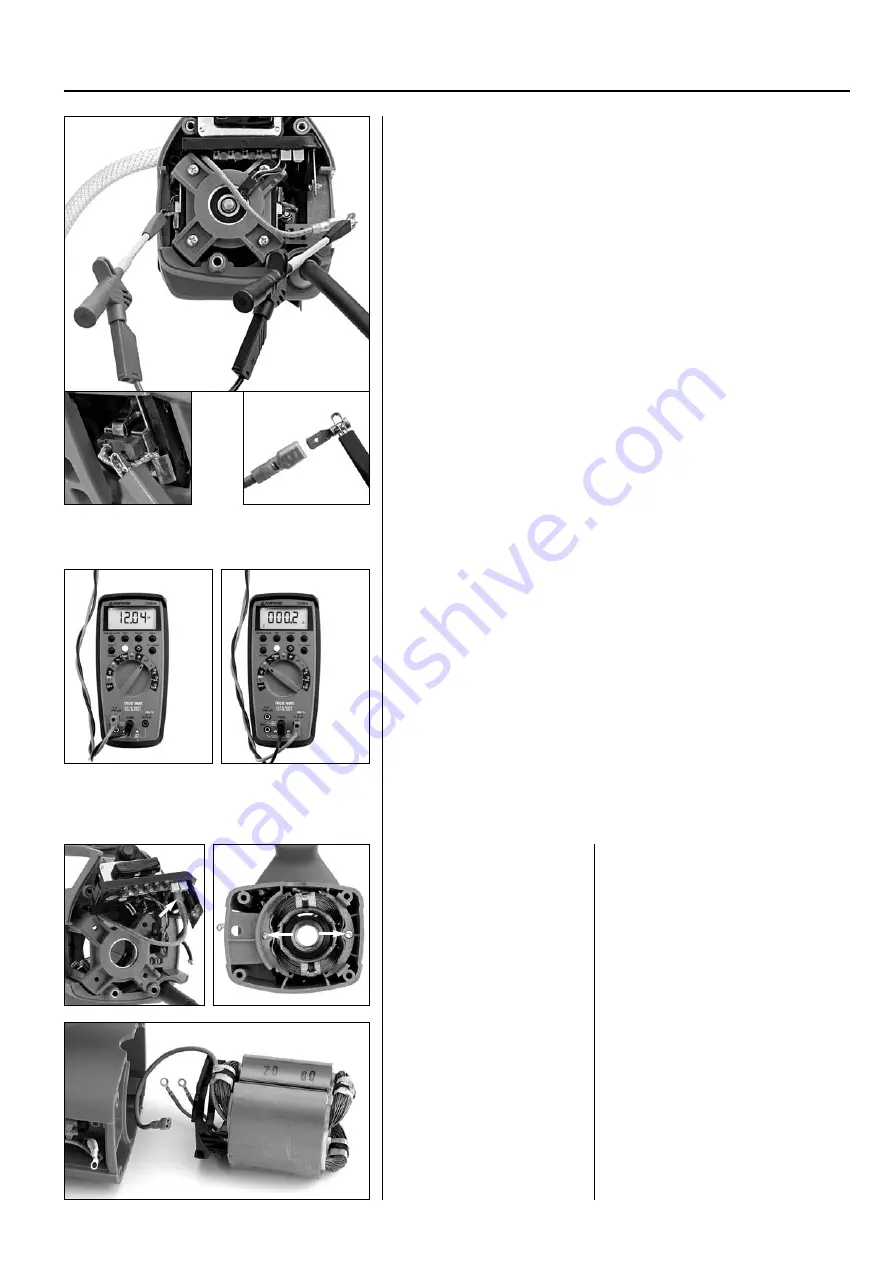
STATOR – 120 V
Dismantling
Loosen the contact.
Remove both stator screws.
Dismantling
Loosen the flat pin contact from the
circuit board.
Remove the two screws that hold the
stator in the motor housing. Nuts on the
opposite side of the stator.
Pull the stator out of the motor housing
by hand.
Note when reassembling: The flat pin
contact is connected to the circuit board.
Connect the two round cable lugs (d) to
the same carbon brush holder (left side
seen from behind). See page 17.
Pull the stator out of the motor
housing.
Functional test
Fractures to the stator winding are easiest to indicate using the check below.
In general, short-circuited windings can also be identified, particularly if the
short circuit eliminates current in several winding turns. If the short circuit
only eliminates a few turns, the measurement is unlikely to record this. A
fault like this has no noticeable effect on the performance of the motor either.
Resistance measurement – Ohm Ω
Resistance measurement provides an unequivocal answer as to whether the
stator winding is fractured. However, the method gives unclear indications for
short-circuited winding turns.
Inductance measurement – Henry (H)
The dimension is “Henry”, abbreviated H (1 H = 1000 mH). Inductance
measurement is best applied to both identify fractures in the stator winding or
short-circuited winding turns.
Use short measuring cables and lay these close to each other: the easiest way
is to twist them. Cables run in a coiled way give incorrect readings.
Preparations, illustration 1
Remove the inspection cover to the carbon brushes.
Left side: Break the electric circuit to the rotor by pulling out the carbon
brush a little and lock with the spring to the side. Connect one of the test
pins to the carbon brush.
Disconnect the contact to the stator at the circuit board and connect to the
other test pin.
Measured values
Typical measured values for a complete stator are around 10–12 mH. Typical
value for resistance measurement is around 0.2–0.3 ohm.
If the stator winding is fractured you get the value 0 mH. Resistance
measurement gives a maximum, or immeasurable ohm figure.
Short-circuited winding turns reduce the inductance value. If the value is
30 % below the typical value, the stator is unfit for use.
A dismantled stator is best tested by measuring both stator windings indivi -
dually. Connect the measurement cables to the flat pin sleeve and one of the
ring cable lugs. Repeat the measurement with the other ring cable lug.
Typical values for a winding (one of two) are for an inductance measure-
ment 4–4.5 mH and for a resistance measurement 0.5–0.6 ohm. Major
deviations between the windings indicate a defect stator.
mH
Ω
1
15
21
d