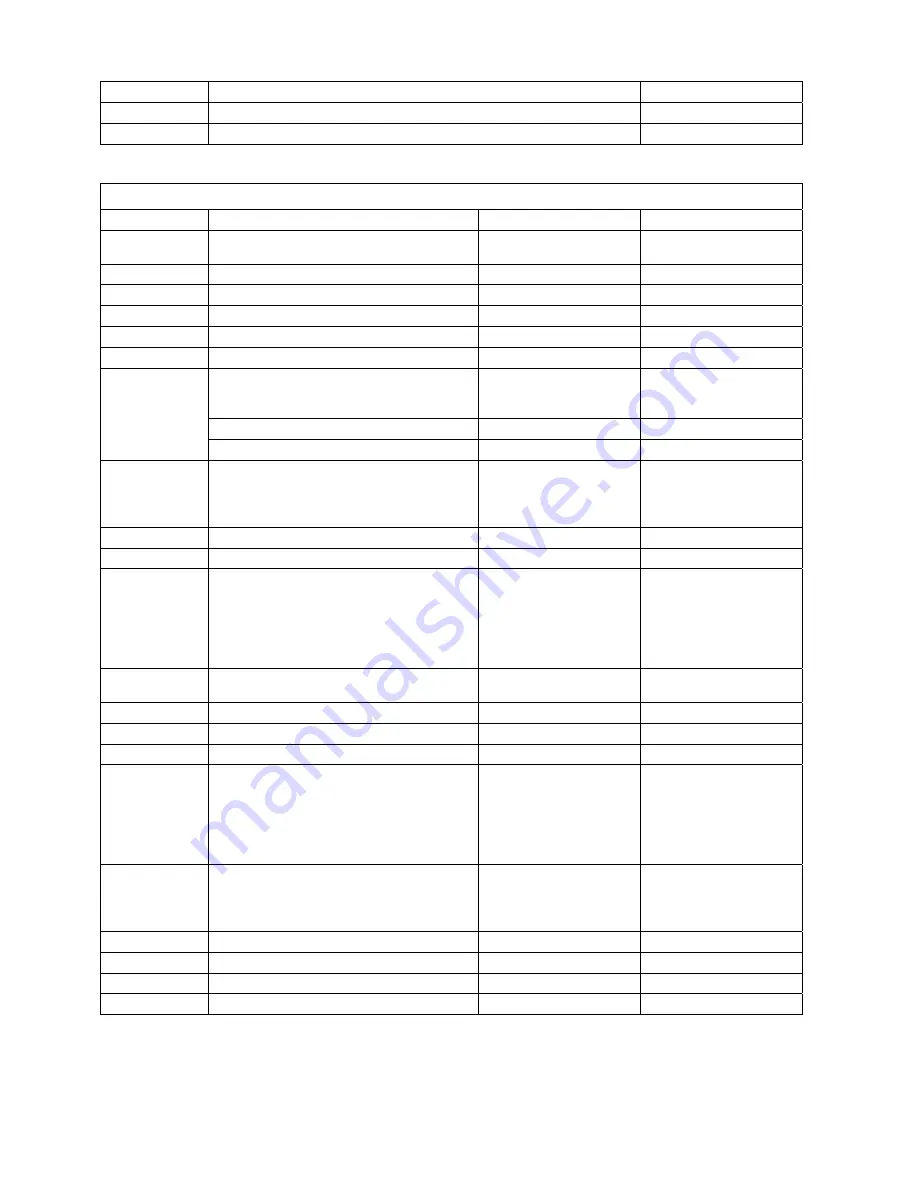
1
Top
Casting
F5A4
2
Bottom
Casting
F5B10
3
Evaporator
F5C13
Replacement Parts
Item
No.
Description
Includes
Part
No.
4
Coupling
Hub
Kit
Coupling
Hub
Hardware
F5A6
‐
KT
5
Main
Shaft
F5D2
6
Ice
Blade
F5E1
Ice
Blade
Adjustment
Gauge
Kit
Set
of
7
Gauges
E10E15
7
Auxiliary
Ice
Scraper
F5E2
8
Ice
Deflector
F5G1
9
Water
Distribution
Pan
Kit
Lead
Spout
Side
Spouts
Water
Distribution
Pan
F5H5
Water
Distribution
Pan
Side
Spout
F5H6
Water
Distribution
Pan
Lead
Spout
F5H30
10
Water
Tube
Kit
Compression
Fitting
Copper
Water
Tube
Insulation
Water
Regulating
Valve
F5H11
‐
KT
11
Water
Sump
Gasket
F5H18
12
Water
Sump
Cover
F5H25
‐
4
13
Water
Sump
Kit
Float
Valve
Water
Pump
Water
Regulating
Valve
Water
Sump
Gasket
Water
Sump
Water
Sump
Covers
F5H26
‐
P
14
Water
Distribution
Spout
Kit
Lead
Spout
Side
Spouts
F5H30
‐
KT
15
Handhole
Cover
F5I2
16
Top
Insulating
Ring
F5J4
17
Bottom
Insulating
Ring
F5J8
18
Bearing
Kit
Oil
Seals
Sleeve
Bearings
Bearing
Thrust
Plate
Bottom
Bearing
Disc
Lock
Ring
O
‐
Ring
F5K7
19
Gear
Motor
Kit
Adapter
Plate
Gear
Motor
Flexible
Coupling
Hardware
F5M1
‐
KT
20
Flex
Coupling
F5N1
21
Float
Valve
E10H79
23
Water
Regulating
Valve
E10H59
24
Water
Pump
E10Q7
‐
P
Содержание 1000-RLE
Страница 6: ...6 Engineering Guidelines Figure 1 ...
Страница 40: ...40 Appendix Appendix Cut View 1000 RLE ...
Страница 41: ...Appendix 41 Cut View 2000 RLE 3000 RLE ...
Страница 42: ...42 Appendix Assembly Drawing 1000 RLE Ice Flaker CP750 Mobile Express Ice Bin ...
Страница 43: ...Appendix 43 Assembly Drawing 2000 RLE Ice Flaker CP1500 Mobile Express Ice Bin ...
Страница 44: ...44 Appendix Assembly Drawing 3000 RLE Ice Flaker CP2500 Mobile Express Ice Bin ...
Страница 45: ...Appendix 45 Wiring Diagram Ice Flaker ...
Страница 46: ...46 Appendix Wiring Diagram 230 3 60 Air Cooled Condensing Unit supplied by Howe Corporation ...
Страница 47: ...Installation Service Manual For Use with Remote Single Condensing Unit RLE Rev Date 08 2014 ...
Страница 48: ...Parts List 1000 RLE Non Replaceable Parts Item No Description Part No ...
Страница 51: ...Parts List 2000 RLE 3000 RLE ...