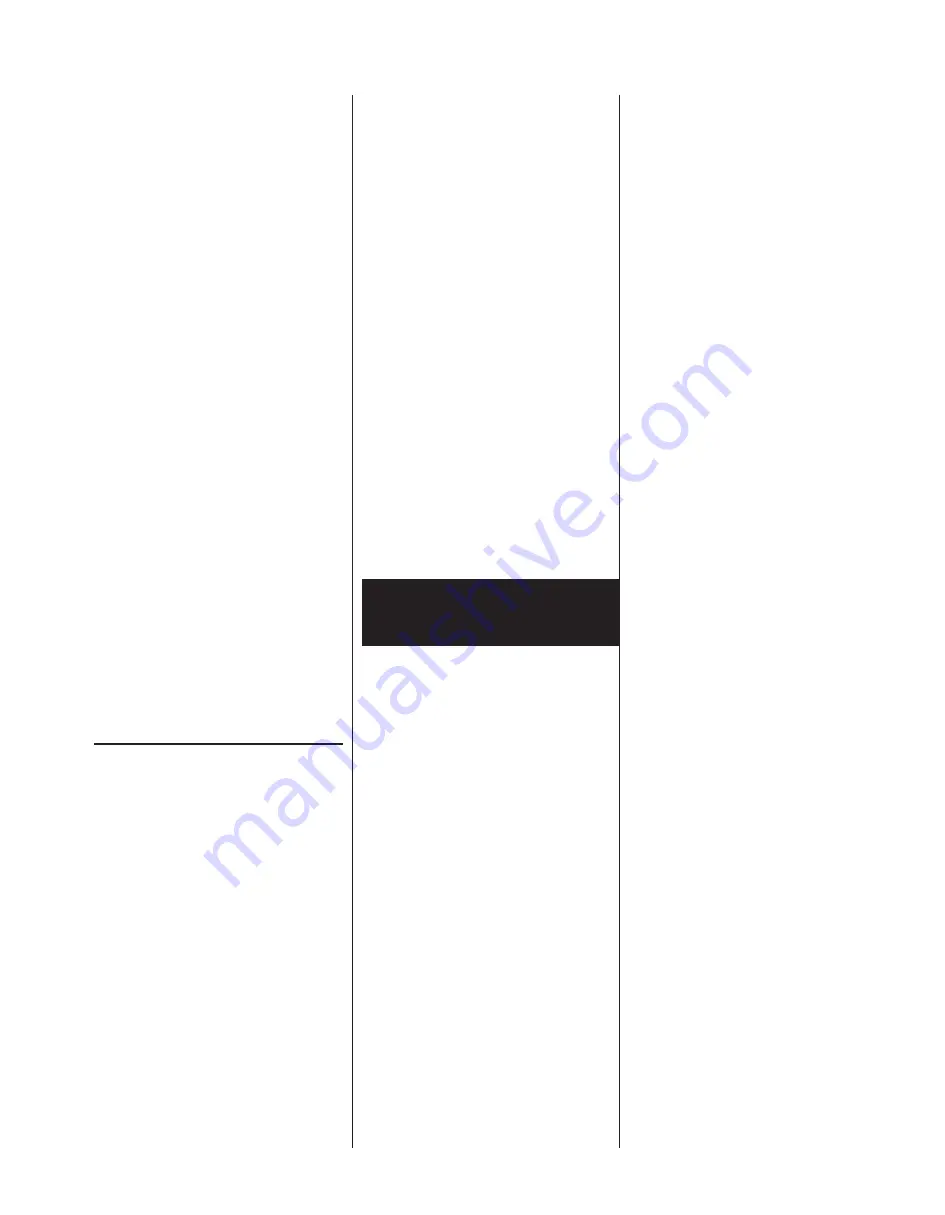
3
Pump Not Operating
or in Storage:
Pumps with carbon ceramic seals
must have impellers manually
rotated (6 revolutions) after
setting nonoperational for 3
months or longer and prior to
electrical start-up.
Pumps with tungsten carbide seals
must have impellers manually
rotated (6 revolutions) after
setting nonoperational for 3
weeks or longer and prior to
electrical start-up.
Codes:
All codes must be observed.
Consult with the local inspector
before installation to avoid
costly delays. Hydromatic is not
responsible for any expense
incurred to meet local codes
Installation
Instructions
1. Concrete Basin(s)
Pour one or two concrete systems
(one for pumps and control, etc.
and one for valves, if required)
or obtain precast concrete rings.
A 45-degree slope may be poured
around the inside perimeter of
the basin at the bottom to
prevent solids buildup providing
the slope does not interfere
with the discharge elbow and
pump locations. Before beginning
the installation, refer to the
Installation Data as found in the
Hydromatic Engineered Products
Catalog.
Follow the Installation Data
taking into account the location
of the discharge pipe, inlet pipe,
controls, vent pipe, and anchoring
requirements of the discharge
elbow(s). (All of the above concrete
work to be done by others.)
2. Discharge Elbow Installation
See Installation Data for the
proper location of the discharge
elbow on the basin bottom. Either
cast 5⁄8” anchor bolts into basin
bottom protruding 2” from basin
floor with 5⁄8” lock washers and
nuts securing, or drill holes for
expansion lag screws to secure
elbow to basin bottom. Each
elbow requires four anchors (all
furnished by others). Each elbow
must be level. Length of anchors
embedded in concrete varies
with materials used, but must
be sufficient to withstand the
weight, torque, and thrust loads
imposed by the pump.
3. Discharge Piping
(All supplied by others)
Install vertical discharge piping
modules to elbow using bolts,
nuts, lock washers, and gasket.
NOTE:
When
increasing
the pipe size at the discharge
elbow an eccentric flanged
reducer coupling may be
required to avoid interference
with the guide rail. See
Installation Data.
Install remainder of the sump
discharge piping. This typically
includes a vertical run of
piping appropriately sized and
configured to mate with the
vertical discharge piping, a ninety
degree elbow, and a horizontal
run of piping appropriately sized
and configured to mate with the
valve box or main piping. Install
horizontal run extending through
the wall of basin. Secure vertical
run to the vertical discharge
piping using the appropriate
method (i.e., flange, weld,
gasketed collar coupling) and
grout all piping extending through
basin walls.
System Description:
In a Hydromatic Pultruded Rail
System, the pump is raised and
lowered in the basin using a
noncorrosive fiberglass I-beam.
A unique, patented hydraulic
sealing flange at the pump
discharge allows the pump to
be connected and removed from
the discharge elbow with ease at
any time without entering the
wet well. There is no need to
disconnect any piping or electrical
connections to remove a pump for
inspection or routine maintenance
checks. A typical system will
operate on float control switches.
A bottom float control will turn
off the pump(s). An additional
float control per pump is then
used to turn on the pump(s). In a
multiple pump station, the pumps
are automatically alternated
if using a standard Hydromatic
panel. Also, additional float
controls may be used to
indicate height and/or low
water sump conditions. The
general
equipment
for
a
simplex and duplex system
includes the following:
Simplex
Duplex
One pump
Two pumps
One discharge
Two discharges
Elbow assembly
Elbow assemblies
One hydraulic
Two hydraulics
Sealing flange
Sealing flanges
One guide rail
Two guide rails
One lifting chain Two lifting chains
One door &
Two doors &
frame assembly
frame assemblies
Electrical
Electrical
controls
controls
Two level
Three level
controls
controls
Содержание PULTRUDED RAIL SYSTEM
Страница 11: ......