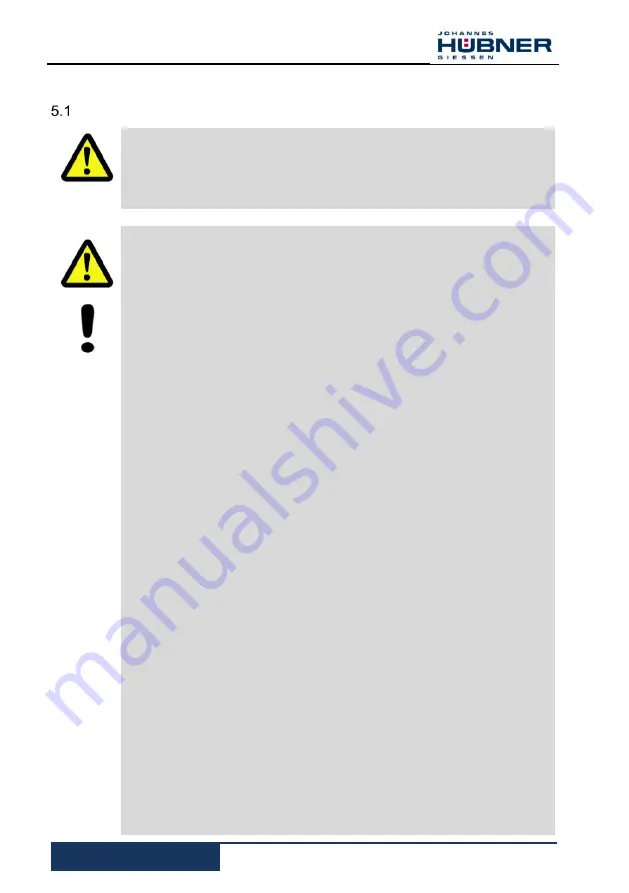
24
Incremental Encoder FG 41
5 Assembly
Safety instructions
WARNING!
At assembly, dismantling and other work to the device the basic safety
instructions to chapter 2 must be observed.
The assembly, dismantling and other work of the measuring system must only
be carried out by qualified personnel!
DANGER! NOTICE!
Danger of death, serious physical injury and/or damage to property due to
deactivation of safety functions, caused by an unstable shaft drive!
·
The system manufacturer must implement suitable design measures, so that
the drive of the measuring system is ensured at all times through the shaft
and mounting of the measuring system (fault exclusion). The specifications
of
DIN EN 61800-5-2:2017-11
Adjustable speed electrical power drive systems,
Safety requirements, Table D.8 – Motion and position sensors" must be
observed.
·
In general, the requirements and acceptance conditions for the complete
system must be taken into account for mounting.
·
The measuring system must be inspected on a regular basis (see below).
Inspections must be recorded in a log book.
As the installation situation is application-dependent, the following notes
are not exhaustive.
·
All fastening screws must be secured against unintentional loosening.
All screwed connections must be inspected once a year.
·
In case of applications with low operating temperatures, increased values for
the start-up torque result. This fact is to be considered when the assembling
and shaft drive is performed.
·
After approx. 16 000 - 20 000 hours of operation or higher levels of
continuous load:
Check deep groove ball bearings for noise, running smoothly. Bearings must
be replaced by the manufacturer only.
·
A suitable coupling with form closure must be used for the application. The
coupling must be dimensioned so that fault exclusion is ensured for the
mechanical mounting of the measuring system in accordance with DIN EN
61800-5-2, depending on the static and dynamic load cases. If this is not
possible, the hazard must be incorporated into the risk assessment for the
application in the form of a coupling breakage.
·
The coupling manufacturer's information and installation requirements must
be observed.
In particular, you must ensure that:
·
the coupling is suitable for the specified speed and the potential axial offset,
·
installation is on a grease-free shaft,
·
the coupling and the measuring system are not axially loaded,
·
the clamping screws are tightened with the torque defined by the coupling
manufacturer,
·
the screws are secured against unintentional loosening
·
Axial slipping of the measuring system on the drive shaft must be prevented
by the coupling fixing, see Figure 1