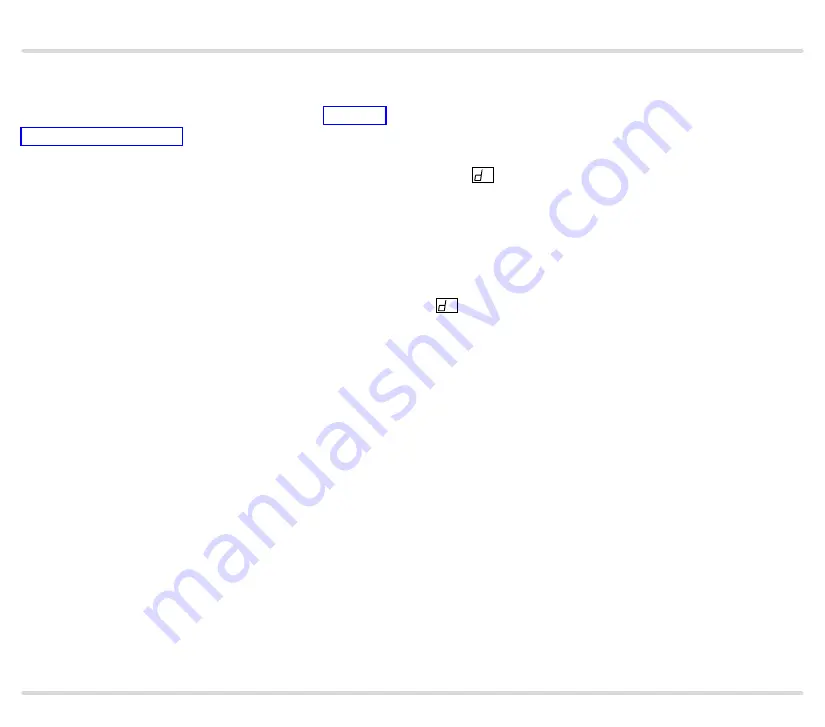
BCU 370 · Edition 01.19
53
Parameters
4 .5 .4 Air monitoring during operation
Parameter 05
If this parameter is activated, parameter 04 “Air moni-
toring during pre-purge” is also activated. This param-
eter determines whether the air supply is monitored
during burner operation.
To ensure that there is actually air pressure during burn-
er operation, the pressure can be monitored using the
air monitoring during operation function.
Parameter 05 = 0: no air monitoring during operation. A
decrease in the air pressure or a failure in air supply will
not be detected.
Parameter 05 = 1: the air pressure is monitored during
operation. During burner start (after pre-purge until
the end of the main burner safety time t
SA2
) and during
burner operation (after the end of main burner flame
proving period t
FS2
until the end of normal operation),
the air must flow and a HIGH signal must be applied to
input DL. If the HIGH signal drops, the BCU performs a
safety shut-down.
– DL signal drops during burner start.
If further start-up attempts have been parameterized
(parameter 07), a further burner start-up attempt
is made. If no further start-up attempts have been
parameterized, a fault lock-out occurs and fault mes-
sage
X
, “No air pressure on DL in program step X”, is
displayed.
– DL signal drops during burner operation.
If a restart is parameterized (parameter 08), a one-off
burner restart is attempted. If the restart option is not
activated, a fault lock-out occurs and fault message
X
, “No air pressure on DL in program step X”, is dis-
played.