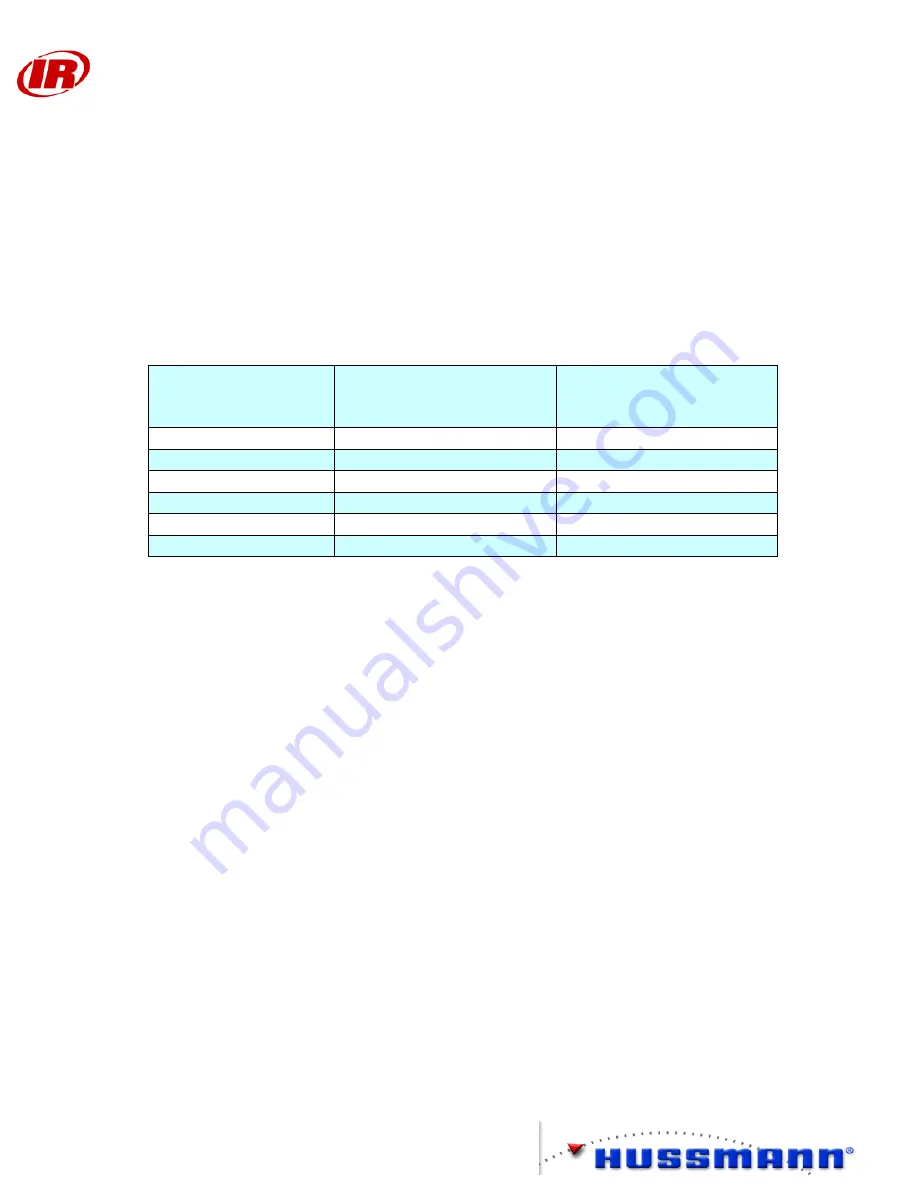
Protocol™ Installation and
Service Manual
Air Vent Valves
Manual air vent valves are recommended. Air vent valves should be located at piping high
points where air will tend to collect. Momentarily open these vents and release trapped air
a few times during startup.
Tie-Ins to Supply Headers
Branch supply pipes
SHOULD NOT
tie into the bottom of main supply pipes. Always tie
into top of a main supply pipe; that is, the “T” fitting should point
UP, NOT DOWN.
Pipe Supports
Pipe support should be provided as follows:
Nominal Pipe Size,
inches
Distance Between Supports,
feet
Schedule 40 Pipe @ 100 °F
Distance Between Supports,
feet
Schedule 80 Pipe @ 120 °F
1.0 4.5
3.5
1.5
5.0
3.5
2.0 5.0
4.0
3.0
6.0
4.5
4.0 6.5
5.0
6.0
7.5
6.0
Do not clamp supports tightly – this restricts axial movement of the pipe. Supports should
provide a smooth bearing surface that conforms to the bottom of the pipe, and should be a
minimum of 2 inches wide.
Exposure to Direct Sunlight
Piping that will be exposed to direct sunlight should be shaded or covered. A thin layer of
insulation is adequate for this.
Leak Check
Check for leaks in the piping before startup by filling with pressurized water at 50 psig.
Cleaning and Flushing
The pipe loop should be cleaned before the system is put into service. Fill the closed loop
with a solution of 1% trisodium phosphate and (99%) water, by weight.
Circulate the detergent/water solution for 24 hours.
Drain the loop and refill with fresh water. Circulate for at least 3 hours.
Drain and refill again. Repeat until all phosphate is gone.
Filling
The water loop
MUST
have adequate corrosion protection. In most situations, using fully
inhibited, industrial grade ethylene glycol or propylene glycol 30% by volume with water
50
Содержание Proto-Aire
Страница 1: ...9 20 2005 Installation Manual Hussmann Part 0385841 ...
Страница 11: ...Protocol Installation and Service Manual TYPICAL PIPING ELECTRICAL HOOKUP Vertical Units 7 ...
Страница 12: ...Protocol Installation and Service Manual 8 ...
Страница 13: ...Protocol Installation and Service Manual 9 ...
Страница 14: ...Protocol Installation and Service Manual 10 ...
Страница 15: ...Protocol Installation and Service Manual 11 ...
Страница 16: ...Protocol Installation and Service Manual 12 ...
Страница 17: ...Protocol Installation and Service Manual 13 ...
Страница 18: ...Protocol Installation and Service Manual 14 ...
Страница 19: ...Protocol Installation and Service Manual 15 ...
Страница 20: ...Protocol Installation and Service Manual 16 ...
Страница 21: ...Protocol Installation and Service Manual 17 ...
Страница 22: ...Protocol Installation and Service Manual 18 ...
Страница 23: ...Protocol Installation and Service Manual 19 ...
Страница 24: ...Protocol Installation and Service Manual Horizontal Units 20 ...
Страница 25: ...Protocol Installation and Service Manual 21 ...
Страница 26: ...Protocol Installation and Service Manual 22 ...
Страница 27: ...Protocol Installation and Service Manual 23 ...
Страница 28: ...Protocol Installation and Service Manual 24 ...
Страница 29: ...Protocol Installation and Service Manual 25 ...
Страница 30: ...Protocol Installation and Service Manual 26 ...
Страница 31: ...Protocol Installation and Service Manual 27 ...
Страница 32: ...Protocol Installation and Service Manual 28 ...
Страница 33: ...Protocol Installation and Service Manual 29 ...
Страница 34: ...Protocol Installation and Service Manual 30 ...
Страница 35: ...Protocol Installation and Service Manual 31 ...
Страница 36: ...Protocol Installation and Service Manual 32 ...
Страница 37: ...Protocol Installation and Service Manual Proto_Aire Units 33 ...
Страница 38: ...Protocol Installation and Service Manual 34 ...
Страница 39: ...Protocol Installation and Service Manual 35 ...
Страница 40: ...Protocol Installation and Service Manual 36 ...
Страница 41: ...Protocol Installation and Service Manual 37 ...
Страница 42: ...Protocol Installation and Service Manual 38 ...
Страница 43: ...Protocol Installation and Service Manual 39 ...
Страница 58: ...Protocol Installation and Service Manual Very Large Box Very Large Box Pump Station Water Cooled Condenser 54 ...
Страница 62: ...Protocol Installation and Service Manual 58 ...
Страница 68: ...Protocol Installation and Service Manual Electrical Legend 64 ...
Страница 69: ...Protocol Installation and Service Manual Main Power Wiring 208V Two Wide Protocol 65 ...
Страница 70: ...Protocol Installation and Service Manual 208V 5 or 6 Compressor Protocol 66 ...
Страница 71: ...Protocol Installation and Service Manual 460V Two Wide Protocol 67 ...
Страница 72: ...Protocol Installation and Service Manual 460V 5 or 6 Compressor Protocol 68 ...
Страница 73: ...Protocol Installation and Service Manual 460V Two Wide Protocol with Factory installed transformer 69 ...
Страница 74: ...Protocol Installation and Service Manual 460V Two Wide Protocol with Field supplied transformer 70 ...
Страница 75: ...Protocol Installation and Service Manual 460V 5 or 6 Compressor Protocol with Field supplied transformer 71 ...
Страница 76: ...Protocol Installation and Service Manual 600V Two Wide Protocol 72 ...
Страница 77: ...Protocol Installation and Service Manual 600V 5 or 6 Compressor Protocol 73 ...
Страница 78: ...Protocol Installation and Service Manual 600V Two Wide Protocol with Field supplied transformer 74 ...
Страница 81: ...Protocol Installation and Service Manual Control and Compressor Wiring PCS without Vapor Wiring 77 ...
Страница 82: ...Protocol Installation and Service Manual PCS with Vapor Wiring 78 ...
Страница 83: ...Protocol Installation and Service Manual CPC Danfoss Comtrol without Vapor Wiring 79 ...
Страница 84: ...Protocol Installation and Service Manual CPC Danfoss Comtrol with Vapor Wiring 80 ...
Страница 85: ...Protocol Installation and Service Manual Controller Wiring PCS 81 ...
Страница 86: ...Protocol Installation and Service Manual CPC 82 ...
Страница 87: ...Protocol Installation and Service Manual CPC Einstein 83 ...
Страница 88: ...Protocol Installation and Service Manual Danfoss 84 ...
Страница 89: ...Protocol Installation and Service Manual Comtrol 85 ...
Страница 99: ...Protocol Installation and Service Manual 95 ...
Страница 100: ...Protocol Installation and Service Manual 96 ...
Страница 101: ...Protocol Installation and Service Manual POWERLINK Operation 97 ...