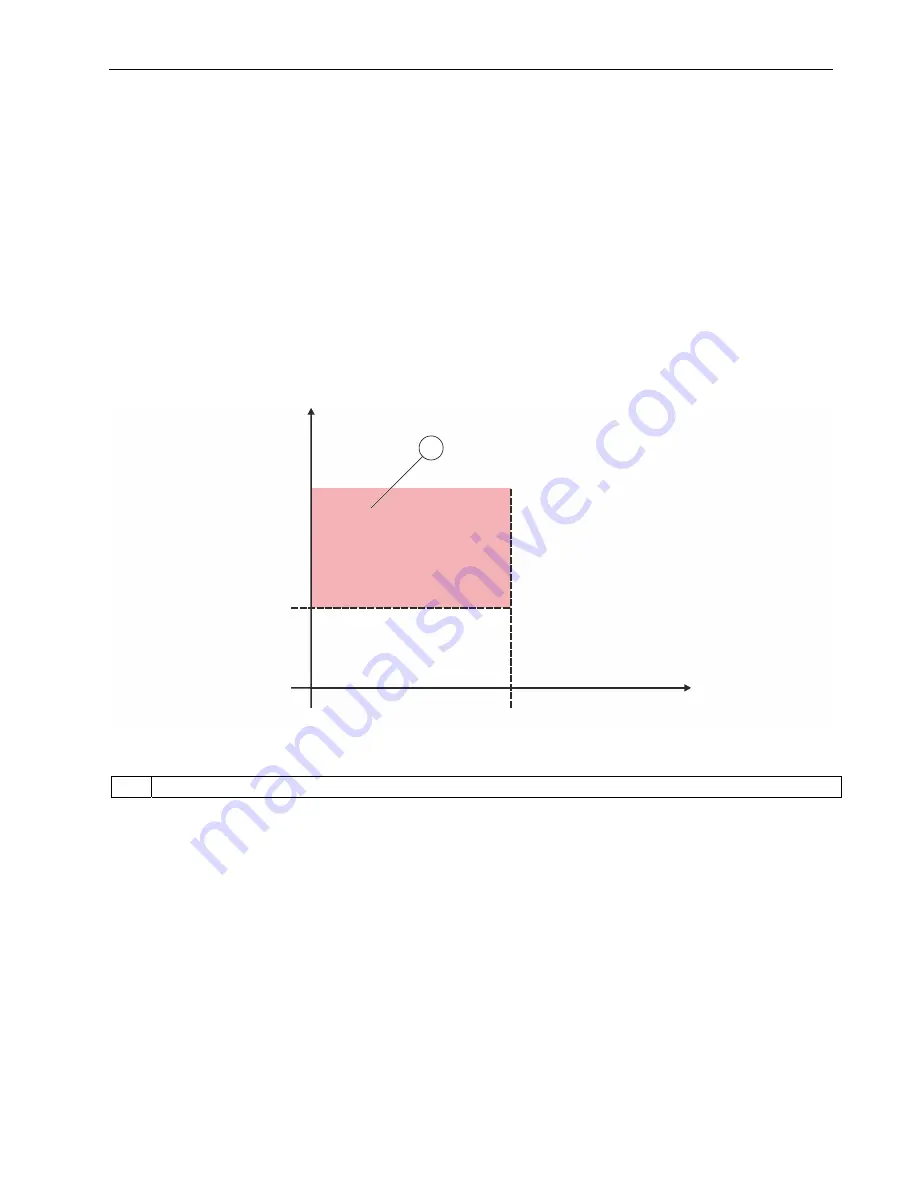
HVAC400X – APPLICATION MANUAL
129
EN2B-0417GE51 R0719
NOTE:
If you use long motor cables (max. 100 m) with small drives (≤ 1.5 kW (≤ 2.0 hp)), the motor current that
the drive measures can be much higher than the actual motor current. This is because there are
capacitive currents in the motor cable.
P3.9.11 MOTOR STALL FAULT (ID 709)
You can use this parameter to select the response of the drive to a 'Motor Stall' fault.
If the stall protection detects that the shaft of the motor is stalled, a motor stall fault occurs.
P3.9.12 STALL CURRENT (ID 710)
You can use this parameter to set the limit above which the current of the motor must stay for a stall stage to occur.
You can set the value of this parameter between 0.0 and 2*IL. For a stall status to occur, the current must be
higher than this limit. If parameter P3.1.1.7 Motor Current Limit changes, this parameter is automatically calculated
to 90% of the current limit.
NOTE:
The value of the Stall Current must be below the motor current limit.
Fig. 30. The stall characteristics settings
Legend
A.
Stall area.
P3.9.13 STALL TIME LIMIT (ID 711)
You can use this parameter to set the maximum time for a stall stage.
You can set the value of this parameter between 1.0 and 120.0 s. This is the maximum time for the stall status to
be active. An internal counter counts the stall time.
If the stall time counter value goes above this limit, the protection causes the drive to trip.
P3.9.14 STALL FREQUENCY LIMIT (ID 712)
You can use this parameter to set the limit below which the output frequency of the drive must stay for a stall stage
to occur.
A
ID710
ID712
f
I