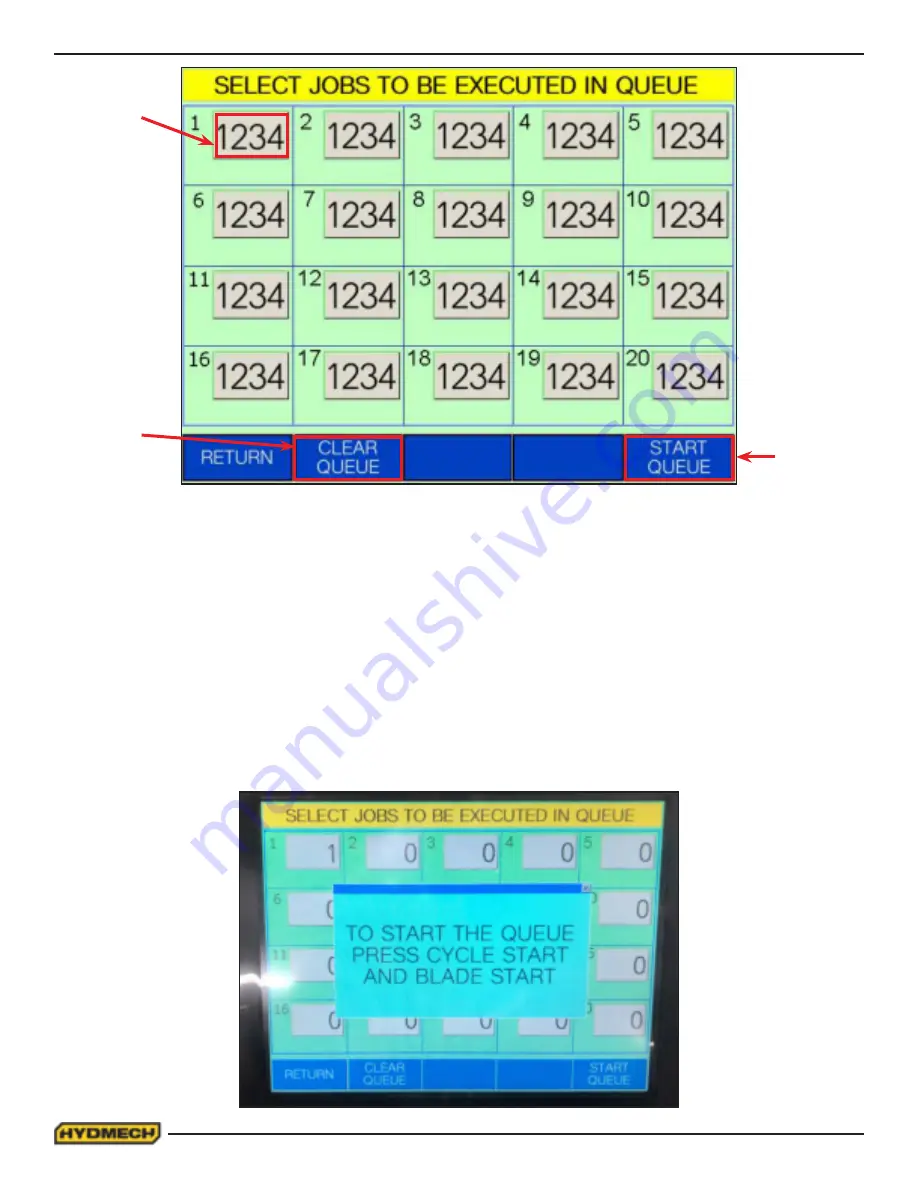
2.12
STEP 7
STEP 8
STEP 9
Step 7. To ensure that no jobs from the previous queue have been programmed into this queue. It is recommended
that the previous job queue be cleared before programming the new job queue. This is done by selecting the “CLEAR
QUEUE” key on the touch screen. All job numbers currently inputted in the queue will disappear and the 20 grey input
fields in the job queue should be set to their default setting of “0” meaning no job has been inputted.
Step 8. Select grey input box on the 1st queue block on the interface, a number pad display window will appear over the
job queue window. Key in the desired Job # from 1 to 1000 on the touch screen and press enter. The number pad display
window will disappear and the desired job # will be displayed in the selected queue block on the job queue window. The
purpose of a QUEUE is to allow the operator to run several jobs (maximum of 20) in series if they are of the same mate-
rial and shape. Order of the queue is determined by the number in each queue block. With the job programmed in queue
block 1 being run first and the job programmed in queue block 20 being run last.
Step 9. After all jobs have been entered, select the “START QUEUE” key on the interface. The job queue window will dis
-
appear and a display window will prompt to initiate the job queue by pressing cycle start on the keypad. Press the “Cycle
Start” button on the keypad to initiate the job queue.
Содержание V18APC
Страница 2: ...2 ...
Страница 64: ...5 3 HYDRAULIC SCHEMATIC AND PLUMBING DIAGRAM SEE PDF ON ATTACHED CD ...
Страница 65: ...6 1 MECHANICAL ASSEMBLY DRAWINGS PARTS LIST SEE PDF ON ATTACHED CD SECTION 6 MECHANICAL ASSEMBLIES ...
Страница 66: ...7 1 SECTION 7 OPTIONS OPTIONAL ASSEMBLY DRAWINGS SEE PDF ON ATTACHED CD ...
Страница 73: ......