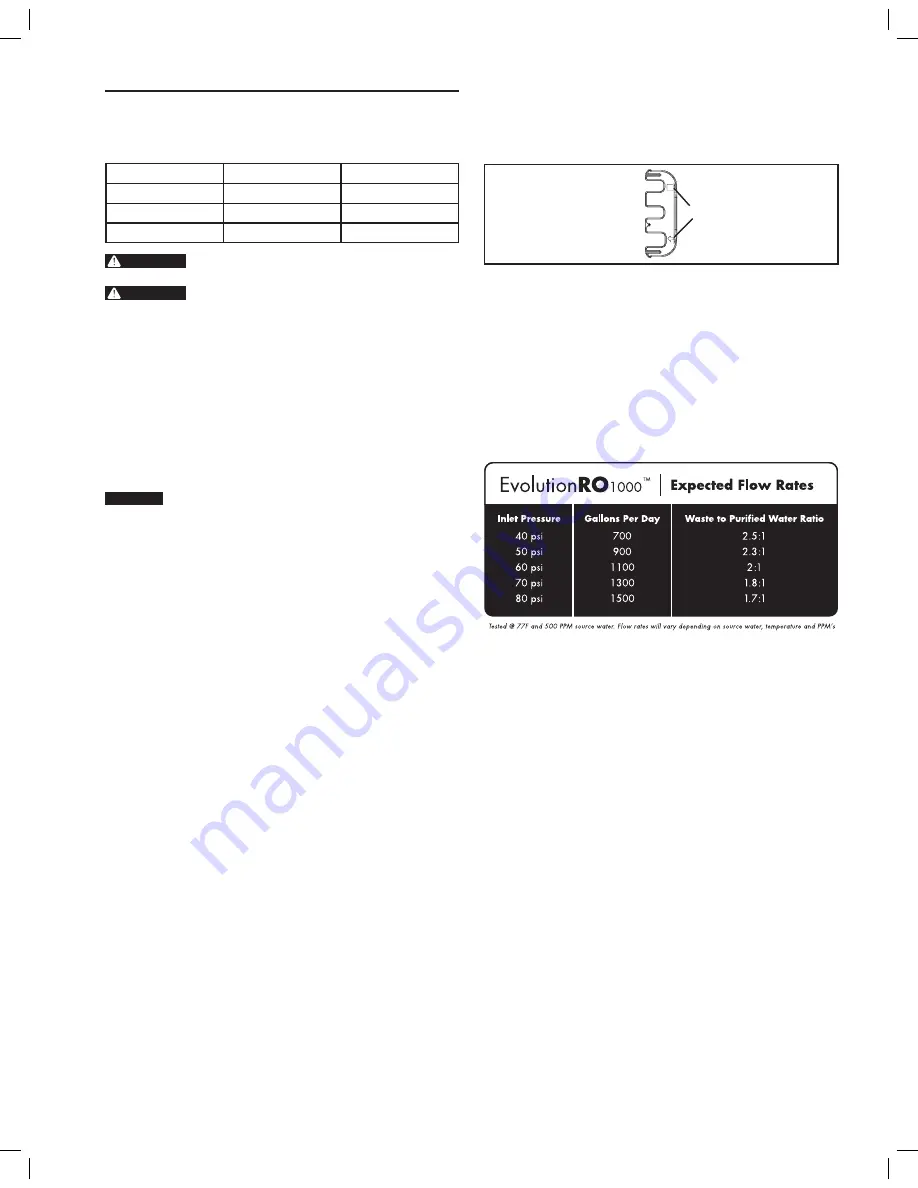
The table below shows the coding system for the fitting connections.
Each fitting has a unique “keyed” socket on the manifold. Each
fitting also has a graphic symbol molded into the elbow with a
corresponding symbol on the manifold.
Connector Symbol
Connection
Tubing Color
`
Feed-Inlet
Natural
—
Concentrate
Black
*
Product
Blue
WARNING:
Be sure to lubricate the manifold ports with silicone
lubricant, prior to inserting the fittings into manifold.
WARNING:
Do not turn the incoming water valve on until the
locking bar is in place.
When all of the connections have been made, use the locking bar to
hold the fittings in position. Match the symbols on the locking bar to
the corresponding symbols on the manifold (Figure 12).
Step 6: System Startup
Inspect all connections.
1.
Position manifold horizontal with openings facing up.
2.
Remove new membrane elements from plastic packaging. The
3.
blue and green tape surrounding the membrane are an important
part of the membrane element and should not be removed.
CAUTION:
Elements contain a foodgrade preservative. The use of
sterile/latex gloves is recommended.
Lubricate all O-ring seats in the manifold that come in contact
4.
with the sump and element O-rings. Refer to "Connection
Lubrication" on page 8.
NOTE: To properly lubricate the O-ring contact area, a film of clean
silicone grease is applied. The film should cover all of the
surface area that the O-ring will slide over and seal with. Do
not use grease containing petroleum products.
Securely insert O-ring end of membrane elements into manifold.
5.
Push the membrane straight down into the hole in the manifold.
Do not twist or rock the membrane when intsalling, as this may
damage the o-rings.
Remove pre-filter from packaging. Check that gaskets are in
6.
place.
Place pre-filter in manifold.
7.
Replace sumps and tighten until it bottoms out. (DO NOT
8.
OVERTIGHTEN)
Pressure Test System
To check for leaks, the system must be filled with water and brought
up to operating pressure.
Open cold water feed valve slowly. Run at 1/2 open for a minute,
1.
then open fully.
Make sure included shut off valve installed on the blue purified
2.
water line is in the open position.
Check for leaks.
3.
NOTE: When the system is initially turned on, water may temporarily
sputter all the air is purged. Allow 1 to 3 hours for any trapped
air noise in the system to subside.
Purge the system. Run the water through the RO system allowing
4.
all water to go to drain for two to eight hours to stabilize the pH
and PPM’s of the purified water
NOTE: A minimum of a 2 hour flush is required to remove the food
grade preservative. After 8 hours performance will reach its
stable maximum performance.
The RO system is now ready for use.
Symbols
INSTALLATION cont.
Figure 6
NOTE: The flow ratre of purified water will vary depending on 3
factors:
- Inlet water pressure
- Inlet water temperature
- Inlet water PPM
9
Содержание EVOLUTION-RO1000
Страница 1: ...Installation Maintenance Manual ...
Страница 16: ...GL4000442 RevA ...