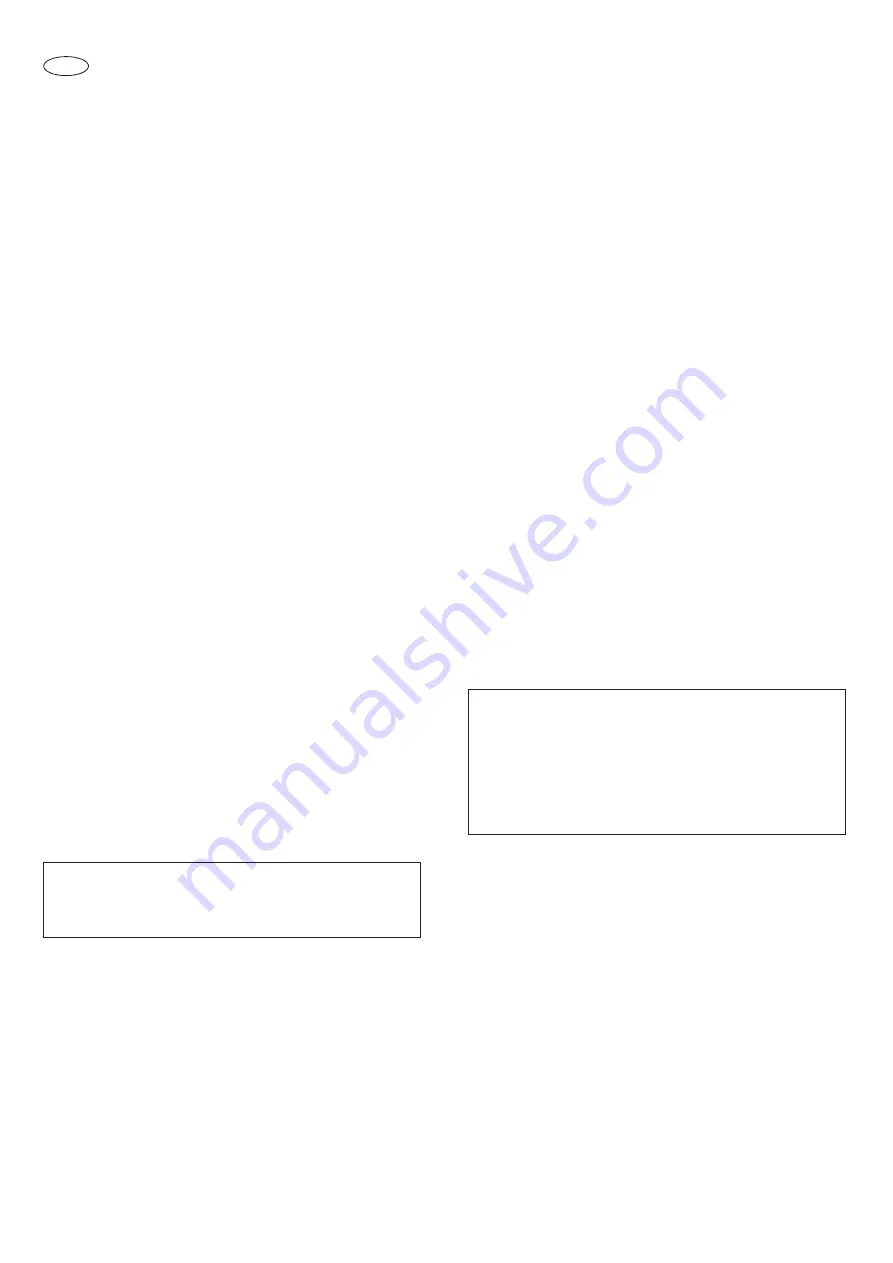
44
A GENERAL
The periods and the procedures for maintenan-
ce and cleaning are given as guides and are
not to be construed as absolute or invariable.
Cleaning, especially, will vary depending upon
local water and ambient conditions and the ice
volume produced; and, each icemaker must be
maintened individually, in accordance with its
particular location requirements.
B ICEMAKER
The followingmaintenance should be scheduled
at least two times per year on these icemakers.
1 Check and clean the water line strainer.
2 Remove the cover from the float reservoir -
care to do not damage the two water sensors
- and depress the float to make sure that a
full stream of water enters into the reservoir.
If not gently remove the float valve from its
reservoir bracket than clean the hole of the
nozzle.
3 Check that the icemaker is levelled in side to
side and in front to rear directions.
4 Check that the water level in the water reser-
voir is below the overflow but high enough
that it does not run out of the spout opening.
5 Clean the water system, water reservoir and
the interior of freezing cylinder using a solu-
tion of cleaner.
Refer to procedure C cleaning instructions
and after cleaning will indicate frequency
and procedure to be followed in local areas.
6 If required, polish the two sensor rods secu-
red to the float reservoir cover, heavy scale
sediment on them can be removed with the
help of a bit of cleaner.
7 With the ice machine and fan motor OFF on
air cooled models, clean condenser using
vacuum cleaner, whisk broom or non metallic
brush taking care to do not damage the con-
denser/ambient temperature sensor.
8 Check for water leaks and tighten drain line
connections.Pourwater down bin drain line to
be sure that drain line is open and clear.
9 Check the ice level control sensor to test
shut-off. Close the bottom of the ice chute
and wait till it is completely full of ice so to cut
off the light beam for at least 6 seconds.
This should cause the immediate blinking of
the Bin Full YELLOW LED located in the front
of P.C. Board and, 6 seconds later, the total
stopping of the ice maker with the simulta-
neous light up of the same LED (steady).
Within few seconds from the removal of the
ice between the sensor lights the ice maker
resume its operation.
10Check for refrigerant leaks and for proper
frost line, which should frost as far as approx.
20 cm (8") from the compressor.
11When doubtful about refrigerant charge,
install refrigerant gauges on corresponding
service valvesandcheckforcorrect refrige-
rantpressures.
12Check that fan blades move freely and are
not touching any surfaces.
NOTE.
Cleaning requirements vary accor-
ding to the local water conditions and indivi-
dual user operation.
NOTE:
The ice level control uses devices
that sense light, therefore they must be kept
clean enough so they can “see”.
Everythreemonthsremovetheopticalsystem
then clean/wipe the sensing “eyes” with a
clean soft cloth.
MAINTENANCE AND CLEANING INSTRUCTIONS
Содержание F 125C
Страница 17: ...15...
Страница 35: ...35 WIRING DIAGRAM F 80C Air cooled 220 240 50 1...
Страница 36: ...36 WIRING DIAGRAM F 80C Water cooled 220 240 50 1...
Страница 37: ...37 WIRING DIAGRAM F 125C Air water cooled 220 240 50 1...
Страница 38: ...38 WIRING DIAGRAM F 120 F 200 Air water cooled 220 240 50 1...
Страница 39: ...39 WIRING DIAGRAM SF 300 SF 500 Air water cooled 220 240 50 1...
Страница 40: ...40 WIRING DIAGRAM SF 500 Air water cooled 400 50 3...
Страница 41: ...41 WIRING DIAGRAM SFN 1000 Air water cooled 400 50 3...
Страница 47: ......