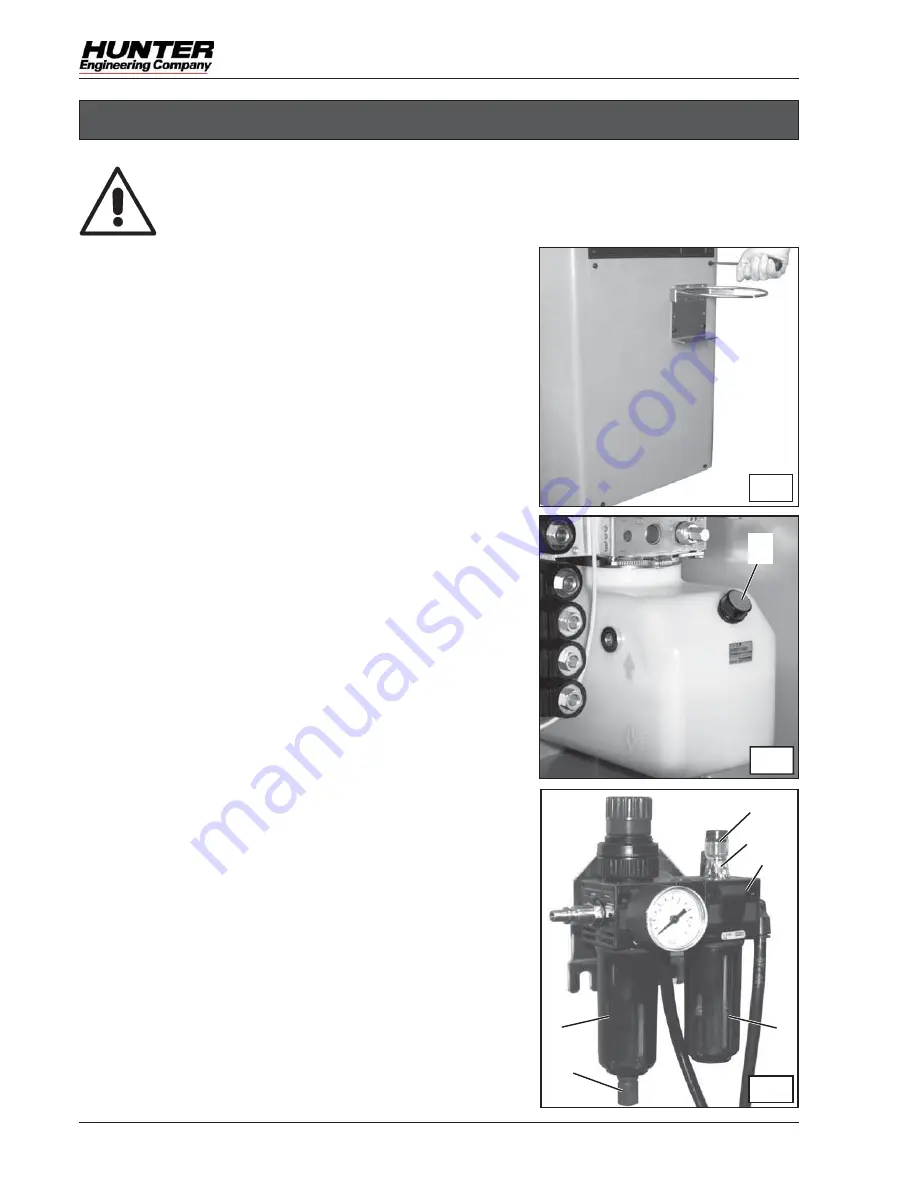
58
(1*/,6+,QVWUXFWLRQVPDQXDO
7&;
12. MAINTENANCE
WARNING!
Before carrying out any maintenance, the tyre changer must be disconnected from the power supply sources:
1) Disconnect the equipment from the electrical mains.
2) Disconnect the equipment from the compressed air supply system by disconnecting the intake line using --------
the snap union fitted.
To obtain the best performance and a longer working life from your TCX3000 tyre
changer, carry out the maintenance procedures listed below:
1- CHECK the hydraulic power unit oil level periodically.
The tank is in clear plastic and is installed inside the control column.
Proceed as follows:
- Unscrew the 4 screws which secure the guard (see Fig. R/1).
- Check that the oil level in the tank is between the MINIMUM and MAXIMUM arrows
(see Fig. R/2).
For any top-ups:
- Unscrew the cap on the tank (1, Fig. R/2).
- Top up with Esso Nuto H 46 hydraulic system oil or equivalents (e.g. AGIP OSO 46,
SHELL TELLUS OIL 46, MOBIL DTE 25, CASTROL HYSPIN AWS 46, CHEVRON RPM EP
HYDRAULIC OIL 46, BP ENERGOL HLP.)
- Screw the cap back onto the tank and replace the guard.
2- CHECK regularly (about once a fortnight) that the lubricator oil level is between
the “MIN” and “MAX” marks on the cup (5, Fig. R/3).
To top up, proceed as follows:
- Unscrew the cup (5, Fig. R/3).
- Top up with class ISO HG pneumatic system oil having viscosity ISO VG 32 (for
example: ESSO Febis K 32; MOBIL Vacouline Oil 1405; KLUBER Airpress 32).
- Screw the cup back into place.
3- Make a regular CHECK (every 2-3 days) that the lubricator unit is functioning
correctly (4, Fig. R/3).
Operate the control of the fixed bead presser, checking that at every 5-6 arm travel
strokes, a drop of oil falls into the clear cup (6, Fig. R/3) of the lubricator.
Otherwise, adjust the lubricator regulator screw (3, Fig. R/3) with a screwdriver.
4- To ensure that the safety device which limits the pressure during tyre inflation
(see “Safety Devices” section) continues to operate efficiently over time, it is essential
to perform the checks listed below:
- Check the condensation level in the filter cup (1, Fig. R/3) regularly; it must NEVER
be above the “MAX. DRAIN” mark on the cup.
When necessary, drain the condensation by turning the ring-nut (2, Fig. R/3)
clockwise
N.B.: connect to the compressed air supply system to carry out this operation.
-Every 30 - 40 days disconnect the machine from the compressed air supply and
remove the cup (1, Fig. R/3) to clean out any solid dirt which has built up inside it.
5- CLEAN the machine every day, removing any dirt or tyre waste which might
block the tool carriage travel ways, or chuck clamping device.
6- CLEAN the lens of the laser pointer and the mirror (or camera, if installed)
regularly.
7
- CHECK the condition of the plastic guards on the mounting and demounting tools
every day.
If they are worn or damaged, REPLACE them with new ones.
R/1
R/3
1
2
3
4
5
6
R/2
1
Содержание TCX3000
Страница 32: ...32 7 12 0DQXDOH G XVR 7 ...
Страница 62: ...62 1 6 QVWUXFWLRQV PDQXDO 7 ...
Страница 92: ...92 5 1d 6 0DQXHO G LQVWUXFWLRQV 7 ...
Страница 122: ...122 876 HWULHEVDQOHLWXQJ 7 ...