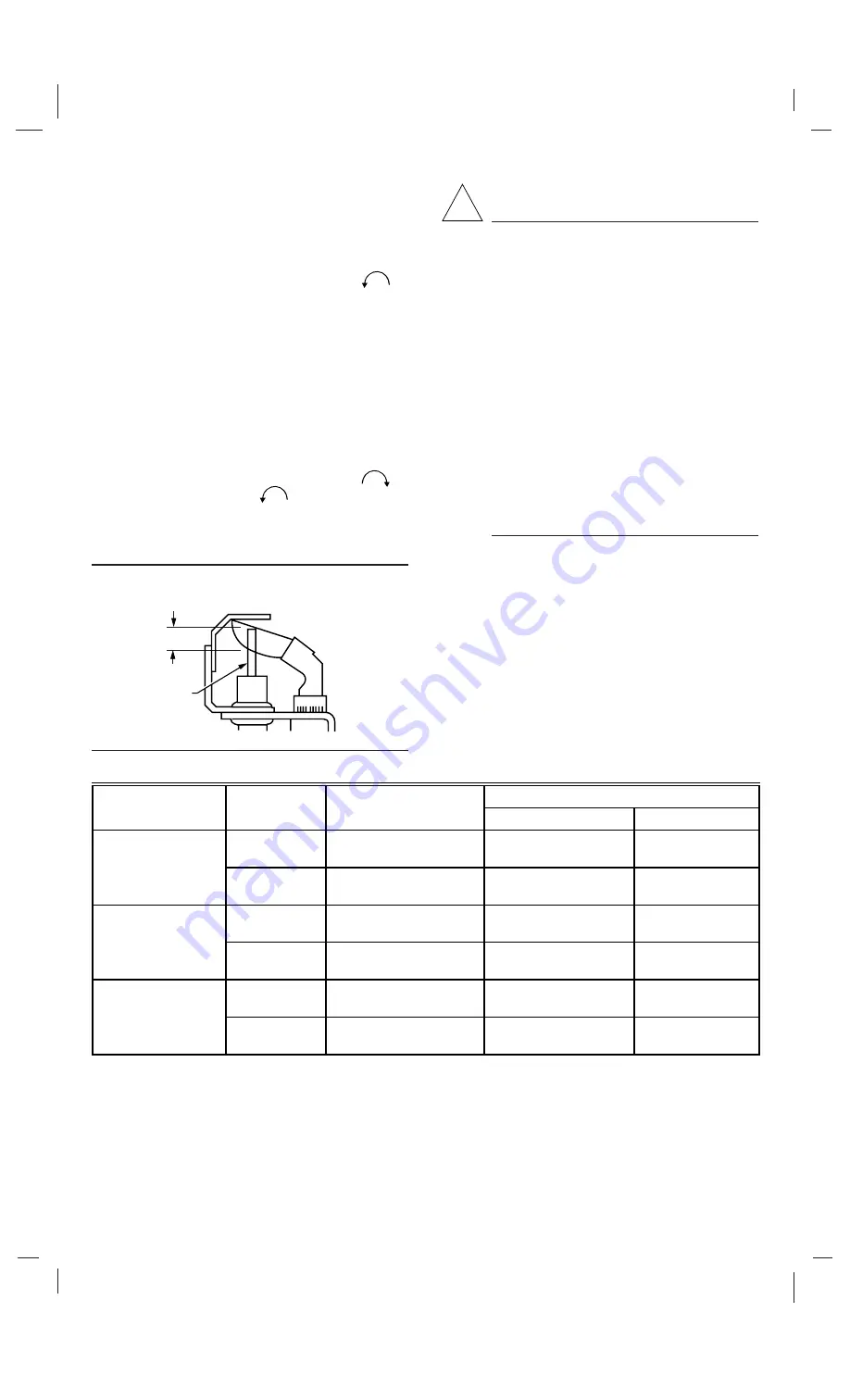
69-0814—1
6
4. With the main burner in operation, paint all pipe
joints and gas control inlet and outlet with a rich soap and
water solution.
5. If another gas leak is detected, tighten pipe connections.
6. Replace the part if gas leak cannot be stopped.
TURN ON GAS CONTROL
Rotate the gas control knobs counterclockwise
to
ON.
TURN ON MAIN BURNER
Follow instructions provided by appliance manufac-
turer or turn up thermostat to call for heat.
ADJUST THE PILOT BURNER FLAME
The pilot flame should envelop 3/8 to 1/2 inch [10 to
13 millimeters] of the igniter-sensor tip. Refer to Fig. 8. To
adjust the pilot flame.
1. Remove the pilot adjustment cover screw. Refer to
Fig. 3.
2. Turn the inner adjustment screw clockwise
to
decrease or counterclockwise
to increase the pilot
flame.
3. To prevent gas leakage replace the cover screw after
adjustment.
Fig. 8—Proper flame adjustment.
CHECK GAS INPUT TO MAIN BURNER
CAUTION
1. Do not exceed the input rating stamped on the
appliance nameplate, or manufacturer recom-
mended burner orifice pressure for the size
orifice(s) used. Make certain the primary air
supply to the main burner is properly adjusted
for complete combustion (refer to the appli-
ance manufacturer instructions).
2. WHEN CHECKING GAS INPUT BY
CLOCKING THE GAS METER:
• Make sure that the only gas flow through
the meter is that of the appliance being
checked.
• Make certain that other appliances are turned
off with pilot burners extinguished (or de-
duct that gas consumption from the meter
reading).
• Convert the flow rate to Btuh as described in
the Gas Controls Handbook, form 70-2602,
and compare to the Btuh input rating on the
appliance nameplate.
Standard-Opening and Slow-Opening Pressure
Regulator
1. The gas control outlet pressure should match the
manifold pressure listed on the appliance nameplate.
2. With the main burner operating, check the gas con-
trol flow rate using the meter clocking method.
3. If the desired gas flow rate is not as stamped on the
control, check the gas control inlet pressure using a ma-
nometer at the inlet pressure tap. Regulators are fixed. They
are not adjustable. If the inlet pressure is in the normal
range (refer to Table 3), replace the entire gas control.
Otherwise, take the necessary steps to provide proper gas
pressure to the gas control.
!
TABLE 3—PRESSURE REGULATOR SPECIFICATION PRESSURES IN IN. WC [kPa].
Factory Set Outlet Pressure
Model
Type of Gas
Nominal Inlet Pressure
Step
Full Rate
H (Slow-opening)
Natural
7.0 [1.7]
—
3.0 - 5.0
[0.7 - 1.2]
LP
14.0 [3.9]
—
8.0 - 12.0
[2.0 - 3.0]
M (Standard)
Natural
7.0 [1.7]
—
3.0 - 5.0
[0.7 - 1.2]
LP
14.0 [3.9]
—
8.0 - 12.0
[2.0 - 3.0]
P (Step-opening)
Natural
7.0 [1.7]
0.7, 0.9, 1.2, 1.7,
[0.17, 0.22, 0.30, 0.42]
3.0 - 5.0
[0.7 - 1.2]
LP
14.0 [3.9]
1.4, 2.5, 4.0, 5.5
[0.35, 0.62, 1.0, 1.4]
8.0 - 12.0
[2.0 - 3.0]
NOTE: Factory set outlet pressure is not field adjustable.
PROPER FLAME
ADJUSTMENT
IGNITER-
SENSOR
M3080A
3/8 TO 1/2 INCH
[10 TO 13 mm]