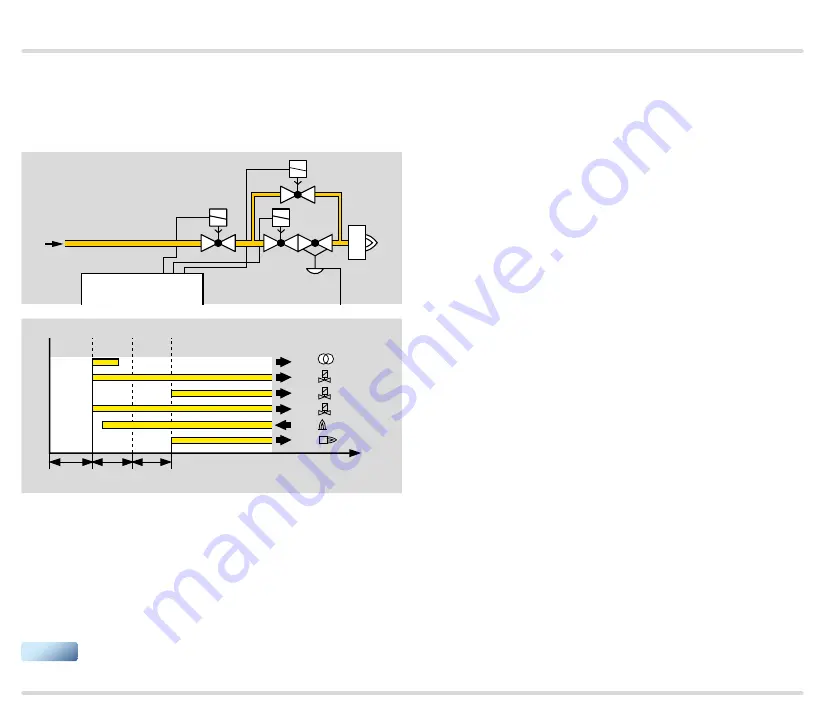
BCU 460, BCU 465 · Edition 11.19
80
Parameters
Parameter A078 = 4: two-stage burner 1. Three valves
(V1, V2 and V3) are included for a two-stage burner.
These are connected to the valve outputs (terminals 60,
61 and 62).
BCU 46x
µC
V1
V2
V3
61 62
60
52
55
54
53
56
47 48
58
03
02
01
04
2
1
3
t
t
FS1
t
SA1
t
BP
1
51
61
62
60
22
96
Valves V1 and V3 open to start the burner. The burner
is started with a limited ignition capacity using gas
valve V3. After the flame proving period t
FS1
has
elapsed, valve V2 opens to enable the 2
nd
gas stage.
If a previous version is replaced by the BCU 4, param-
eter A078 = 4 must be selected in any event.
▼