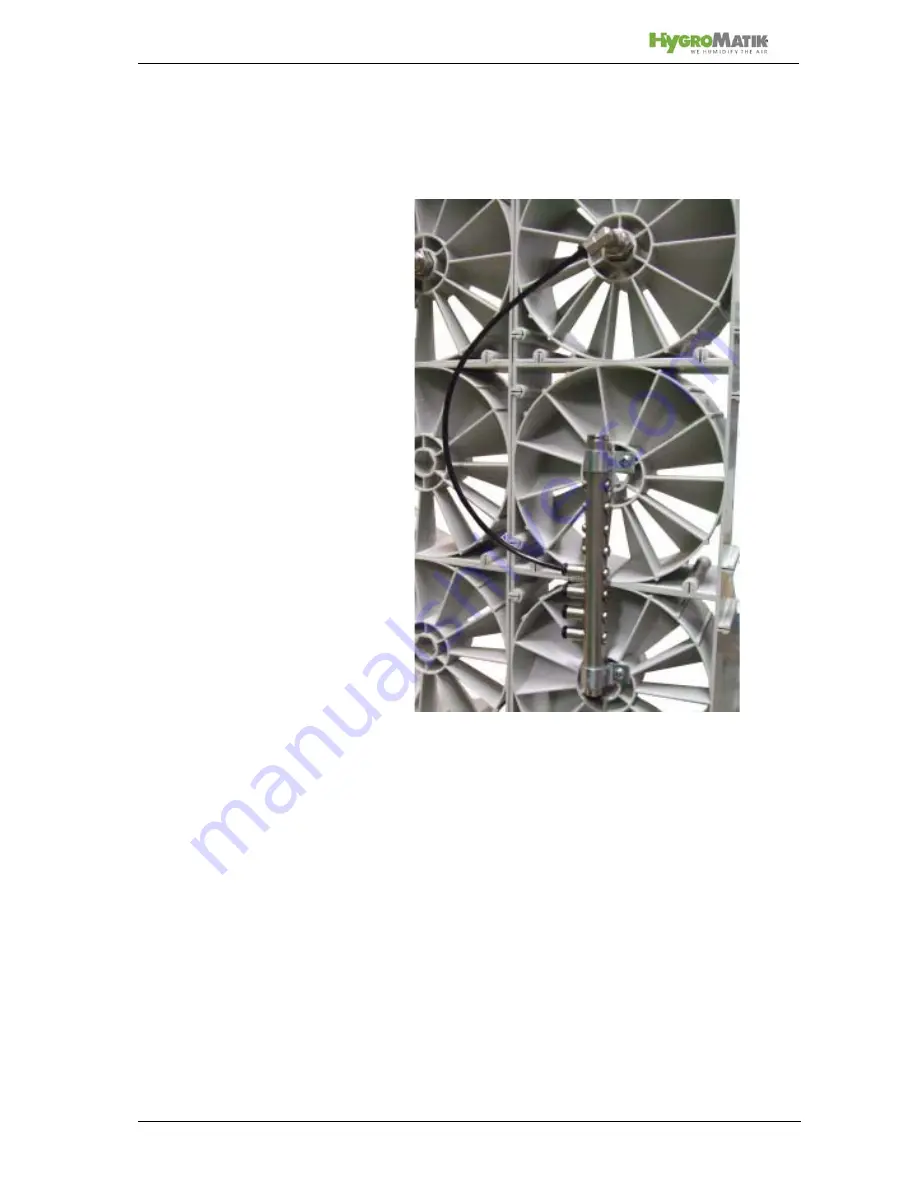
Page 28
The completed finished hose connection should look like this:
Manifold - Pump Station
In the standard version a 6/4 hose leads from the pump station
to a manifold. However, if the LPS nozzle system is equipped
with a partial/full load switch, then there is a 6/4 hose line lead-
ing to two manifolds.
Since the 6/4 hose line goes through the air conditioning duct a
duct wall grommet is provided (or two in the case of a partial/full
load switch).
Содержание LPS
Страница 1: ...LPS Humidifies and Cools ÁLPS Ä4 3Ö ENhÈ LPS 20130619 EN Operating manual ...
Страница 37: ...Page 37 8 Dimensions Pump Station View from below Side view Rear view ...
Страница 62: ...Page 62 14 2 3 1 Menu structure and parameter setting 4 3 ...
Страница 63: ...Page 63 15 EC declaration of conformity ...
Страница 69: ...Page 69 4 3 ...