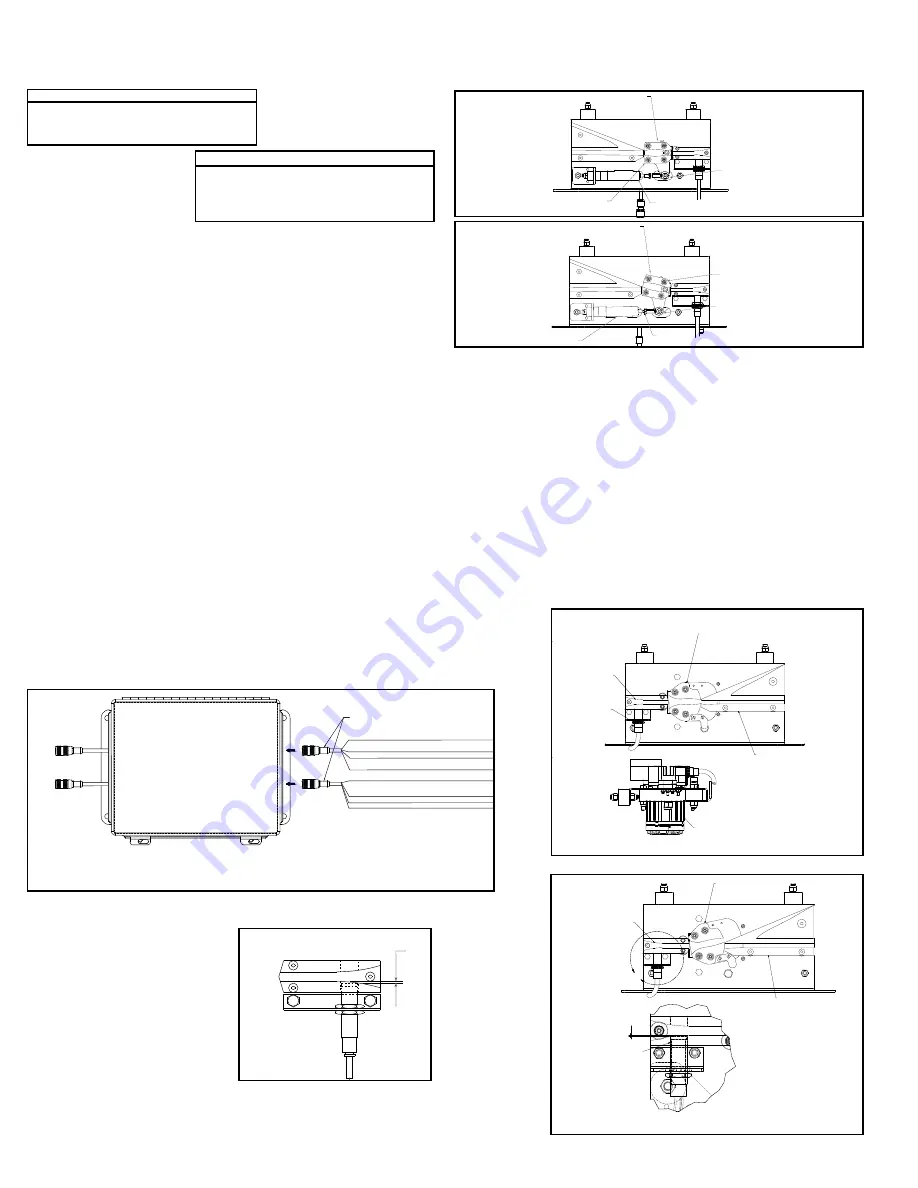
that the packages are truly spaced properly. Attempting to sort packages with too
little gap between them can cause jams.
Note: The minimum gap necessary for sorting a package is a function of the width
of the package. The charts below should be used in checking for proper gap.
* W = Maximum Package Width
Note: When sorting to both
sides, the minimum gap from the
above charts must be increased
by 3 in.
Jam/Confirmation Photo-eye
—Photo-eyes mounted on each take-away spur of
the sorter, as close to the sorter as possible. These eyes perform two functions:
1. Detect a product jam at the sorter “exit point.” If a package blocks this photo-eye
for a longer time than it would take for the package to travel past the photo-eye
normally, this indicated that the package is jammed. The sorter should be stopped
and the jam cleared before restarting the sorter.
2. Divert confirmation. If a divert signal is given to a particular divert point, and no
package is detected by the associated jam/confirmation photo-eye, an error has
occurred. The sorter should be stopped and the error found and corrected before
restarting the sorter.
Full Line Photo-eye
—Photo-eyes mounted on each divert lane from the sorter,
near the infeed end of that lane. These eyes are used to signal the system controls
that a particular divert lane is full. The controls should then send any further
packages assigned to that lane to the recirculation line until the full line photo-eye
on that lane no longer indicates the full condition.
Recommended Controls Procedures
The following are recommendations to assist in the design and installation of
system controls that are interfacing with ProSort sorters.
• Do not place 24VDC control wires in the same wireway with AC power wires,
especially if the AC power exceeds 240 volts. “Noise” produced in the control wires
by the power wires may produce undesirable effects.
• Do not use optional “standard prox output” of the smart prox as a substitute for
an encoder. The five inch spacing between divert shoes does not provide enough
tracking resolution to accurately sort packages.
• Do not use manual override operator of the solenoid air valve to operate a divert
switch while the sorter is running. Doing so bypasses the switch timing controls and
may cause switch damage or a sorter crash.
• Do treat the tripping of any safety switch, motor overload, or low air pressure
signal as an emergency stop. Inspect the safety switch and other parts of the
sorter to be sure everything is in good working order before starting or restarting
the sorter.
• Pneumatic Divert
Switch Checklist
After all ProSort sections are installed
and aligned, each divert switch should be
checked for proper operations as follows:
1. Before air pressure is supplied to the
divert switch solenoid air valve, manually
pivot the switch back and forth between
the non-divert and divert position
checking for a free and smooth pivoting
movement. Determine and remedy the
cause of any switch binding. For proper switch alignment see figures 8C & 8D.
If switch adjustment is necessary, loosen the jam nut on the cylinder rod. Screw
cylinder rod into or out of rod end to adjust the switch and retighten jam nut.
2. Turn air pressure on and verify that each divert switch is in, or moves to, the
home (non-divert) position (Figure 8C).
3. Check to insure that the smart prox is set properly. The face of the prox should
be set just out of the shoe pin guide path in the switch guide (Figure 8B)
•Electric Divert Switch Checklist
NOTE: All electric divert servo motors are paired with the associated drives at the
factory. Connecting motors to the wrong drive may have an adverse effect on the
divert operation and could result in physical damage to the sorter. Always connect
the drives to the factory paired motors to prevent damage.
1. Before running the sorter, apply power to the electric switch system and verify
that the diverts are fully in either the home or diverted position. Divert function was
tested at the factory to ensure proper operation. If the diverts are in the diverted
position, they can be returned to the home position, Figure 8E by removing the
enable signal to the Smart Prox and then flagging the Smart Prox to trigger a
move operation.
2. Each time diverts are powered on, the diverter will move slowly until it finds the
home position.
3. Ensure that the “All Systems Go” signal is on before running the sorter.
4. Check to ensure that the Smart Prox is set properly. The face of the prox should
be set just out of the shoe pin guide path in the switch guide (Figure 8F).
SWITCH BLOCK
(INTERRUPTOR DE
BLOQUEO)
ROD END
(EXTREMO DEL EJE)
NON-DIVERT POSITION
(POSICION DESVIADORA)
AIR CYLINDER EXTENDER
(EXTREMO DEL EJE)
SWITCH BLOCK
(INTERRUPTOR DE
BLOQUEO)
ROD END
(EXTREMO DEL EJE)
DIVERT POSITION
(POSICION DESVIADORA)
AIR RETRACTED
(EXTREMO DEL EJE)
JAM NUT
(CONTRA TUERCA)
FIGURE 8D
* BROKEN PROX OUTPUT IS ONLY ACTIVE WHEN SORTER RUN INPUT IS ACTIVE.
BROWN/
CAFÉ
NOT USED
BLACK/
NEGRO
OUPUT (24V=OK, 0V=MISSING BEARING DETECTED)
SALIDA (24 V = CORRECTO, 0 V = COJINETE FALTANTE DETECTADO)
BLUE/
AZUL
COMMON/
COMÚN
WHITE/
BLANCO
BROKEN PROX ERROR (24=OK, 0V=ERROR)/
ERROR DE SENSOR DE PROXIMIDAD DAÑADO (24 = CORRECTO, 0 V = ERROR)
BROWN
/
CAFÉ
POWER (+24VDC)/
ENERGÍA (+24 V CC)
BLACK/
NEGRO
RESET ERROR INPUT/
ENTRADA DE ERROR DE RESTABLECIMIENTO
BLUE
/
AZUL
COMMON/
COMÚN
WHITE
/
BLANCO
SORTER RUNNING INPUT (SORTER UP TO SPEED)
ENTRADA DE CLASIFICADOR EN FUNCIONAMIENTO
(CLASIFICADOR A VELOCIDAD NORMAL)
941.423003
OUTPUT
INPUT
TO PROX 2
TO PROX 1
(HACIA SENSOR DE
PROXIMIDAD 1)
(HACIA SENSOR DE
PROXIMIDAD 2)
(SALIDA)
(ENTRADA)
(LA SALIDA DE SENSOR DE PROXIMIDAD DAÑADO SOLO SE ACTIVA CUANDO LA
ENTRADA DE FUNCIONAMIENTO DEL CLASIFICADOR ESTÁ ACTIVA.)
FIGURE 8A
FIGURE 8C
1/32"
FIGURE 8B
V
V
NON-DIVERT POSITION
SERVO MOTOR
DIVERT BLOCK
PROX SWITCH
SWITCH GUIDE
NON-DIVERT POSITION
(POSICIÓN SIN DESVIACIÓN)
(GUÍA DEL
INTERRUPTOR)
(INTERRUPTOR
DE PROXIMIDAD)
(BLOQUE DE DESVIACIÓN)
(POSICIÓN SIN DESVIACIÓN)
(SERVOMOTOR)
FIGURE 8E
U
DIVERT POSITION
DIVERT BLOCK
SWITCH GUIDE
SWITCH BLOCK
PROX SWTICH
DETAIL U
SCALE 1.50 : 1
1/32
(BLOQUE DEL
INTERRUPTOR)
(GUÍA DEL
INTERRUPTOR)
(INTERRUPTOR
DE PROXIMIDAD)
(BLOQUE DE
DESVIACIÓN)
(POSICIÓN DE
DESVIACIÓN)
(DETALLE U)
(ESCALA 1.50: 1)
FIGURE 8F
ProSort 121 (22° Diverts)
0” < W ² 6”
Minimum gap = 6”
6” < W ² 18”
Minimum gap = 9”
18” < W ² 30”
Minimum gap = 12”
ProSort 131 (30° Diverts)
0” < W ² 6”
Minimum gap = 6”
6” < W ² 12”
Minimum gap = 9”
12” < W ² 18”
Minimum gap = 12”
18” < W ² 24”
Minimum gap = 15”
8