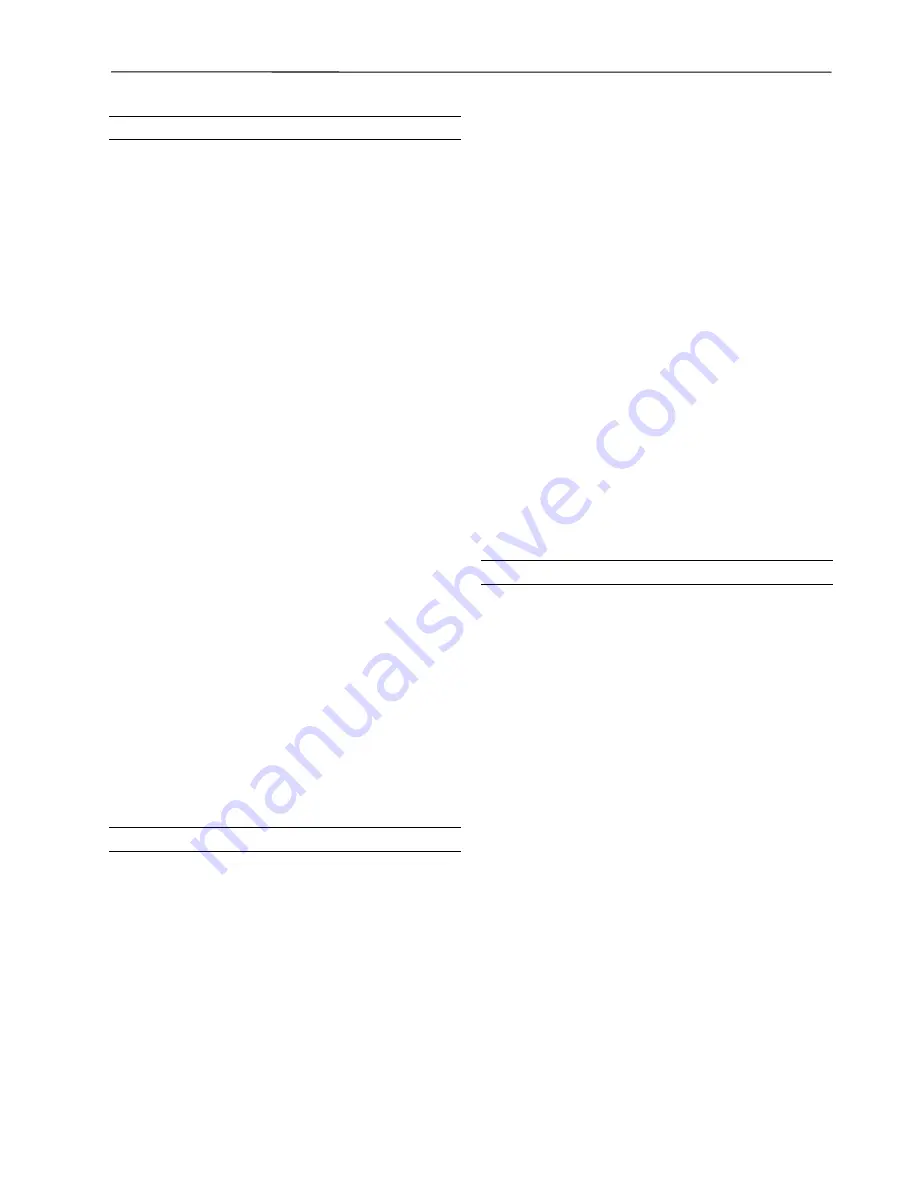
DISTRIBUTED I/O
25
EN0B-0090
Operating Modes
It is important to remember the following definitions:
Local
The term "local" refers to an operating mode in which a max.
of 16 Distributed I/O modules are connected to a single host
Excel 50/500 controller via a L
ON
W
ORKS
bus, and in which
no
other
devices co-exist on that bus. In this mode, the Dis-
tributed I/O modules are assigned to their host Excel 50/500
controller automatically, and autobinding is performed.
Shared
The term "shared" means that, aside from the host Excel 500
controller and its Distributed I/O modules,
other devices
(which may include other Excel 500 controllers with their own
Distributed I/O modules, Excel 50 or Excel 10 controllers, or
3
rd
-party devices) co-exist on the L
ON
W
ORKS
bus. In the
shared mode, autobinding may still be used for the NVs of a
maximum of 16 Distributed I/O modules assigned (manually)
exclusively to the host Excel 500 controller.
NOTE:
It is recommended that you use CARE to assign the
Distributed I/O modules to the host Excel 500 con-
troller (i.e. to enter the Distributed I/O modules'
Neuron IDs). The alternative is to assign them using
the MMI.
Open
The term "open" refers to an
interoperable
L
ON
W
ORKS
sys-
tem in which CARE has been used to generate a L
ON
M
ARK
compliant network interface file capable of providing NVs
which can be bound to other devices (which may include
other Excel 500 controllers with their own Distributed I/O
modules, Excel 50 or Excel 10 controllers, or third-party
devices). In the open operating mode, the NVs of the Dis-
tributed I/O modules exceeding 16 must be bound manually
using a L
ON
W
ORKS
network management tool (an LNS-based
tool capable of using Honeywell plug-ins is recommended).
Combined Shared and Open Mode
The
shared and the open operating modes can be in effect
simultaneously. In this case, autobinding is performed for the
NVs of a maximum of 16 Distributed I/O modules, while the
data points of additional Distributed I/O modules must be
mapped with shared NVs, and the NVs of the additional Dis-
tributed I/O modules must be bound manually (e.g. using an
LNS-based tool).
Autobinding
When Distributed I/O modules are used exclusively by
Honeywell Excel 500 controllers, it is possible to auto-
matically bind their NVs to the controller. This is referred to
as "autobinding." In autobinding, each controller on the bus
finds the Distributed I/O modules assigned to it and binds the
required NVs.
IMPORTANT:
Autobinding does not work across routers. Dis-
tributed I/O modules must be located within the
same router segment as the controller to which their
NVs are to be bound. However, autobinding is
possible across repeaters.
IMPORTANT:
The autobound NVs of a controller are not visible to
a L
ON
W
ORKS
network management tool, and there is
hence no danger that a careless user will attempt to
re-bind them. However, the NVs of the Distributed
I/O modules are visible to a L
ON
W
ORKS
network
management tool. Any attempt to re-bind the auto-
bound NVs of Distributed I/O modules will corrupt
the autobindings. In such a case, the Excel 500 con-
troller will restore the autobindings automatically, but
there will be numerous system and application
alarms as a result.
If, prior to autobinding, the Distributed I/O modules
have been accessed by a L
ON
W
ORKS
network
management tool, the modules will remain in the
“configured” mode. In this state, they cannot be
found by the controller during autobinding, and they
do not appear in the list of modules on the controller
MMI. Such modules must be decommissioned using
the L
ON
W
ORKS
network management tool, or the
L
ON
W
ORKS
service pin must be pressed for at least
three seconds.
If an Excel 500 controller in the shared/open mode is deleted
from the LonMaker project, all of its bindings will also be
deleted. In this case, the Excel 500 controller will restore all
of the autobindings (if any) automatically after 3 minutes
(provided no bindings are performed or changed in LonMaker
in the meantime), but there will be numerous system and
application alarms as a result.
Assignment
There are two methods of assigning Distributed I/O modules
to a particular Excel 500 controller.
Recommended assignment method
The Ideal approach is to know the Neuron IDs of the Dis-
tributed I/O modules when engineering the application using
CARE, thus enabling you to enter the Neuron ID during the
CARE terminal assignment. When this is done, every module
will be fully identified and assigned automatically by the Excel
500 controller after the application is downloaded.
Alternate assignment method
If the Neuron ID is not available when engineering the
application using CARE, it will be possible to correctly assign
the Distributed I/O modules to their controller(s) only after
having downloaded the application. In this case, assignment
is performed via the MMI as described in detail in the
XI581/XI582 User Guide, EN2B-0126.
IMPORTANT:
It is essential that Distributed I/O modules not be
assigned simultaneously via different MMIs. When
using the alternative assignment method, work on
only one MMI at a time so as to avoid competing
network accesses. Disregarding this will result in
contradictory and unreliable assignments. There will
be incomplete Distributed I/O module lists displayed,
and there is the danger that one controller will take
away an existent assignment from another
controller.