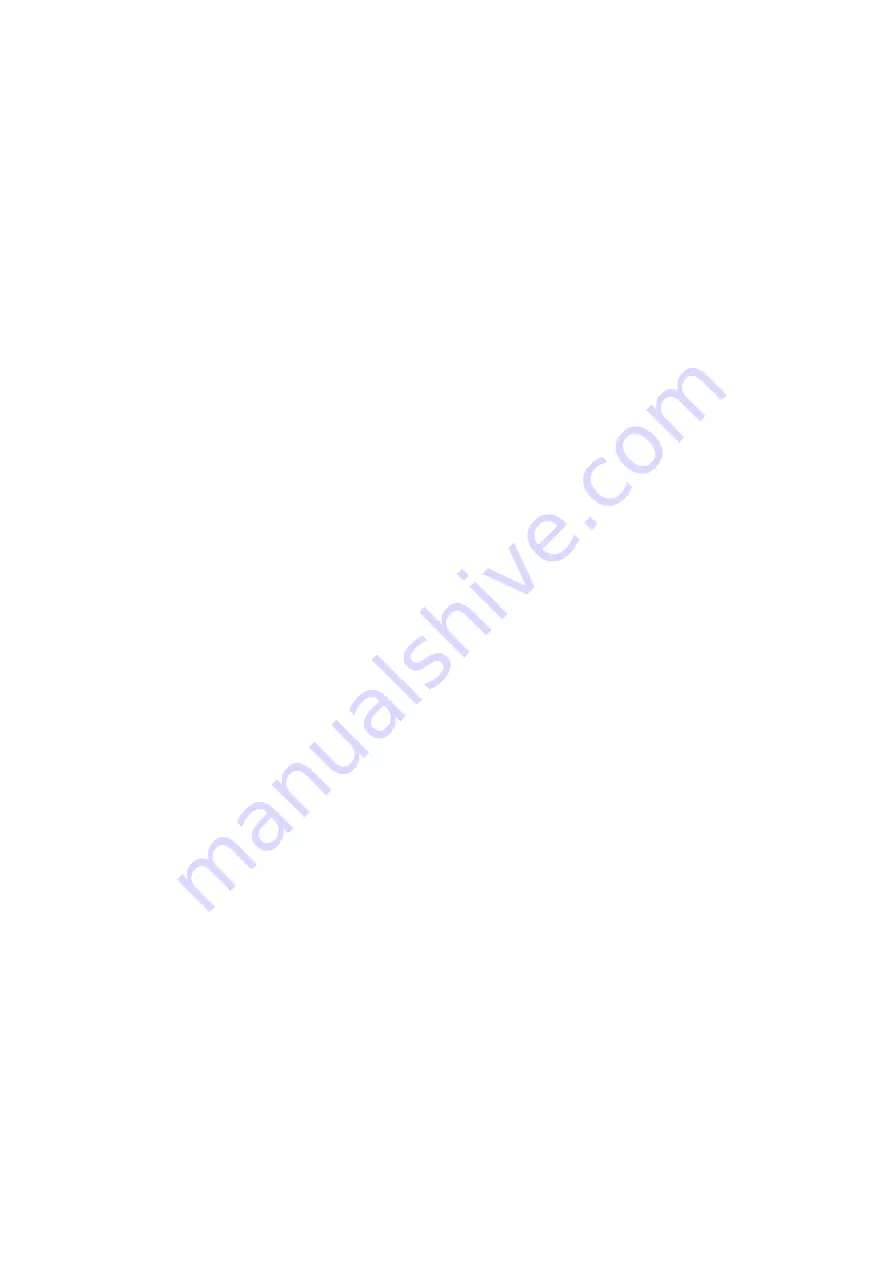
- 11 -
8
. Instructions for Handling
1) Check that the piping does not leak, and sufficiently purge the inside of the piping.
2) To keep the control valve travel correct, use filters to remove particles in the liquid material, or
clean the piping. (When filters are used, 0.01-
m-mesh metal filters or 0.05-
m-mesh
membrane filters are recommended.)
3) The maximum operating temperature of the mixing valve is 140
C, and that of the vaporizer is
200
C. Avoid baking or using these units at temperatures exceeding the maximum working
temperatures.
4) High voltage (approx. 120 V) is used to drive the control valve. To prevent electric shock,
never remove the main unit case while power is on the unit.
5) When selecting temperature regulators for MV and heating piping, check the sensor type and
heater capacity.
6) Since MV is normal open, it is recommended to provide a normal closed type pneumatic valve
on the liquid phase line and on the gas phase line (before the chamber) against power
interruption and emergency stop.
7) Before starting vaporization, sufficiently warm up MV (for more than 30 minutes after the
temperature stabilizes).
8) Since MV and its heating piping are insulated, they become hot. Do not install them near
objects that may be affected or disordered by heat.
9) Since MV and its heating piping become hot, never put combustible materials or ignitable
objects near them.
10) Never touch MV or its heating piping directly with hand after they are heated. Doing so
can burn your hands. When it is necessary to touch them with hand for maintenance,
turn off the temperature regulators of MV, and wait until the units cool off.
11) The temperature of each of the Mixing valve and the vaporizer of MV is controlled by the
temperature regulator. Therefore, thermocouple and heater wires are necessary for
each regulator. Wire the regulator correctly, checking the marking on the cables. If the
regulator is wired improperly, the temperature may be out of control, and the equipment
may not operate correctly.
12) Do not install MV where it is exposed directly to wind from a fan.
13) Supply the liquid material to MV while the carrier gas is flowing in MV.
14) The control valve travel changes with the set temperature of the main unit. To prevent
malfunction due to change in valve travel, keep the MV set temperature within the specified
temperature
10
C. The maximum operating temperatures of the mixing valve and the vaporizer
are 140
C and 200
C. The specified temperature is shown on the label at the back of the
product.
15) Before dismantling the equipment for repair or overhaul, purge the equipment to
discharge the liquid from the main unit. If it is purged incompletely, vapor gas may leak
when it is dismantled. Dismantle it while ventilating the area.
16) Before returning the equipment to us for repair or overhaul, purge it sufficiently in the same
manner as stated in (15) to discharge the liquid from the main unit. If the liquid is left in the unit,
it may leak or react during transportation. In this case, it is difficult to investigate the causes of
trouble. If the liquid is left in the unit when the equipment is returned, there is a possibility that it
cannot be repaired or overhauled.
17) The response speed from the liquid flow meter(LF or XF) to be combined with the vaporizer has
been adjusted on the Liquid flow meter(LF or XF) in the single state. The response speed has
not been adjusted for MV to be actually used. Therefore, after installing the Liquid flow
meter(LF or XF), it is necessary to adjust the speed of response of liquid flow rate.