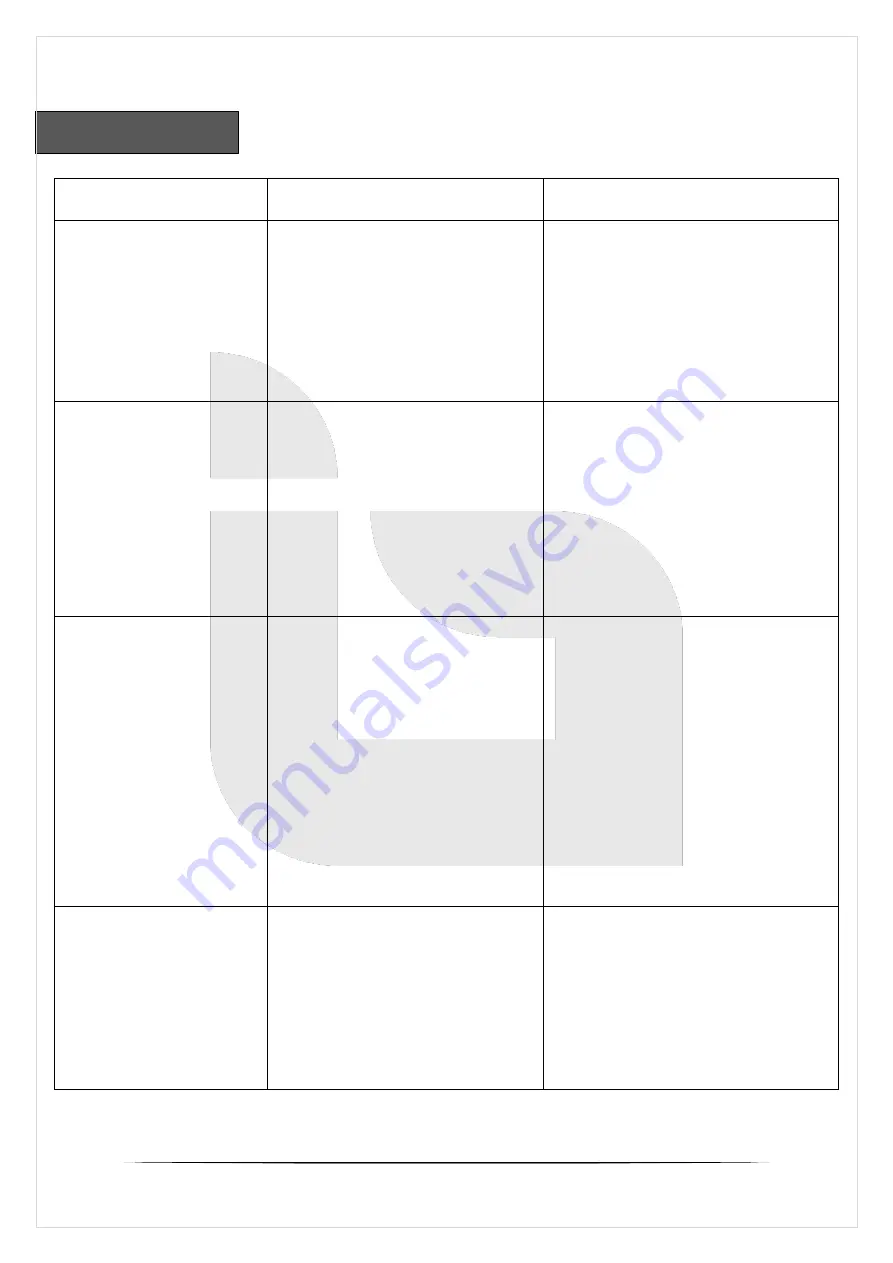
19
Problem
Possible Cause
Solution
1.
Wire feeds,
but no arc
1.1 Poor grounding/
ground connection.
1.2 Trigger not pulled
while wire is in
contact with work.
1.1 Check connection/
Tighten ground cable
.
1.2
Press the trigger
while in contact
with the workpiece.
2. Arc works, but
not feeding
wire
2.1 Insufficient or
excessive pressure
on the drive roller.
2.2 Wire reel/spool is
empty.
2.1 Adjust the drive
pressure.
(See page no.13)
2.2
Check if wire is in
place and replace if
necessary.
3.
No arc or wire
feed.
3.1 Exceeded duty
cycle (>60%);
[Thermal protector
engaged]
3.2 Insufficient air
flow/ Overheat.
3.3 Circuit breaker
has been tripped.
3.1
Allow it to cool at
least 10 minutes
with machine ON.
3.2
Check the vents on all
sides of the machine
for any obstacles.
3.3
Make sure circuit
breaker is reset.
4. Poor quality
welds.
4.1 Gun moved over
workpiece too
quickly/too slowly
.
4.2 Insufficient
amperage.
4.1 Move the gun in a
standard manner.
4.2 Enhance the welding
current.
MAG WELDING
IBL M200-105
Содержание IBL M200-105
Страница 1: ...FLUX CORED MAG MMA IBL M200 105 WELDING MACHINE OPERATORS MANUAL ...
Страница 2: ...1 ...