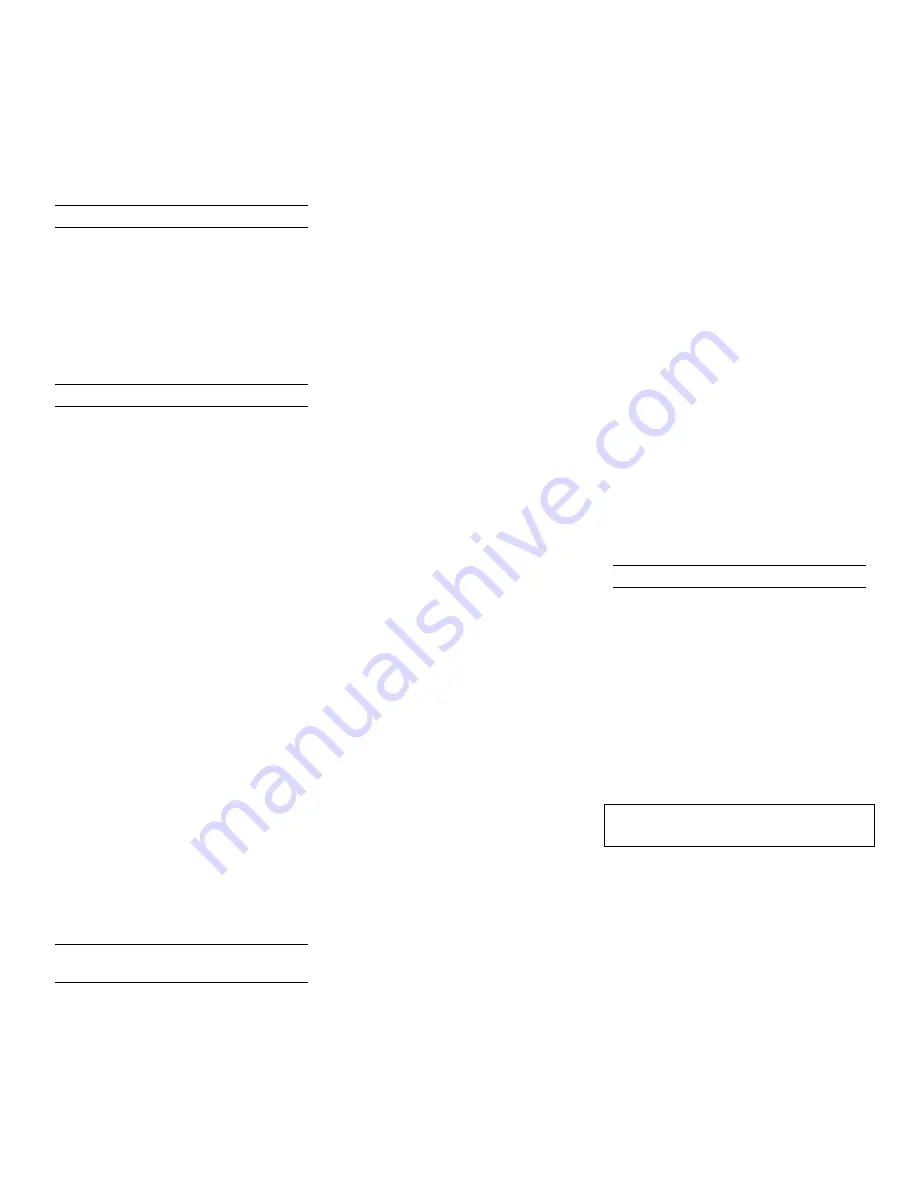
23
Appendix C Calibration Frequency Recommendation
One of the most common questions
that we are asked at Honeywell
Analytics is:
“How often should I
calibrate my gas detector?”
Sensor Reliability and Accuracy
Today’s sensors are designed to
provide years of reliable service. In
fact, many sensors are designed so
that with normal use they will only lose
5% of their sensitivity per year or 10%
over a two-year period. Given this, it
should be possible to use a sensor for
up to two full years without significant
loss of sensitivity.
Verification of Accuracy
With so many reasons why a sensor
can lose sensitivity and given the fact
that dependable sensors can be key to
survival in a hazardous environment,
frequent verification of sensor
performance is paramount.
There is only one sure way to verify
that a sensor can respond to the gas
for which it is designed. That is to
expose it to a known concentration of
target gas and compare the reading
with the concentration of the gas. This
is referred to as a “bump” test. This test
is very simple and takes only a few
seconds to accomplish.
The safest
course of action is to do a “bump”
test prior to each day’s use.
It is not
necessary to make a calibration
adjustment if the readings fall between
90%* and 120% of the expected value.
As an example, if a CO sensor is
checked using a gas concentration of
50 PPM it is not necessary to perform a
calibration unless the readings are
either below 45 PPM or above 60 PPM.
*The Canadian Standards
Association (CSA) requires
combustible gas sensors to undergo
calibration when the displayed value
during a bump test fails to fall
between 100% and 120% of the
expected value for the gas.
Lengthening the Intervals between
Verification of Accuracy
We are often asked whether there are
any circumstances in which the period
between accuracy checks may be
lengthened.
Honeywell Analytics is not the only
manufacturer to be asked this question!
One of the professional organizations
to which Honeywell Analytics belongs
is the Industrial Safety Equipment
Association (ISEA). The “Instrument
Products” group of this organization
has been very active in developing a
protocol to clarify the minimum
conditions under which the interval
between accuracy checks may be
lengthened.
A number of leading gas detection
equipment manufacturers have
participated in the development of the
ISEA guidelines concerning calibration
frequency. Honeywell Analytics’s
procedures closely follow these
guidelines.
If your operating procedures do not
permit daily checking of the sensors,
Honeywell Analytics recommends the
following procedure to establish a safe
and prudent accuracy check schedule
for your Honeywell Analytics
instruments:
1.
During a period of initial use of at
least 10 days in the intended
atmosphere, check the sensor
response daily to be sure there is
nothing in the atmosphere that is
poisoning the sensor(s). The
period of initial use must be of
sufficient duration to ensure that
the sensors are exposed to all
conditions that might have an
adverse effect on the sensors.
2.
If these tests demonstrate that it is
not necessary to make
adjustments, the time between
checks may be lengthened. The
interval between accuracy
checking should not exceed 30
days.
3.
When the interval has been
extended the toxic and
combustible gas sensors should
be replaced immediately upon
warranty expiration. This will
minimize the risk of failure during
the interval between sensor
checks.
4.
The history of the instrument
response between verifications
should be kept. Any conditions,
incidents, experiences, or
exposure to contaminants that
might have an adverse effect on
the calibration state of the sensors
should trigger immediate re-
verification of accuracy before
further use.
5.
Any changes in the environment in
which the instrument is being
used, or changes in the work that
is being performed, should trigger
a resumption of daily checking.
6.
If there is any doubt at any time as
to the accuracy of the sensors,
verify the accuracy of the sensors
by exposing them to known
concentration test gas before
further use.
Gas detectors used for the detection of
oxygen deficiencies, flammable gases
and vapors, or toxic contaminants must
be maintained and operated properly to
do the job they were designed to do.
Always follow the guidelines provided
by the manufacturer for any gas
detection equipment you use!
If there is any doubt regarding your gas
detector's accuracy, do an accuracy
check! All it takes is a few moments to
verify whether or not your instruments
are safe to use.
One Button Auto Calibration
While it is only necessary to do a
“bump” test to ensure that the sensors
are working properly, all current
Honeywell Analytics gas detectors offer
a one-button auto calibration feature.
This feature allows you to calibrate a
Honeywell Analytics gas detector in
about the same time as it takes to
co
mplete a “bump” test. The use of
automatic bump test and calibration
stations can further simplify the tasks,
while automatically maintaining
records.
Don't take a chance with your life.
Verify accuracy frequently!
Please read also Honeywell Analytics’s
application note:
AN20010808 “Use of
‘equivalent’ calibration gas mixtures”
.
This application note provides
procedures to ensure safe calibration of
LEL sensors that are subject to silicone
poisoning.
Содержание ToxiPro CO
Страница 1: ...Reference Manual ToxiPro Single Gas Detector Part 13 264 N3 Version 4 ...
Страница 8: ...8 ...