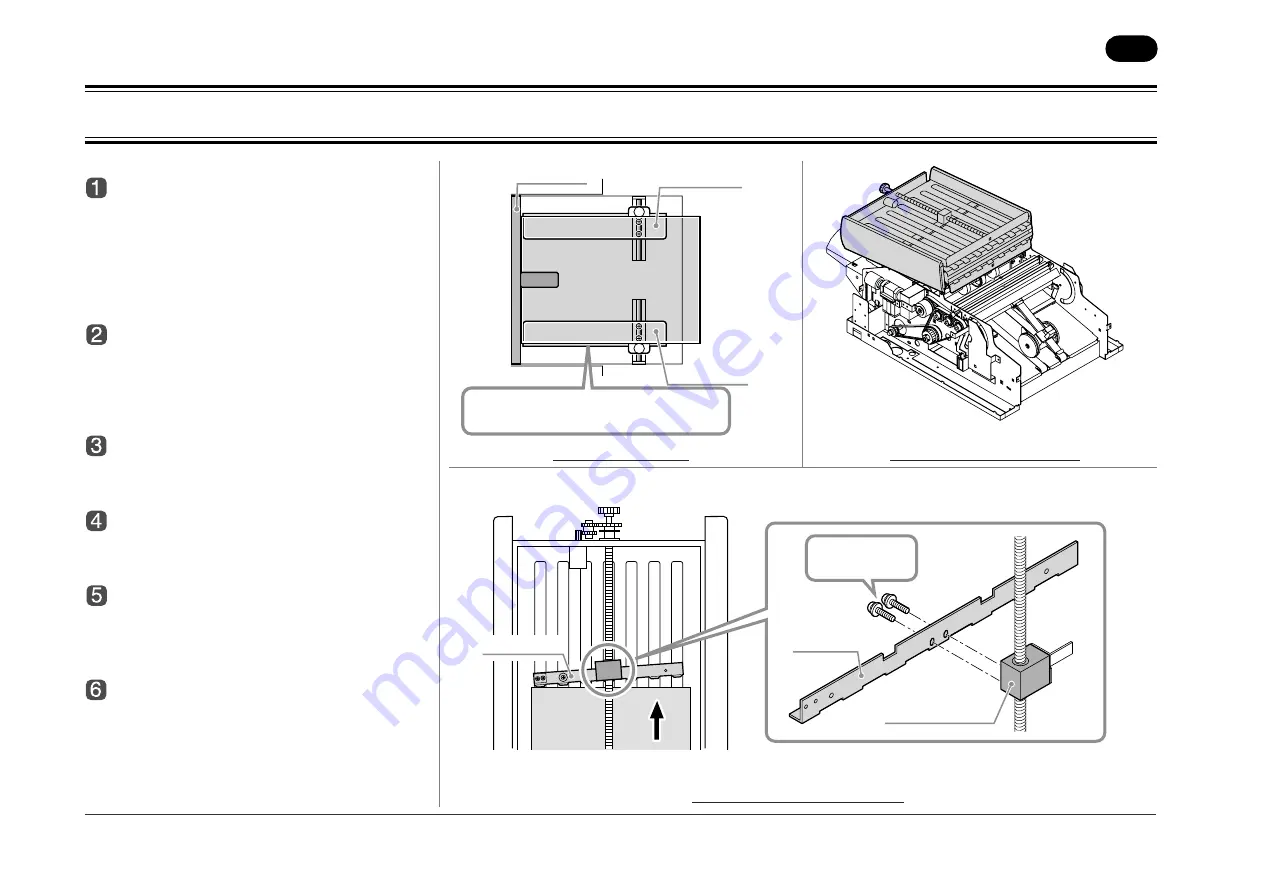
3-6
3: Adjusting and Checking Procedures
3-5
Buckle Chute Stopper Level Adjustment
Check the sheet guides.
- Place a sheet so that the sheet edge touches the
front stop and check that the sheet guides are
parallel to the sheet. (Fig.1)
If the sheet guides are askew, see Section 3-1:
Sheet Guides Right Angle and Parallel Adjustment
and correct the sheet guides angle.
Remove the cover on buckle chute
section.
- Lay down the buckle chute section and loosen the
fixing screws at the bottom of the buckle chute.
(Fig.2)
Remove the rear cover.
- In later procedure, the motor belt will be driven
manually to feed a sheet.
Load a sheet on the feed table.
- Load a square sheet and place the sheet guides on
both side.
Feed a sheet.
- Drive the motor belt manually and feed a sheet.
- Stop the belt at position where the sheet front edge
touches the stopper.
Adjust the stopper angle.
- Adjust the stopper angle within the play made by
the two fixing screws so that the stopper is parallel
to the sheet. (Fig.3)
Fig. 2 Remove the Covers
Fig. 3 Stopper Fixing Section
Fig. 1 Sheet Guide
Front Stop
No gap between the sheet guide and the
sheet that is aligned with the front stop.
Sheet Guide
Sheet Guide
Sheet
Stopper
Slide Guide
Stopper
Two screws
adjust the tilt.
Содержание PF-P330
Страница 2: ......
Страница 9: ...1 1 1 1 Mechanism Mechanism 1 Mechanism ...
Страница 21: ...2 2 1 2 Service Mode Service Mode 2 Service Mode ...
Страница 24: ...2 4 2 Service Mode This page is intentionally left blank ...
Страница 36: ...3 12 3 Adjusting and Checking Procedures This page is intentionally left blank ...
Страница 37: ...4 4 1 4 Mechanical Troubleshooting Mechanical Troubleshooting 4 Mechanical Troubleshooting ...
Страница 51: ...5 5 1 5 Folding Quality Troubleshooting Folding Quality Troubleshooting 5 Folding Quality Troubleshooting ...
Страница 58: ...5 8 5 Folding Quality Troubleshooting This page is intentionally left blank ...
Страница 59: ...6 6 1 6 Electrical Circuit Electrical Circuit 6 Electrical Circuit ...
Страница 70: ...6 12 6 Electrical Circuit This page is intentionally left blank ...