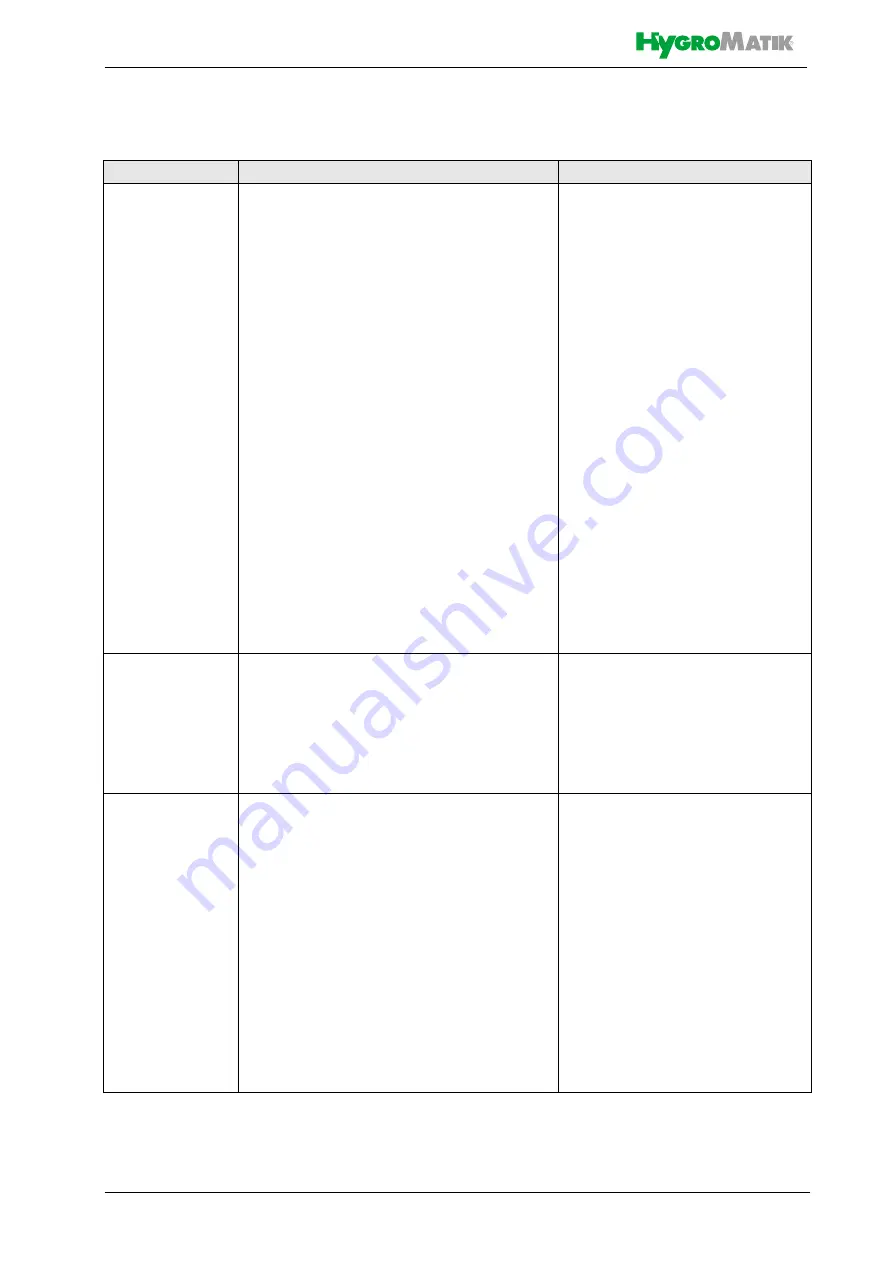
Page 73
12.2 Table of functional disrup-
tions
Problem
Possible cause for faulty situation
Counter measure
Set humidity level
not reached
•
Output limitation parameter setting im-
peds full power output
•
Check 1-1 parameter setting
•
Nominal unit output insufficient
•
Check unit technical data, air-
flow and secondary airflow
•
Phase failure
•
Check circuit breakers
•
Lengthy steam hose layout crossing cold
and drafty rooms may lead to increased
condensate formation
•
Change unit installation location
allowing for shorter steam hose.
Insulate steam hose
•
Improper steam manifold installation may
cause condensate formation within air
duct
•
Check steam manifold position
within total system and installa-
tion correctness
•
Control signal not properly selected or
software setting mismatch
•
Check control signal and 1-2
parameter setting
•
Water quality requires water concentra-
tion for full steam output
•
Wait
•
Excessive pressure in duct system
caused by e.g. water bags or partly
blocked steam pipes (max. overpressure
is 1200 Pa)
•
Eleminate particular cause(s)
Excessive humi-
dity
•
A steam output limitation setting that is
too high may result in poor control perfor-
mance and even condensate formation in
ducts
•
Check 1-1 parameter setting
•
Control signal not properly selected or
software setting mismatch
•
Check control signal and 1-2
parameter setting
Water collects on
bottom plate
•
Cylinder improperly reassembled follow-
ing maintenance:
- O-ring not replaced, defective or not in
place
- Flange (tongue and groove) damaged
- Flange improperly composed
-
Mineral deposits in flange area
•
Clean cylinder and assemble /
install properly
•
Cylinder improperly inserted in cylinder
base
•
Using moistened new O-ring, in-
sert steam cylinder properly into
cylinder base
•
Water cannot drain freely when pumped
from cylinder
•
Make sure drain is unobstructed