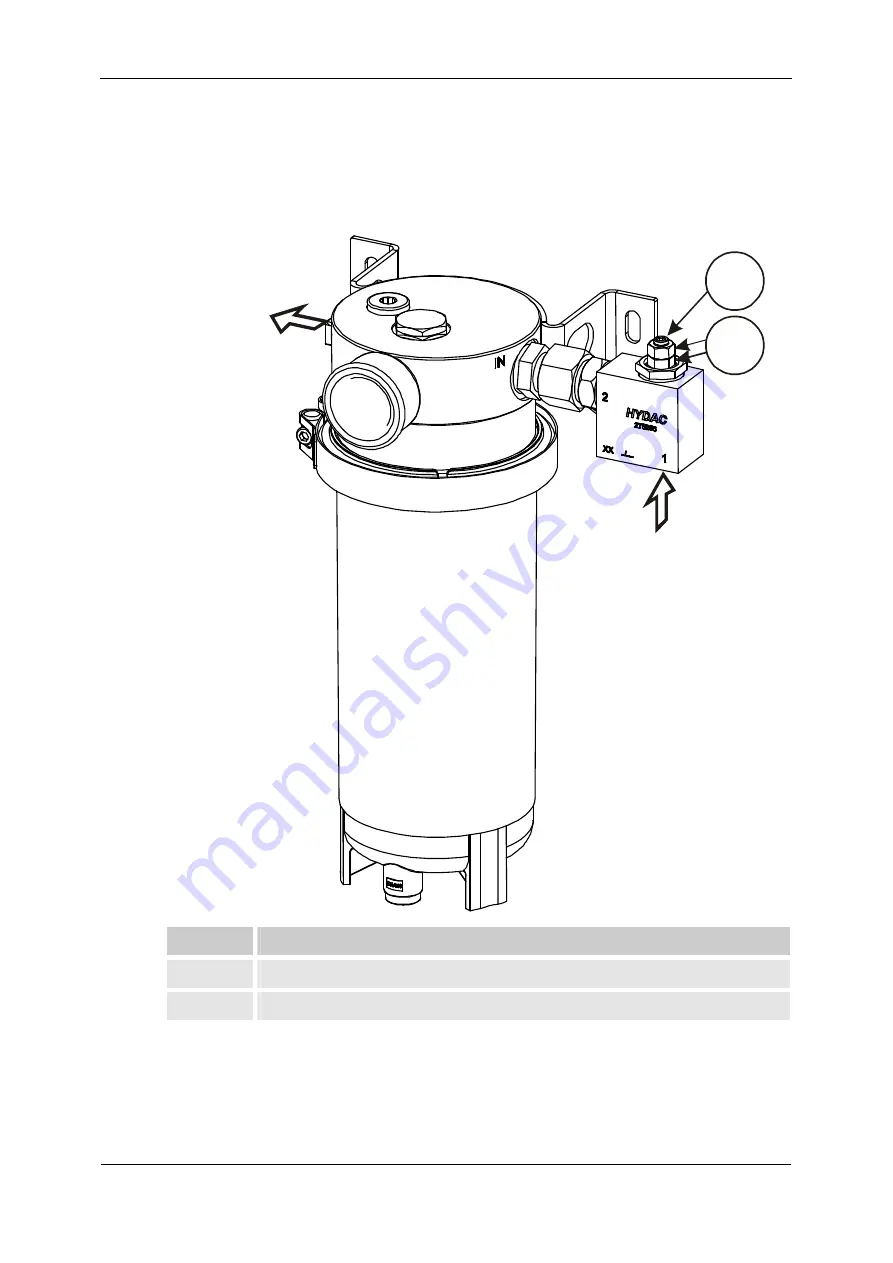
OLF-5 Series
Starting up the OLF
HYDAC FILTER SYSTEMS GMBH
en
Page 19 / 52
BeWa OLF5_Serie 3433222b en-us 2011-11-14.doc
2011-11-14
OLF with flow control valve (only OLF -5-E-Z)
The flow control valve keeps the exiting flow constant due to a controlling process.
The flow rate is almost entirely independent of the pressure and viscosity.
The flow rate is factory-set to 5 l/min. The flow control valve's setting range ranges
from 4.0 ... 5.2 l/min.
A
B
IN
OUT
Item
Description
(A)
Adjustment screw
(
B)
lock nut