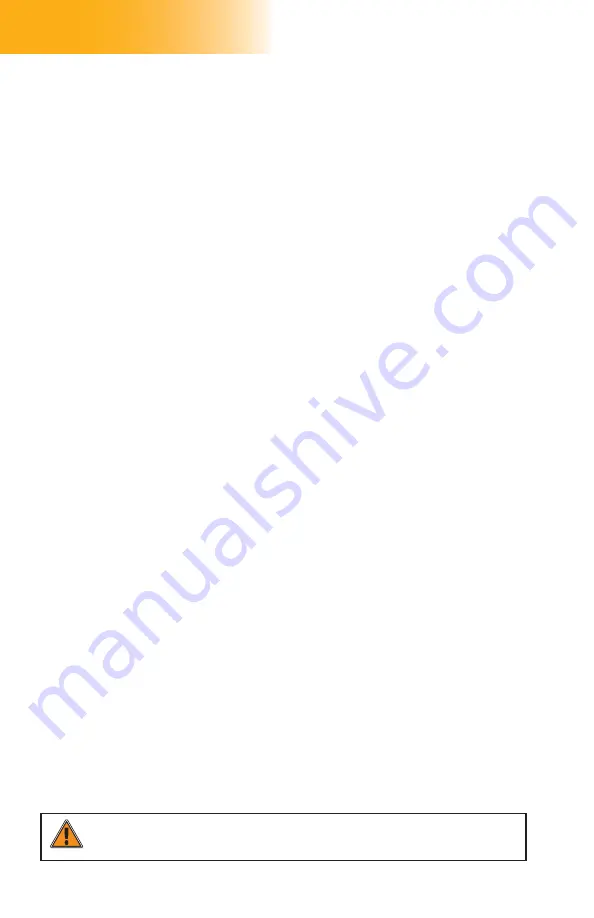
44
2 - S
ਠਥਤਲ਼ਸ
D
ਤਵਨਢਤਲ
Emergency Descent Control System
Emergency descent procedure for a single unit installation (cont’d)
Emergency descent procedure for a multiple units installation
Safety Devices
1-
Make sure that the engine is still running at the operating end of the structure (see “A”
in fi g. 2.6, p. 45).
Perform the following steps at the end of the structure that
cannot be operated normally
(see “B” in fi g. 2.6, p. 45).
2-
Make sure the engine is shut down at the end of the structure that cannot operate
normally. On an
F300 unit model used in a linked confi guration
, make sure that
both engines are shut down.
3-
Before using the emergency descent control system check the hydraulic oil level to
make sure it is in the
FULL
range on the dipstick. The emergency descent system
must
not be used if there is a major hydraulic leak
. On an
F300 unit model used in a
linked confi guration
, make sure to verify both sides of the unit.
4-
Perform a visual inspection of gears, pinions and rollers and other parts of the structure
to make sure that they are clear of debris and that there are no signs of damages that
could prevent the emergency descent system from operating normally. The emergency
descent system
must not be used if the gear system is damaged
. In case of doubt,
contact a qualifi ed technician to seek advice. For the defi nition of a qualifi ed technician,
refer to p. 7 of the
Performance and Safety Rules
section.
5-
Pull the emergency stop button to power on the control panel and log in. On an
F300
unit model used in a linked confi guration
, power on both control panels.
6-
Review all screen alerts and make sure that there is no high oil temperature alert
displayed. Make sure also that the overspeed safety device is not engaged. For more
information about the control panel and the alerts displayed, refer to the
Control Panel
section, on p. 74. On an
F300 unit model used in a linked confi guration
, perform
this step on both sides of the unit.
7-
If there is a high oil temperature alert on the screen or if high oil temperature is suspected,
let the oil cool down suffi ciently before initiating the emergency descent procedure.
WARNING
The emergency descent system must be inspected and tested when and as
required by the daily/weekly inspection schedule for this motorized unit.
7-
Once the oil level and temperature have been verifi ed and are appropriate, lift and
remove the plastic hood on the left-hand side of the control panel (fi g. 2.5, p. 43) to
access the control valve levers and the manual pump. On an
F300 unit model used
in a linked confi guration
, perform this step on
both sides of the mast
.
8-
Under normal operating conditions, all three control valve levers are in the
UP
position.
To activate the emergency descent system, pull all three levers down, beginning with
the bottom lever (see sequence illustrated in fi g. 2.2, p. 43). On an
F300 unit model
used in a linked confi guration
, perform this step on
both sides of the mast
.
9-
Once all three levers are down, close the manual pump relief valve by turning the knob
clockwise
(fi g. 2.3, p. 43). On an
F300 unit model used in a linked confi guration
,
perform this step on
both sides of the mast
.
10-
Build up hydraulic pressure by operating the pump handle back and forth
throughout
the emergency descent (fi g. 2.4, p. 43). On an
F300 unit model used in a linked
confi guration
, perform this step on
either side of the mast
. The motorized unit will
descend at a speed between 5' (1,5 m) and 10' (3 m) a minute.
11-
If the
emergency descent must be interrupted
, open the manual pump relief valve
by turning the knob
counterclockwise
or by lifting the upper control valve lever (“3”
in fi g. 2.2, p. 43) to release the hydraulic pressure. On an
F300 unit model used in
a linked confi guration
, perform this step on
either side of the mast
.
12-
To reactivate the emergency descent, make sure that all three levers are down and
that the valve is closed (according to what was done in step 11 above). On an
F300
unit model used in a linked confi guration
, perform this step on
the side where the
relief valve was opened
(see step 11).
13-
Once the motorized unit has been brought safely to the
nearest evacuation point
,
open the manual pump relief valve by turning the knob
counterclockwise
and raise
all three levers, starting from the top. Replace the plastic hood and secure in place.
The engine cannot be started if all or any of the levers of the control valves are down.
On an
F300 unit model used in a linked confi guration
, perform this step on
both
sides of the mast
.