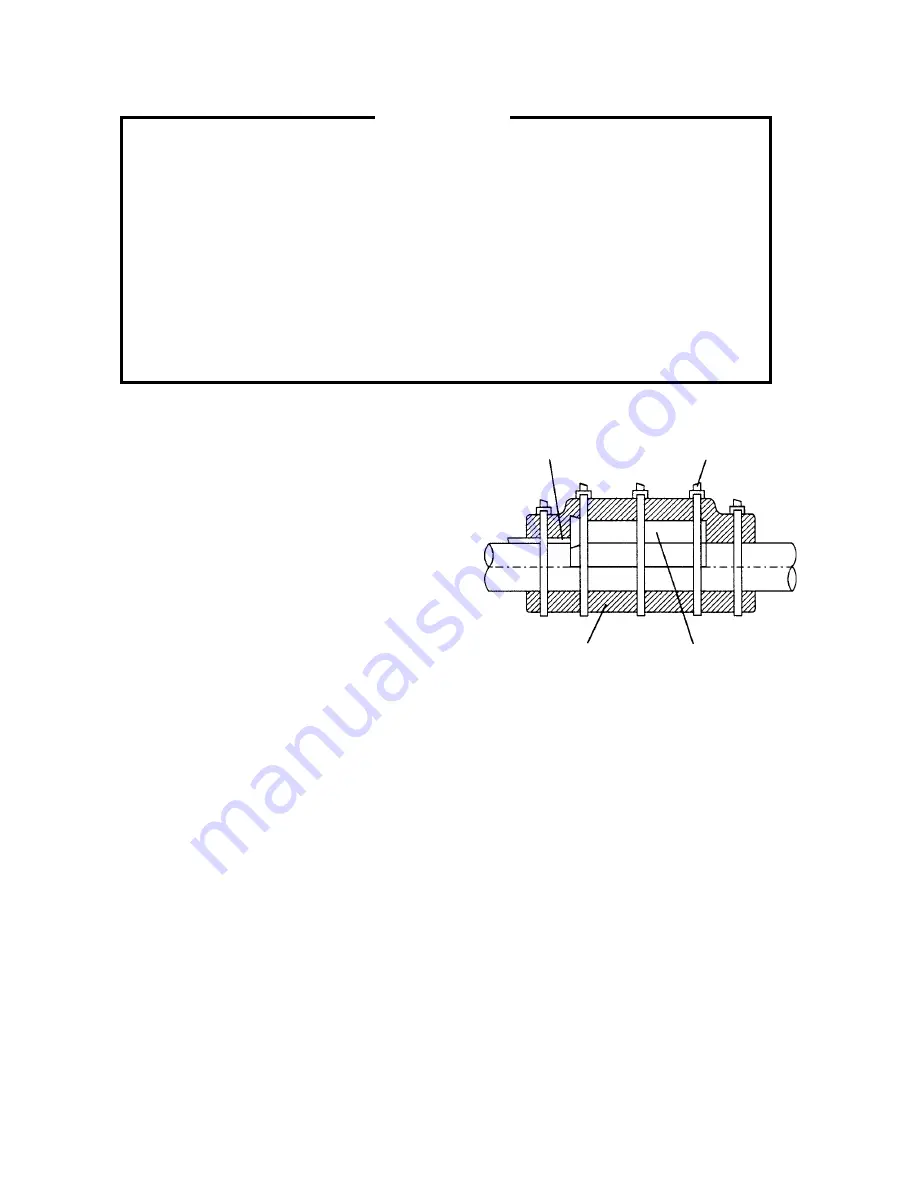
46
Foam Insulation
Thermistor Holder
Thermistor Lead
Cable Tie
Fig. 2
10. REMOVAL AND REPLACEMENT OF THERMISTOR
CAUTION
1. Fragile, handle very carefully.
2. Always use a recommended sealant (High Thermal Conductive Type),
Model KE4560RTV manufactured by SHINETSU SILICONE, Part Code
60Y000-11, or Part Code 4A0683-01 or equivalent.
3. Always use a recommended foam insulation (Non-absorbent Type) or
equivalent.
4. Do not shorten or cut the Thermistor leads when installing it.
1) Turn off the power supply, and unplug
the icemaker.
2) Remove the panels.
3) Remove the Control Box Cover
at the rear of the unit.
4) Disconnect the Thermistor leads from
the K3 Connector on the Controller
Board.
5) Remove the Plastic Cable Ties, Foam
Insulation, Thermistor Holder and
Thermistor. See Fig. 2.
6) Scrape away the old sealant on the Thermistor
Holder and the Suction Pipe.
7) Wipe off moisture or condensation on the Suction Pipe.
8) Smoothly apply recommended sealant (KE4560RTV, Part Code 60Y000-11) to the
Thermistor Holder concave.
9) Attach the new Thermistor to the Suction Pipe very carefully to prevent damage to
the leads. Secure it using the Thermistor Holder and recommended foam
insulation.
10) Secure the insulation using the Plastic Cable Ties.
Содержание KM-150BAF
Страница 5: ...5 I SPECIFICATIONS 1 KM 150BAF ...
Страница 6: ...6 2 KM 150BWF ...
Страница 7: ...7 II GENERAL INFORMATION 1 CONSTRUCTION a KM 150BAF ...
Страница 8: ...8 b KM 150BWF ...
Страница 14: ...14 Control Products HOSHIZAKI001 Board ...
Страница 15: ...15 Control Products HOS 001A Board ...
Страница 23: ...23 TEST PROGRAM OF ALPINE CONTROLLER BOARD ...
Страница 25: ...25 III TECHNICAL INFORMATION 1 WATER CIRCUIT AND REFRIGERANT CIRCUIT a KM 150BAF ...
Страница 26: ...26 b KM 150BWF ...
Страница 30: ...30 4 PERFORMANCE DATA a KM 150BAF Air cooled ...
Страница 31: ...31 b KM 150BWF Water cooled ...