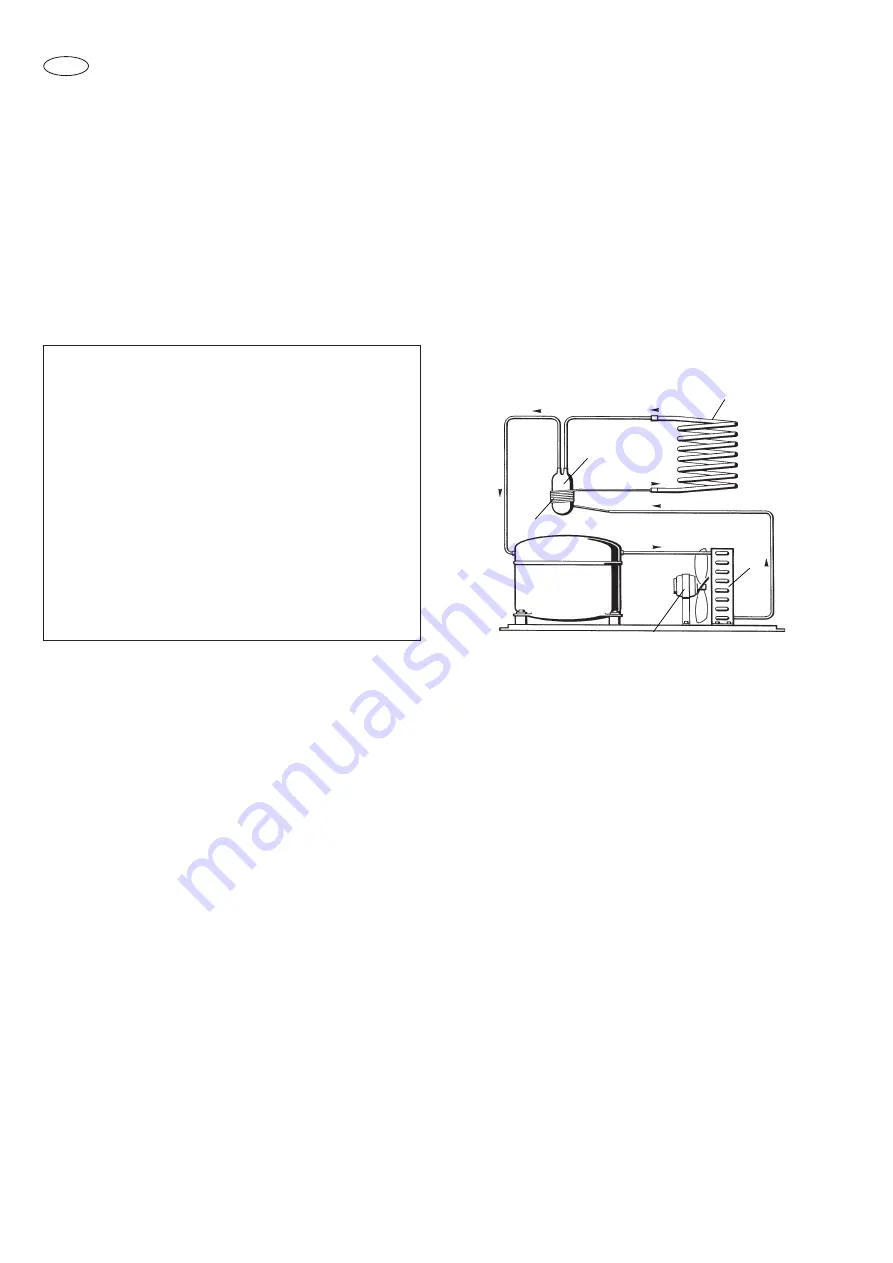
20
By running the ice maker, i.e. by putting the unit
under power, starts the automatic and conti-
nuous icemaking process which would not stop
until the ice storage bin gets filled-up to the
level of the control “eyes” located on the ice
chute. As the ice level raises to interrupt the
light beam running between the two infrared
leds, the unit stops after six seconds (compres-
sor first and 3' later the gear reducer), with the
simulteneous glowing of the
YELLOW LED
signalling the
“Full Bin”
situation.
As some ice gets scooped out from the storage
bin, the light beam between the two sensors
resumes (fast blinking of YELLOW LED) and six
seconds later the ice machine restarts the ice
making process - going always through the 3'
stand by - and the YELLOW LED goes off.
REFRIGERANT CIRCUIT
The hot gas refrigerant discharged out from the
compressor reaches the condenser where,
being cooled down, condenses into liquid.
Flowing into the liquid line it passes through the
drier filter, then it goes all theway throughtheca-
pillary tubewhere it looses some of its pressure
so that its pressure and temperature are lowe-
red.
Next, the refrigerant enters into the evaporator
coil wrapped around the freezer inner tube.
The water being constantly fed at the interior of
thefreezer inner tube,exchange heat with the
refrigerant circulating into the evaporator coil,
this cause the refrigerant to boil-off and evapo-
rate, there by it changes from liquid into vapor.
The vapor refrigerant then passes through the
suction accumulator and through the suction line
where the refrigerant exchanges heatwith the
one flowing into the capillary tube (warmer) befo-
rebeingsuckedinto thecompressor to be recircu-
lated.
The refrigerant head pressure is kept between
two pre-set values (8¸9 bar -110¸125 psig on
F120 and 17¸18 bar - 240¸250 psig on F200,
SF300, SF500 and SFN1000) by the condenser
temperature sensorwhich has its probe loca-
tedwithin the condenser fins - in air cooled ver-
sions.
This condenser temperature sensor, when sen-
ses a rising of the condenser temperature
beyond thepre-fixedlimit,changesits electrical
resistance and send a low voltage power flow to
the
MICROPROCESSOR
of the P.C. Board
which energizes,
through a
TRIAC
, the Fan Motor in ON-OFF
mode.
On the water cooled versions, the refrigerant
head pressure is kept at the constant value of 8.5
bar 8.5 bar (120 psig) on F200 and of 17 bar
(240 psig) on F200, SF300, SF500 and SFN1000
by themetered amount ofwater passing through
the condenserwhich is regulated by the action of
theWater Regulating Valve that has its capillary
tube connected to the liquid refrigerant line. As
pressure increases, the water regulating valve
opens to increase the flow of cooling water to
the condenser.
NOTE.
The interruption of the light beam
between the two light sensors is immediately
signalled by the blinking of the
BIN FULL
YELLOW LED
located on the front of the
P.C. Board.
After about
6" of steady interruption
of the
light beam the unit stops and the
“Full Bin”
YELLOW LED
glows steady.
The six seconds of delay prevent the unit
from stopping for any undue reason like the
momentarily interruption of the light beam
caused by the flakes that slides along the ice
spout before dropping into the bin.
ACCUMULATOR
CAPILLARY TUBE
DISCHARGE LINE
EVAPORATOR
FAN MOTOR
COMPRESSOR
C
O
N
D
E
N
S
E
R
S
U
C
TI
O
N
L
IN
E
Содержание F 125C
Страница 17: ...15...
Страница 35: ...35 WIRING DIAGRAM F 80C Air cooled 220 240 50 1...
Страница 36: ...36 WIRING DIAGRAM F 80C Water cooled 220 240 50 1...
Страница 37: ...37 WIRING DIAGRAM F 125C Air water cooled 220 240 50 1...
Страница 38: ...38 WIRING DIAGRAM F 120 F 200 Air water cooled 220 240 50 1...
Страница 39: ...39 WIRING DIAGRAM SF 300 SF 500 Air water cooled 220 240 50 1...
Страница 40: ...40 WIRING DIAGRAM SF 500 Air water cooled 400 50 3...
Страница 41: ...41 WIRING DIAGRAM SFN 1000 Air water cooled 400 50 3...
Страница 47: ......