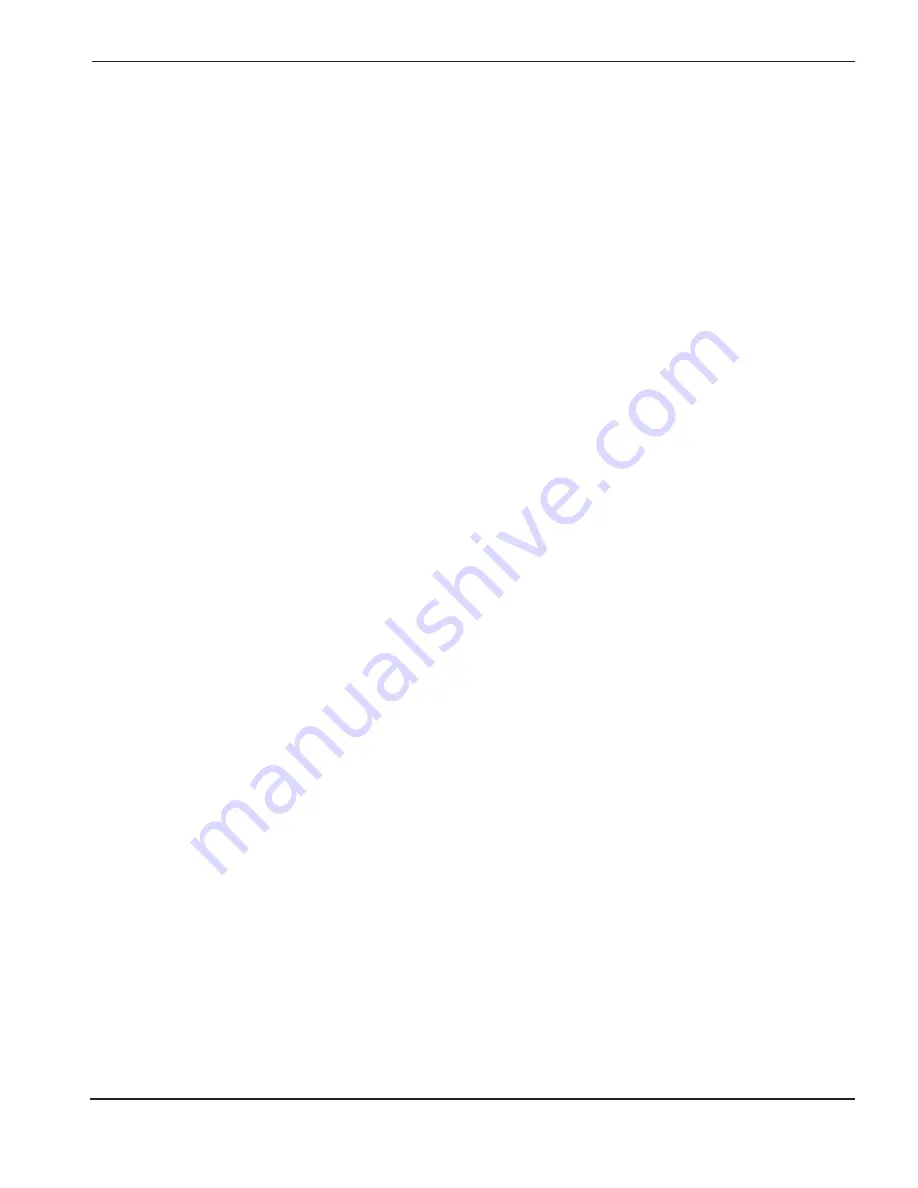
ELECTROMAGNETIC COMPATIBILITY (EMC)
Hypertherm
i
4-08
EMC Introduction
Hypertherm’s CE-marked equipment is built in compliance
with standard EN60974-10. The equipment should be
installed and used in ac cor dance with the information
below to achieve elec tro mag net ic compatibility.
The limits required by EN60974-10 may not be adequate
to com plete ly eliminate in ter fer ence when the affected
equip ment is in close proximity or has a high degree of
sensitivity. In such cases it may be nec es sary to use other
mea s ures to fur ther reduce interference.
This cutting equipment is designed for use only in an
indus tri al environment.
Installation and use
The user is responsible for installing and using the plasma
equipment according to the manufacturer’s instructions.
If elec tro mag net ic disturbances are detected then it shall
be the re spon si bil i ty of the user to re solve the situation
with the technical as sis tance of the man u fac tur er. In some
cases this remedial action may be as sim ple as earthing
the cutting circuit, see
Earthing of Workpiece
. In other
cas es it could in volve con struct ing an elec tro mag net ic
screen enclosing the pow er source and the work
complete with associated input filters. In all cases
electromag net ic dis tur banc es must be reduced to the
point where they are no longer trou ble some.
Assessment of area
Before installing the equipment the user shall make an
assessment of po ten tial elec tro mag net ic problems in the
sur round ing area. The following shall be taken into
account:
a. Other supply cables, control cables, signalling and
telephone ca bles; above, below and adjacent to the
cutting equip ment.
b. Radio and television transmitters and receivers.
c. Computer and other control equip ment.
d. Safety critical equipment, for example guarding of
industrial equipment.
e. Health of the people around, for example the use of
pacemakers and hear ing aids.
f. Equipment used for calibration or mea sure ment.
g. Immunity of other equipment in the en viron ment. User
shall ensure that other equip ment being used in the
environment is com pat i ble. This may require ad di tion al
protection measures.
h. Time of day that cutting or other ac tiv i ties are to be
carried out.
The size of the sur round ing area to be considered will
depend on the structure of the building and other
activities that are tak ing place. The surrounding area may
ex tend beyond the bound aries of the pre mises.
Methods of reducing emissions
Mains supply
Cutting equipment must be con nect ed to the mains
supply according to the man u fac tur er’s recommendations.
If interfer ence occurs, it may be necessary to take
additional precautions such as filtering of the mains supply.
Consideration should be given to shield ing the supply
cable of per ma nent ly installed cutting equip ment, in
metallic conduit or equiva lent. Shield ing should be
electrical ly continuous through out its length. The shielding
should be connected to the cutting mains supply so that
good electrical contact is maintained between the conduit
and the cutting pow er source enclosure.
Maintenance of cutting equipment
The cutting equipment must be rou tine ly main tained
according to the man u fac tur er’s rec om men da tions. All
access and service doors and covers should be closed
and properly fastened when the cutting equipment is in
op er a tion. The cutting equipment should not be modified
in any way except for those chang es and adjust ments
covered in the manufacturer’s instructions. In par tic u lar,
the spark gaps of arc striking and stabilizing devices
should be adjusted and maintained according to the
manufacturer’s rec om men da tions.
Cutting cables
The cutting cables should be kept as short as possible
and should be po si tioned close together, running at or
close to the floor level.
Equipotential bonding
Bonding of all metallic components in the cutting
installation and adjacent to it should be considered.
However, metallic com po nents bonded to the workpiece
will increase the risk that the op er a tor could receive a
shock by touch ing these metallic compo nents and the
electrode (nozzle for laser heads) at the same time.
The op er a tor should be in su lat ed from all such bonded
metallic components.
Содержание Command THC
Страница 61: ...SETUP CommandTHC for X Y Table Instruction Manual 3 7 5 Blank...
Страница 81: ...HD3070 SETUP CommandTHC for X Y Table Instruction Manual 3a 1 5 Section 3a HD3070 SYSTEM INTERCONNECTIONS...
Страница 88: ...HT2000 SETUP CommandTHC for X Y Table Instruction Manual 3b 1 6 Section 3b HT2000 SYSTEM INTERCONNECTIONS...
Страница 95: ...HT2000LHF SETUP CommandTHC for X Y Table Instruction Manual 3c 1 5 Section 3c HT2000LHF SYSTEM INTERCONNECTIONS...
Страница 102: ...HT4001 SETUP CommandTHC for X Y Table Instruction Manual 3d 1 5 Section 3d HT4001 SYSTEM INTERCONNECTIONS...
Страница 108: ...MAX100 SETUP CommandTHC for X Y Table Instruction Manual 3e 1 5 Section 3e MAX100 SYSTEM INTERCONNECTIONS...
Страница 113: ...MAX200 SETUP CommandTHC for X Y Table Instruction Manual 3f 1 6 Section 3f MAX200 SYSTEM INTERCONNECTIONS...
Страница 126: ...HT4400 SETUP CommandTHC for X Y Table Instruction Manual 3h 1 5 Section 3h HT4400 SYSTEM INTERCONNECTIONS...
Страница 135: ...HPR SETUP CommandTHC for X Y Table Instruction Manual 3i 1 9 Section 3i HPR SYSTEM INTERCONNECTIONS...
Страница 148: ...HPR SETUP 3i 14 CommandTHC for X Y Table Instruction Manual Figure 3i 14 Ohmic contact wire connection B B 11...
Страница 149: ...HSD130 SETUP CommandTHC for X Y Table Instruction Manual 3j 1 11 Section 3j HSD SYSTEM INTERCONNECTIONS...
Страница 188: ...MAINTENANCE CommandTHC for X Y Table Instruction Manual 5 15 6 Figure 5 7 Control board...
Страница 192: ...PARTS LIST CommandTHC for X Y Table Instruction Manual 6 3 10 Figure 6 2 THC control module interior...
Страница 220: ...CommandTHC for X Y Table Instruction Manual...