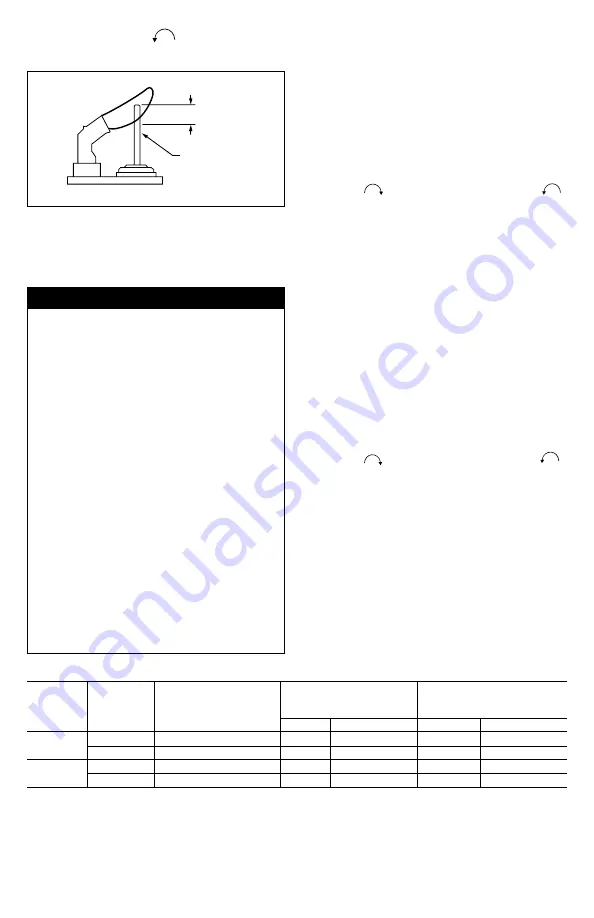
crease or counterclockwise
to increase pilot flame.
3. Always replace cover screw after adjustment and
tighten firmly to ensure proper operation.
V5306A,B Standard-Pressure Regulator
1. Check the manifold pressure listed on the appliance
nameplate. Gas control outlet pressure should match the
nameplate.
2. With main burner operating, check gas control flow
rate using the meter clocking method or pressure using a
manometer connected to the outlet pressure tap on the gas
control. Refer to Fig. 3.
3. If necessary, adjust pressure regulator to match appli-
ance rating. Refer to Tables 5 and 6 for factory set nominal
outlet pressure and adjustment range.
a. Remove pressure regulator adjustment cap and
screw.
b. Using screwdriver, turn inner adjustment screw
clockwise
to increase or counterclockwise
to decrease gas pressure to burner.
c. Always replace cap screw and tighten firmly to
ensure proper operation.
4. If desired outlet pressure or flow rate cannot be
achieved by adjusting the control, check the control inlet
pressure using a manometer at the inlet pressure tap. If inlet
pressure is in normal range (refer to Tables 6 and 7),
replace the control. Otherwise, take the necessary steps to
provide proper gas pressure on the control.
V5307A,B Step-Opening Pressure Regulator
1. Check the full rate manifold pressure listed on the
appliance nameplate. Gas control full rate outlet pressure
should match this rating.
2. With main burner operating, check the control flow
rate using the meter clocking method or pressure using a
manometer connected to outlet pressure tap on the control.
Refer to Fig. 3.
3. If necessary, adjust pressure regulator to match appli-
ance rating. Refer to Tables 6 and 7 for factory set nominal
outlet pressure and adjustment range.
a. Remove pressure regulator adjustment cap screw.
b. Using a screwdriver, turn inner adjustment screw
clockwise
to increase or counterclockwise
to decrease gas pressure to burner.
c. Always replace cap screw and tighten firmly to
ensure proper operation.
4. If desired outlet pressure or flow rate cannot be
achieved by adjusting the control, check the inlet pressure
using a manometer at inlet pressure tap or upstream of the
gas control. If inlet pressure is in the normal range (refer to
Tables 6 and 7), replace the existing control. Otherwise,
take the necessary steps to provide proper gas pressure to
the control.
5. Carefully check burner lightoff at step pressure. Make
sure burner lights smoothly and without flashback to orifice.
Make sure all ports remain lit. Cycle burner several times,
allowing at least 30 seconds between cycles for regulator to
resume step function. Repeat after allowing burner to cool.
Readjust full rate outlet pressure if necessary to improve
lightoff characteristics.
TABLE 6—PRESSURE REGULATOR SPECIFICATION PRESSURES IN IN. WC.
OUTLET PRESSURE
NOMINAL
SETTING
TYPE
NOMINAL INLET
FACTORY SETTING
RANGE
MODEL
OF GAS
PRESSURE RANGE
Step
Full Rate
Step
Full Rate
A,M
NATURAL
5.0-7.0
—
3.5
—
3-5
LP
12.0-14.0
—
11.0
—
8-12
C,P
NATURAL
5.0-7.0
0.9
3.5
None
3-5
LP
12.0-14.0
2.2
11.0
None
8-12
Fig. 7—Proper flame adjustment.
TURN ON MAIN BURNER
Follow appliance manufacturer instructions or adjust
thermostat to call for heat.
CHECK AND ADJUST GAS INPUT TO MAIN BURNER
CAUTION
1. Do not exceed input rating stamped on appliance
nameplate, or manufacturer’s recommended
burner orifice pressure for size orifice(s) used.
Make certain primary air supply to main burner is
properly adjusted for complete combustion. Fol-
low appliance manufacturer instructions.
2. IF CHECKING GAS INPUT BY CLOCKING GAS
METER:
•
Ensure that the only gas flow through the meter
is that of the appliance being tested.
•
Ensure other appliances are turned off and
their pilot burners are extinguished (or deduct
their gas consumption from the meter reading).
•
Convert flow rate to Btuh as described in the
Gas Controls Handbook (form number 70–
2602) and compare to Btuh input rating on
appliance nameplate.
3. IF CHECKING GAS INPUT WITH MANOMETER:
•
Ensure gas control knob is in PILOT position
before removing outlet pressure tap plug to
connect manometer (pressure gauge).
•
Turn gas control knob back to PILOT when
removing gauge and replacing plug.
•
Shut off gas supply at the appliance service
valve or, for LP gas, at the gas tank before
removing outlet pressure tap plug and before
disconnecting manometer and replacing outlet
pressure tap plug.
•
Perform Gas Leak Test at inlet pressure tap
plug.
5
95-6996—10
M3086B
PROPER FLAME
ADJUSTMENT
3/8 TO 1/2 IN.
(10 TO 13 MM)
THERMOCOUPLE