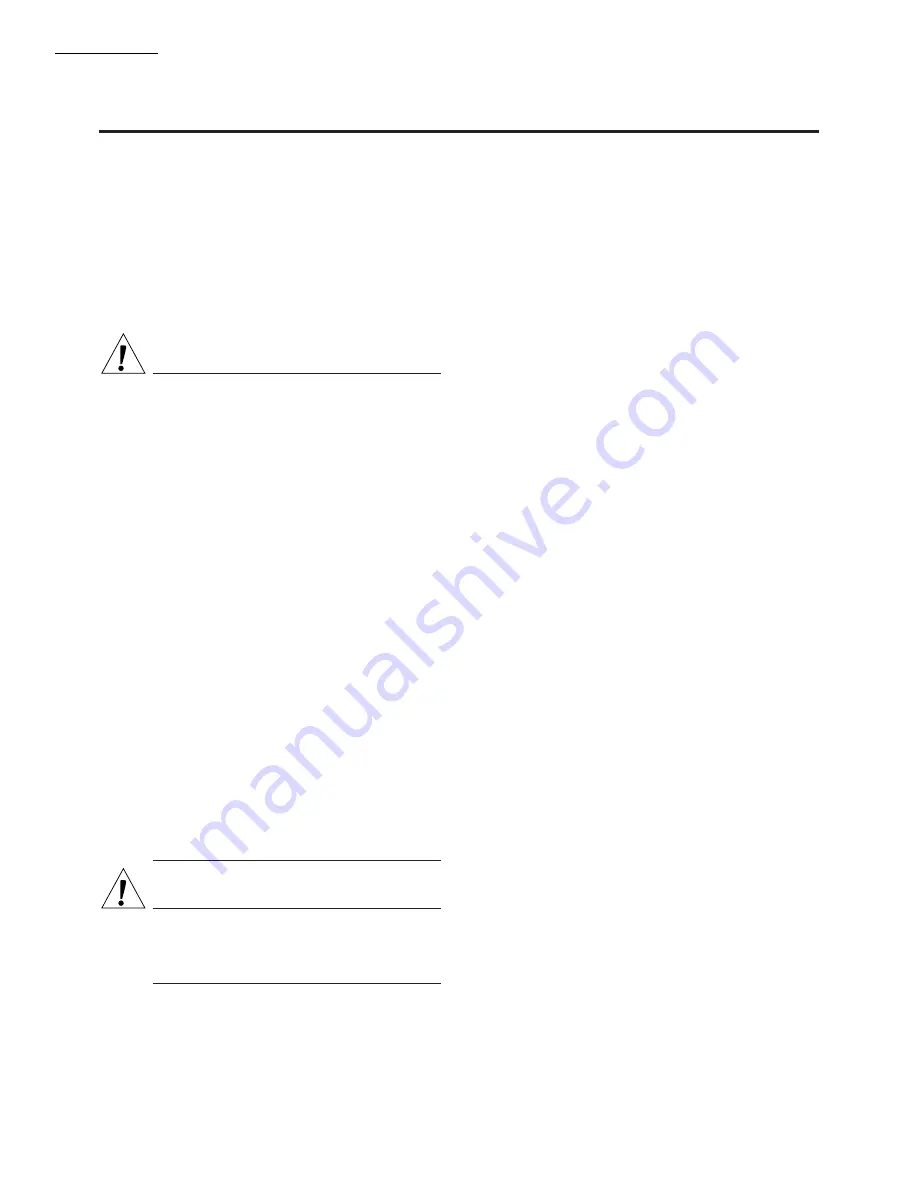
68-0150
4
VR8405
INSTALLATION
Installation
WHEN INSTALLING THIS PRODUCT…
1. Read these instructions carefully. Failure to follow
them could damage the product or cause a hazardous
condition.
2. Check the ratings given in the instructions and on
the product to make sure the product is suitable for your
application.
3. The installer must be a trained, experienced service
technician.
4. After installation is complete, use these instructions
to check out product operation.
WARNING
FIRE OR EXPLOSION HAZARD
CAN CAUSE PROPERTY DAMAGE,
SEVERE INJURY, OR DEATH.
Follow these warnings exactly:
1. Disconnect power supply before wiring to pre-
vent electrical shock or equipment damage.
2. To avoid dangerous accumulation of fuel gas,
turn off gas supply at the appliance service valve
before starting installation, and perform the Gas
Leak Test after completion of installation.
3. Always install sediment trap in gas supply line
to prevent contamination of gas control.
4. Do not force the gas control knobs. Use only
your hand to turn the gas control knobs. Never
use any tools. If the gas control knobs will not
operate by hand, call a qualified service techni-
cian to replace the entire gas control. Force or
attempted repair can result in fire or explosion.
5. Replace entire VR8405 when doing a product
replacement. Do not replace individual valve
components.
6. For complete device shutoff, both gas control
knobs must be in the OFF position. For complete
appliance shutoff, turn off the upstream appli-
ance valve and disconnect the power supply.
7. Use the wiring harness for connecting the en-
tire gas control to the ignition control module.
Do not remove the harness or modify the wires
in the harness.
CAUTION
Never apply a jumper across or short the valve
leadwires. This can burn out the heat anticipator
in the thermostat or damage the electronic direct
ignition (DI) module.
IMPORTANT: This entire gas control is shipped with
protective seals over inlet and outlet tappings. Do
not remove seals until ready to connect piping.
Follow the appliance manufacturer instructions if avail-
able; otherwise, use the instructions provided below.
INSTALL BUSHINGS ON ENTIRE GAS CONTROL
1. Remove seals over gas control inlet or outlet.
2. Apply moderate amount of good quality pipe com-
pound to bushing, leaving two end threads bare. On an LP
gas installation, use compound resistant to LP gas. See
Fig. 3. Do not use Teflon tape.
3. Insert bushing in entire gas control and thread pipe
carefully into bushing until tight.
CHOOSE GAS CONTROL LOCATION
Locate the gas control in the appliance vestibule on the
gas manifold. In replacement applications, locate the entire
gas control in the same location as the old gas control.
Do not locate the entire gas control where it can be
affected by steam cleaning, high humidity, dripping water,
corrosive chemicals, dust or grease accumulation, or exces-
sive heat. To safeguard proper operation, follow these
guidelines:
• Locate entire gas control in a well-ventilated area.
• Mount entire gas control high enough above the cabi-
net bottom to avoid exposure to flooding or splashing
water.
• Make sure the ambient temperature does not exceed
the ambient temperature ratings for the entire gas
control.
• Cover entire gas control when appliance is cleaned
with water, steam, or chemicals or to avoid dust and
grease accumulation.
• Avoid locating gas control where exposure to corro-
sive chemical fumes or dripping water is possible.
Install Appliance Shutoff Valve
It is recommended that an appliance shutoff valve be
installed upstream of the VR8405. Refer to the instructions
provided by the valve manufacturer.
Install Piping to Gas Control
All piping must comply with local codes and ordinances
or with the National Fuel Gas Code (ANSI Z223.1 NFPA
No. 54), whichever applies. Tubing installation must com-
ply with approved standards and practices.
1. Use new, properly reamed pipe free from chips. If
tubing is used, make sure the ends are square, deburred and
clean. Make sure all tubing bends are smooth and without
deformation.
2. Run pipe or tubing to the gas control. If tubing is
used, obtain a tube-to-pipe coupling to connect the tubing
to the gas control.
3. Install sediment trap in the supply line to the entire
gas control. See Fig. 2.