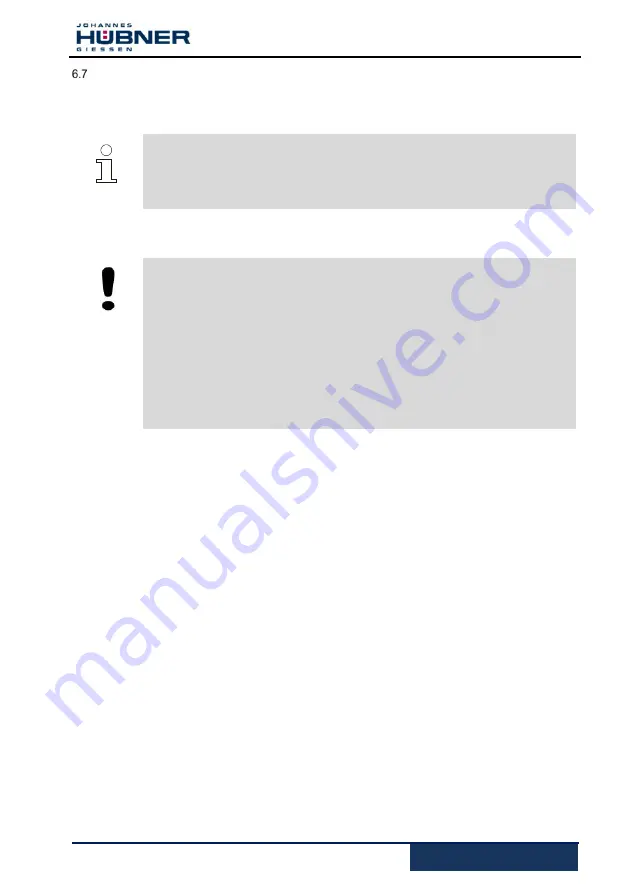
Incremental Encoder FG 41
37
Connection instructions for plug connection
The electrical equipment features are mainly determined by the variable connection
technology.
NOTES!
The connection can only be made in conjunction with the device-specific pin
assignment!
When the measuring system is delivered, a printed version of the pin assignment is
enclosed and can also be downloaded later.
7
Incremental interface
CAUTION!
Danger of damage to subsequent electronics due to overvoltages caused by a
missing ground reference point!
·
If the ground reference point is completely missing, e.g. 0 V of the power
supply not connected, voltages equal to the supply voltage can occur at the
outputs of this interface.
- It must be ensured that a ground reference point is present at all times,
- or the system operator must provide appropriate protective mechanisms
for the subsequent electronics.
●
If the input voltage exceeds 30 V, these voltages occur accordingly at the
HTL outputs. This can lead to damage of the output or input circuit of the
downstream processing unit.
The measuring system acquires the angular information from the connected process via the
rotation of the shaft. A pulse disk is fixed to the shaft; this acquires the angular increments with
a defined number of periods per revolution. A scanning unit with integrated optoelectronics
generates electrical signals and outputs signal periods, which can be processed in a signal
conditioner afterwards.
The resolution of the measuring system is defined by the number of light/dark segments (pulse
number per revolution) on the pulse disk. A signal sequence of e.g. 1024 periods is output
during one revolution. To evaluate the counting direction, a 2nd signal sequence with a 90°
phase offset is output for the control.
The counter of an external control can be reset with an additional zero pulse, and the
mechanics - control reference point can thus be defined.