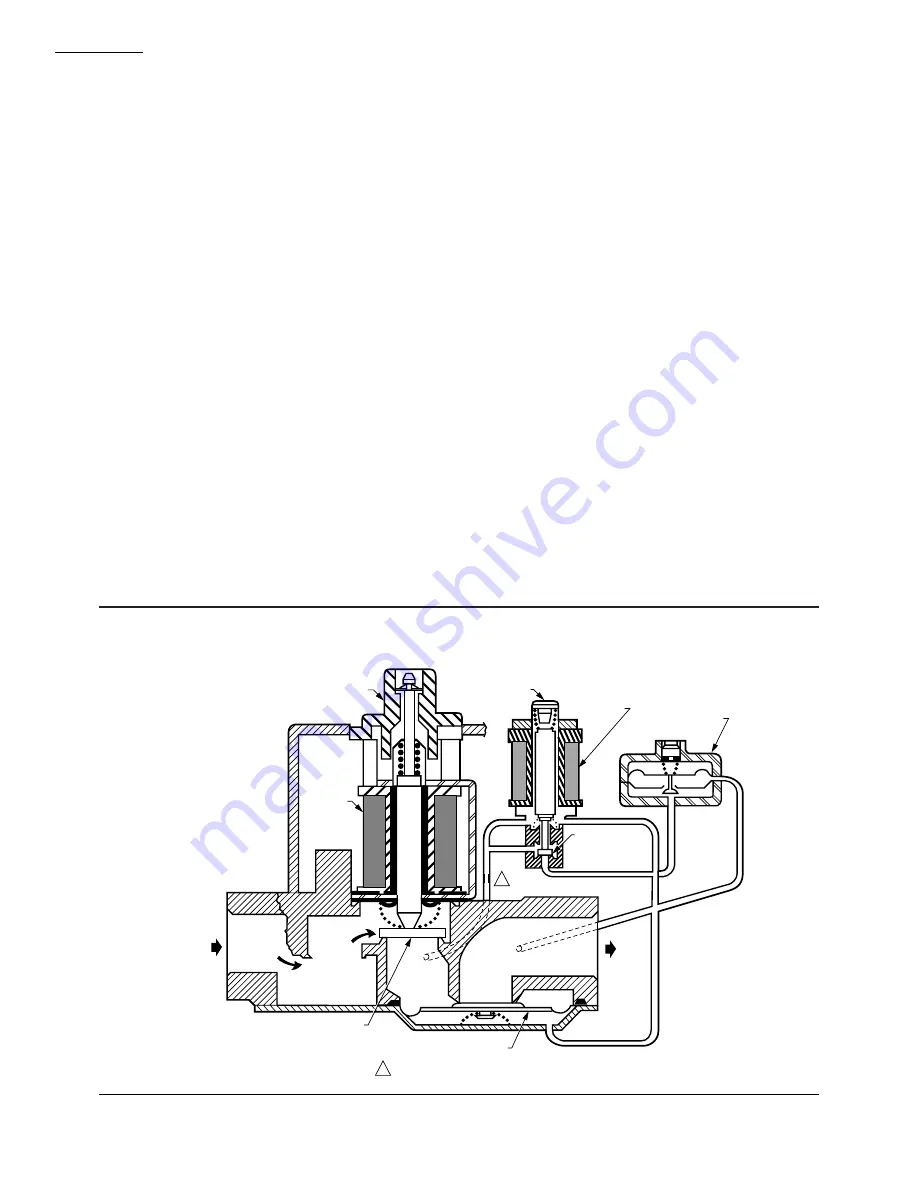
68-0150
10
VR8405
OPERATION
If main burner flame is restarted successfully, operation
continues as described above. Gas control operation is de-
scribed in more detail below.
VALVE POSITION DURING THERMOSTAT OFF
CYCLE
Each valve is positioned as shown in Fig. 8 when the:
• Gas control knob is in the ON position.
• Thermostat is not calling for heat.
The first automatic valve is closed. The second automatic
valve operator is de-energized, closing the channel to the
pressure regulator, and opening a channel to the underside
of the second automatic valve operator valve diaphragm.
The combination of spring pressure under the second auto-
matic valve diaphragm and lack of outlet pressure hold the
diaphragm firmly closed. Main burner gas flow is blocked
by both valves.
WHEN THERMOSTAT CALLS FOR HEAT
When the thermostat calls for heat, the DI module gener-
ates a spark at the main burner and the first automatic valve
and second automatic valve operators are energized, Fig. 9.
The first automatic valve opens, and the second automatic
valve operator valve disc is lifted off its seat. This diverts
gas flow from the second automatic valve diaphragm, and
causes a reduction of pressure on the underside of this
diaphragm. The reduced pressure on the bottom of the auto-
matic valve diaphragm repositions the diaphragm down-
ward, away from the valve seat, allowing main burner gas
flow.
Standard-Opening Pressure Regulation (VR8405M)
During the ON cycle, the servo pressure regulator pro-
vides close control of outlet pressure, even if inlet pressure
and flow rate vary widely. Any outlet pressure change is
immediately reflected back to the pressure regulator dia-
phragm, which repositions to change the flow rate through
the regulator valve and, thus, through the automatic valve.
If outlet pressure begins to rise, the pressure regulator
diaphragm moves slightly higher, allowing less gas flow to
the gas control outlet. This increases gas pressure under the
automatic valve diaphragm and repositions the valve disc
closer to the seat. Thus, flow of gas through the second
automatic valve is reduced, and outlet pressure falls to the
desired level.
If outlet pressure begins to fall, the pressure regulator
diaphragm moves slightly lower, allowing more gas flow to
the gas control outlet. This decreases gas pressure under the
second automatic valve diaphragm and repositions the
valve disc further from the seat. Thus, gas flow through the
second automatic valve is increased, and outlet pressure
rises to the desired level.
Slow-Opening Pressure Regulation (VR8405H)
Slow-opening gas controls function the same as stan-
dard-opening models except that when the thermostat calls
for heat, the second automatic valve opens gradually. Open-
ing is slowed because a flow restrictor in the passage from
the second automatic operator slows the rate at which gas
pressure is reduced under the second automatic valve dia-
phragm after the second automatic operator opens. Outlet
FIRST
AUTOMATIC
VALVE
SOLENOID
CONTROL
KNOB
GAS
CONTROL
INLET
SECOND AUTOMATIC
VALVE OPERATOR
SECOND
AUTOMATIC
OPERATOR
SOLENOID
SECOND
AUTOMATIC
OPERATOR
VALVE DISC
SERVO PRESSURE
REGULATOR
GAS
CONTROL
OUTLET
SECOND AUTOMATIC
VALVE DIAPHRAGM
FIRST AUTOMATIC VALVE
NOTE: AUTOMATIC VALVE OPERATOR AND SERVO
PRESSURE REGULATOR SHOWN OUTSIDE GAS
CONTROL FOR EASE IN TRACING GAS FLOW.
SLOW-OPENING GAS CONTROL HAS A GAS FLOW RESTRICTOR IN THIS PASSAGE.
M9114
1
1
Fig. 8—Position of gas control components during thermostat Off cycle. Both valves positioned the
same; one valve shown for simplicity.